Batesville Products Invests in Smart Robotics to Stay on Track with its Tech Adoption Roadmap
Batesville Products, Inc.
Case Study
Key Stats
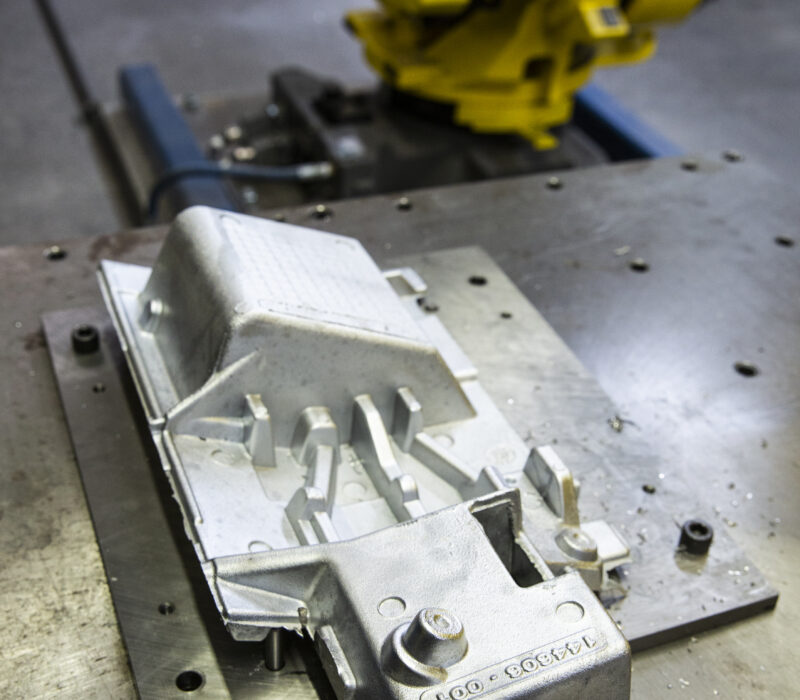
Company History
After 75 years, Batesville Products is still a one-stop-shop for full-service casting.
Established in 1946 in Lawrenceburg, Indiana, Batesville Products Incorporated (BPI) has since added a second production facility in Aurora, Indiana. After more than 75 years of operation, the family-owned, full-service aluminum-casting foundry prides itself on success mixing its small-town family atmosphere with modern technology-forward thinking. When Millard Laugle originally founded the company in 1946, he named it Batesville Ornamental Works, the name it retained until Justin Weber acquired control in the early 1960s. Weber family members remain involved in Batesville Products today, from part-time employees working their way through school to President and COO Len Weber.
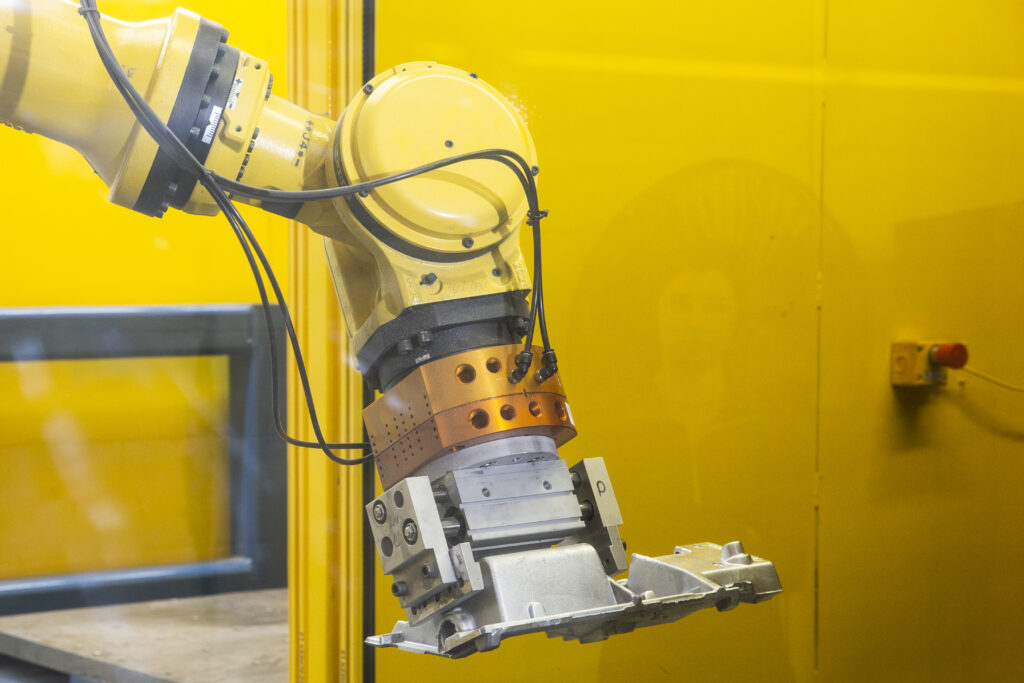
BPI now has 100,000 square feet of manufacturing space in its two locations covering 6 acres of grounds. It pours 80,000 pounds of aluminum alloy each week, employs just under 100 employees with annual revenues in the millions. It provides castings ready for direct-to-assembly lines of OEM finished products as a one-stop-shop for customers’ casting needs. Its services include permanent mold casting of aluminum and zinc, with engineering and design, tooling design and build, machining, polishing, coating and sub-assembly.
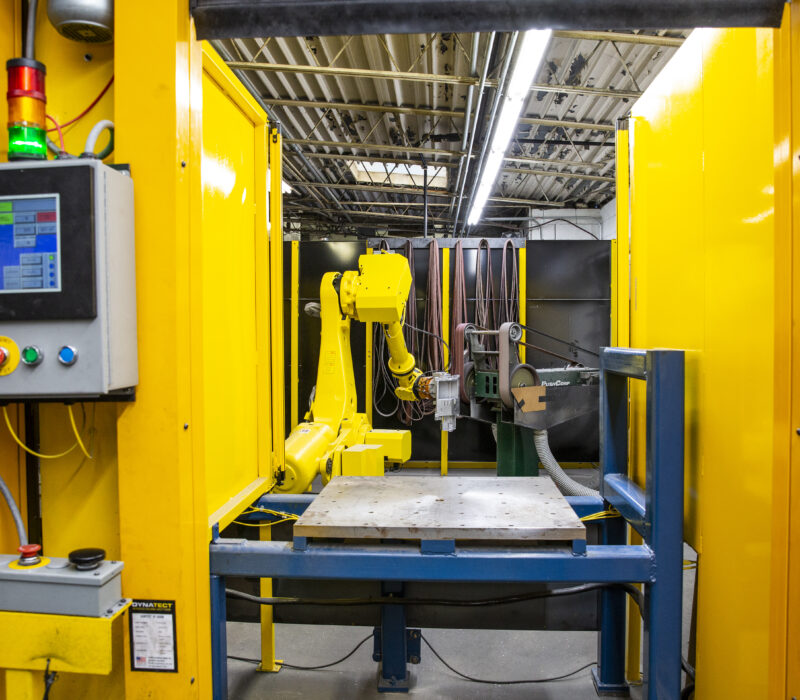
The Project
BPI implements a smart robotic polishing cell to remain cost-effective for customers and competitive in a global manufacturing landscape.
“It may not be the only answer,” said Len Weber, “but it seems the best answer to retain US-based manufacturing and the viability of BPI as a full-service casting supplier.” The smart robotic polishing cell will address BPI’s labor-intensive production tasks via a Fanuc industrial robot. The equipment is truly smart as it will integrate additional Industry 4.0 technologies, such as machine learning (ML) and artificial intelligence (AI), to provide the robot with a sense of “feel” during polishing, which is notably uncommon in most robotic applications used at the competition. As part of BPI’s overall Industry 4.0 initiative, the robotic cell will also be connected to machine monitoring software, which will collect real time data to help production managers and leadership understand the utilization and effectiveness of the cell.
The robotic polishing cell fits into BPI’s technology adoption roadmap through 2024.
“This is our first foray into robotic sanding and polishing,” Len said. “Previously all polishing was performed manually. It is consistent with our robotic saw operation that utilizes similar components and cell design, and part of our 4-year strategic CAPEX (Capital Expenditure) plan.” The robotic polishing cell was the second investment of a series of Industry 4.0 investments expected to take place between 2019 and 2024. Len explained that the strategic roadmap involves estimating the return on investment (ROI) as well as the non-financial critical aspects of each project (i.e. workforce, new business, etc.) so that further tech integration can be prioritized and planned within the 4-year strategic plan.
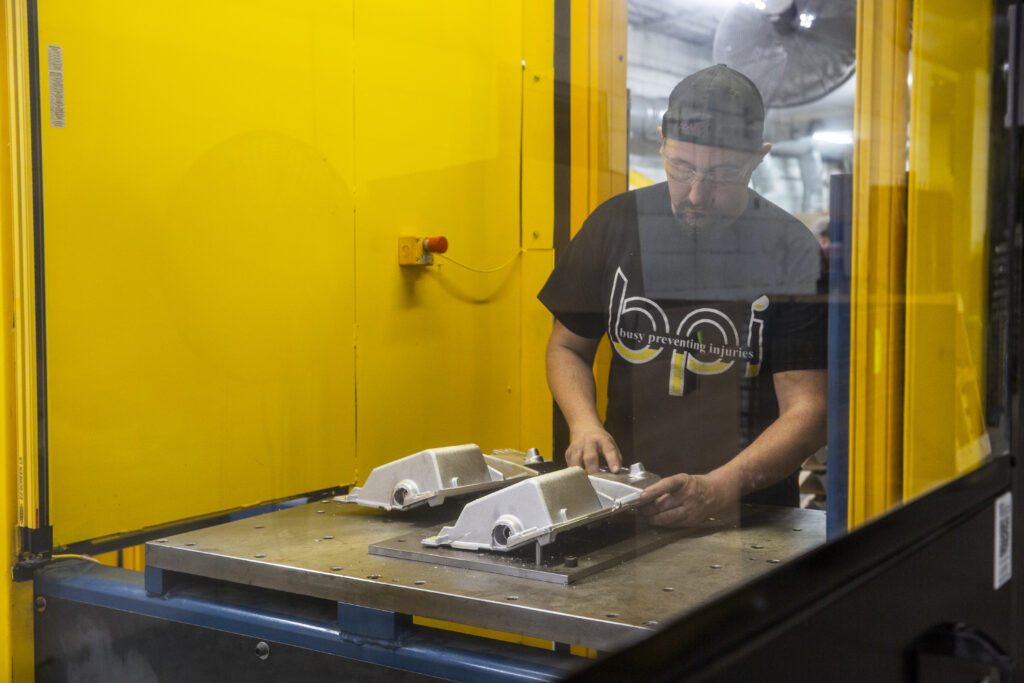
“We understand our current manual cost structure,” Len said. “We will compare that to the updated cost structure with robotic finishing. The variance will establish our ROI. Additionally, we will compare the quality of parts coming from the cell against existing production standards.” In a best-case scenario, he expected the impact of the cell in 2022 to achieve 25% ROI and 80% utilization with parts meeting production quality standards.
“Project implementation is taking slightly longer than we originally planned,” Len said. “Our project engineer left during the implementation period, and the project was delayed while the company sought a replacement.” However, despite these delays, BPI’s technology adoption goals remain ambitious. When the robotic polishing project is complete, the next piece of BPI’s tech adoption roadmap is to implement cobots to tend a CNC turning and machining center. The cobots will also be equipped with an orbital sander to sand high contour parts in the final steps of production.
Manufacturing Readiness Grants (MRG) provided by the Indiana Economic Development Corporation and administered by Conexus Indiana are available to Indiana manufacturers willing to make capital investments to integrate smart technologies and processes that improve capacity. Batesville Products took advantage of the grant funding to support integration of smart robotics to help mitigate workforce challenges.
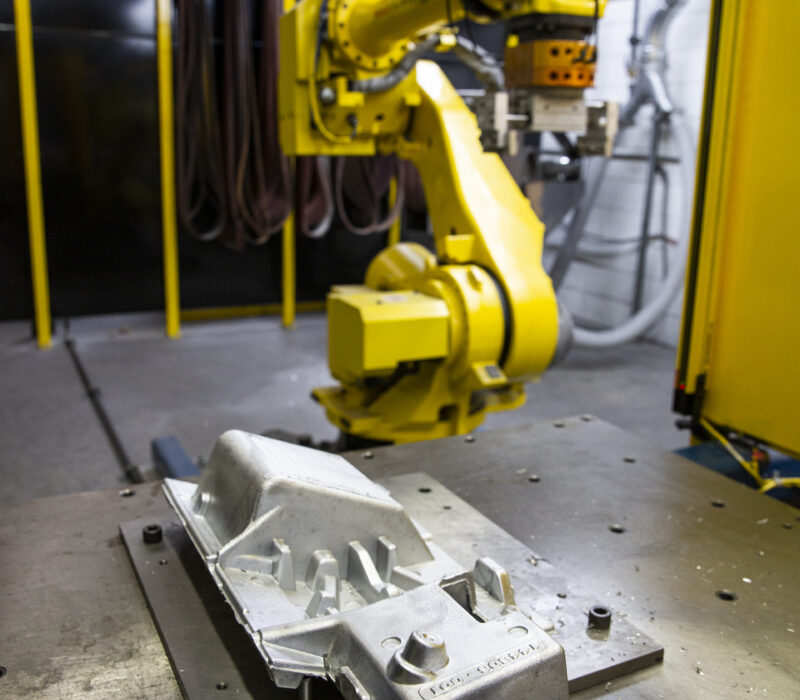
Key Learnings
Find the right balance of in-house vs. outsourced expertise for tech adoption.
Because the project was part of BPI’s 4-year smart automation roadmap, Len said the grant funding accelerated the timeline of the robotic cell project. “It’s quite crucial to make sure to that you have a reliable level of internal automation engineering capabilities,” he said. “Not necessarily full integration level, but capable of programming and troubleshooting.” He also noted that companies should realize that the custom design of a robotic cell can take just as long as obtaining the components in the robotic cell itself. BPI was also able to gain mentorship from a local Indiana partner, Purdue MEP, which helped them find the right balance of in-house and outsourced expertise to make the project a success.
BPI’s culture of transparency contributed to rapid acceptance of robotics within its workforce.
“We are very transparent in sharing plans with our employees,” Len said. Daily department meetings that include monthly sharing of slide decks that covered all technology investment activity in the company. “While I think certain employees remain skeptical, we approached this project with an all-hands event to engage shop floor employees in all aspects of the project during development,” he added.
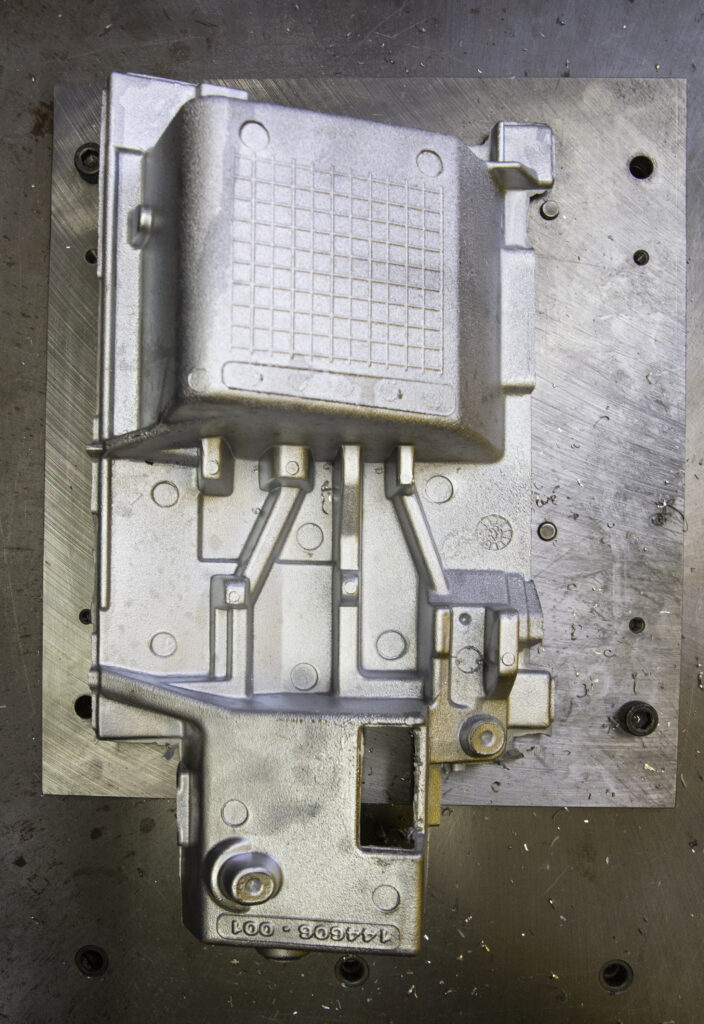
“The project will positively impact several of our hourly associates who currently manually polish and sand castings and their responsibilities will shift toward higher value and more rewarding tasks. If manufacturing companies are struggling with the funds needed to move forward with a smart manufacturing project, they should consider applying for an MRG and also consider the benefits of automation on their workforce.”
“If manufacturing companies are struggling with the funds needed to move forward with a smart manufacturing project, they should consider applying for an MRG and also consider the benefits of automation on their workforce.”
Len Weber
President and COO at Batesville Products, Inc.
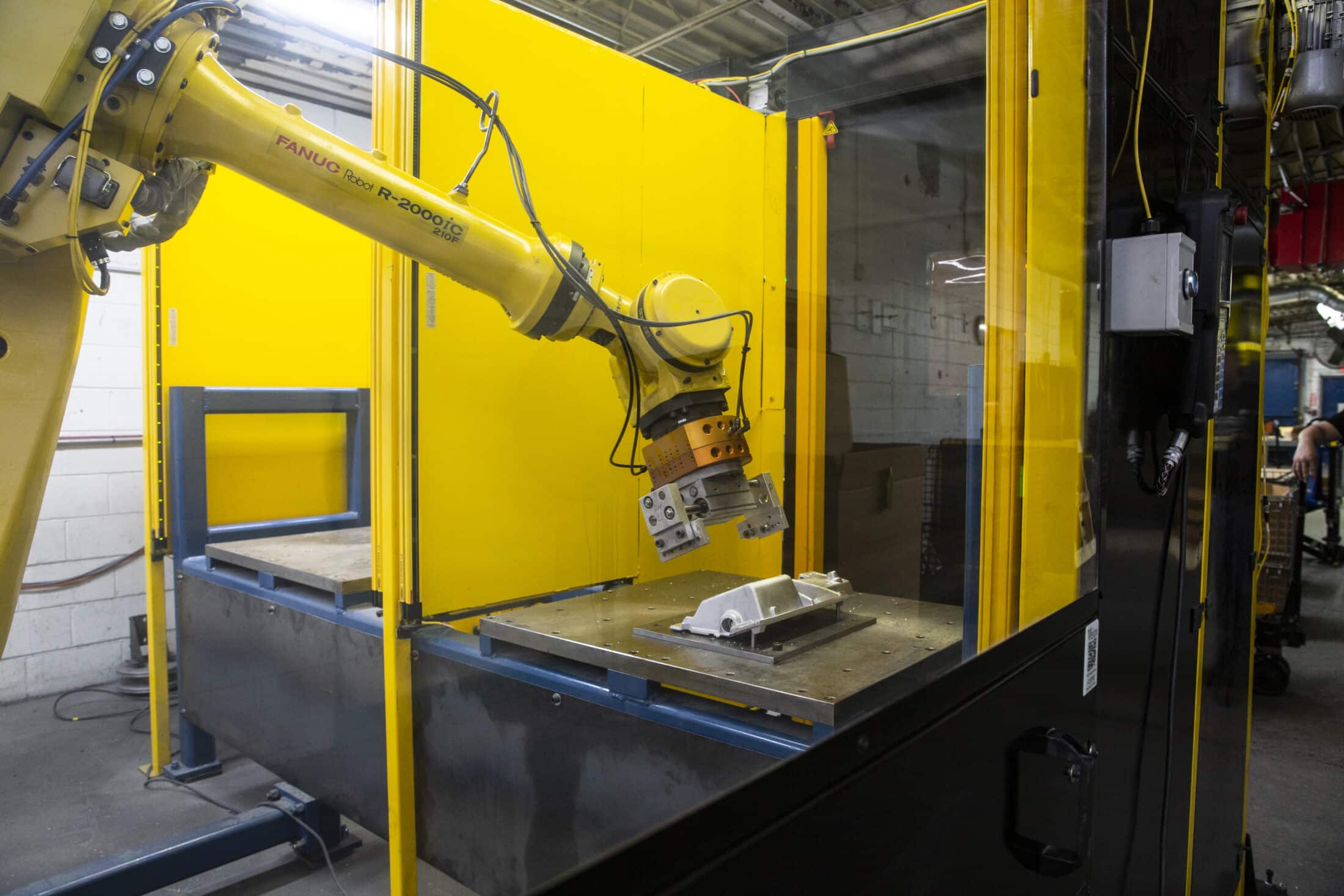