Batesville Tool & Die, Inc. Invested its Manufacturing Readiness Grant in Advanced Robotics with Integrated Machine Vision to Significantly Grow its Manufacturing Capacity
Batesville Tool & Die, Inc. (BTD)
Case Study
Key Stats
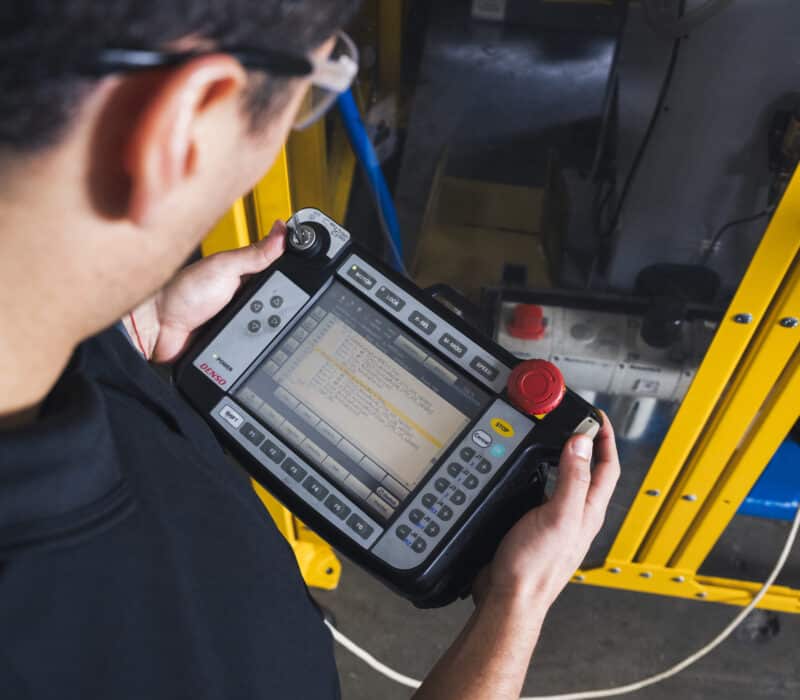
Company History
Batesville Tool & Die is a privately-owned manufacturer of automotive parts that supplies a global customer base of OEM, Tier 1 and Tier 2 companies.
Ronald Fledderman founded Batesville Tool & Die, Inc. (BTD) in Batesville, Ind., in 1978. Today the company offers a wide range of specialized capabilities, including tooling, metal stamping, welding and assembly. BTD’s products predominately support automotive needs, such as brakes, airbags, body, hinges and other diversified systems. While the company occupies satellite plants in both South Carolina and Mexico, the Batesville, Ind., location alone accounts for $100 million in annual revenues and has a workforce of nearly 500 employees. The firm operates in a high-volume manufacturing environment, producing millions of parts and components every month.
“We do complex stampings,” said company President Bob Holtel. “We work with a variety of materials, primarily steel, but also aluminum, stainless steels — anything that automotive companies demand.” What sounds like a simple process becomes much more complicated with BTD’s volume of 1.2 million brackets with 6-millimeter nuts each month. “It’s amazing the volume that automotive customers generate, and because of their standardization and regulation, we can justify new automation and technology to scale up our processes to produce those volumes,” he said.
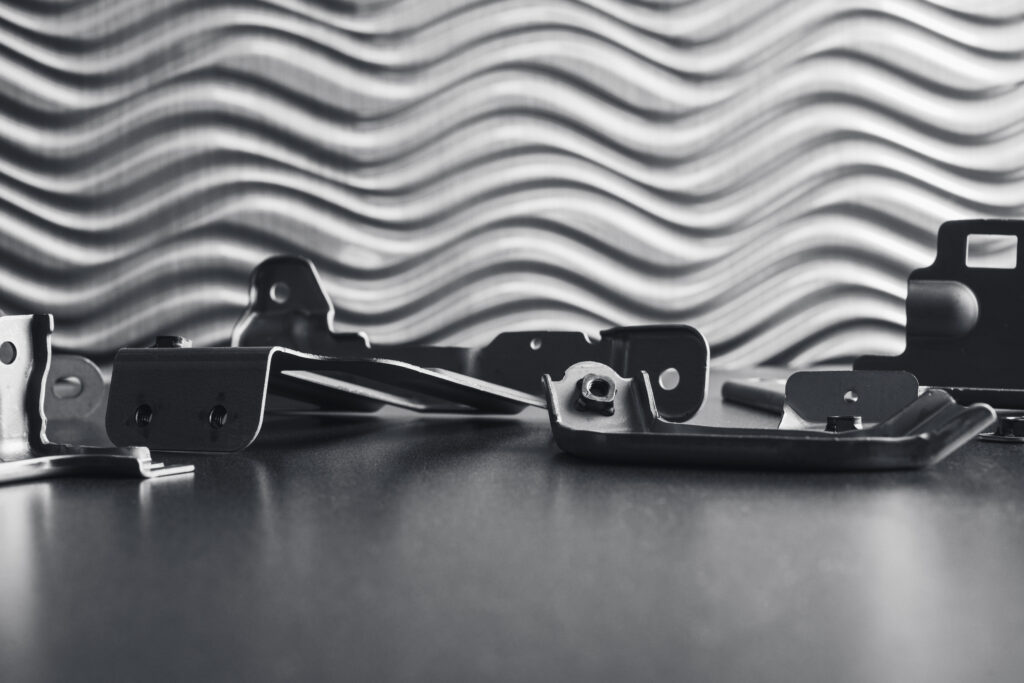
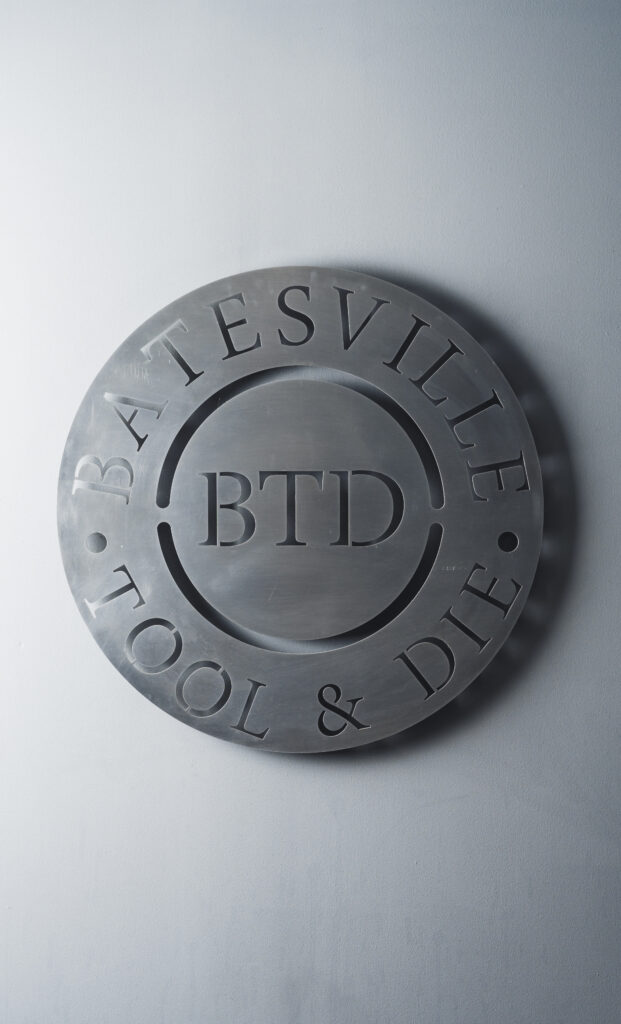
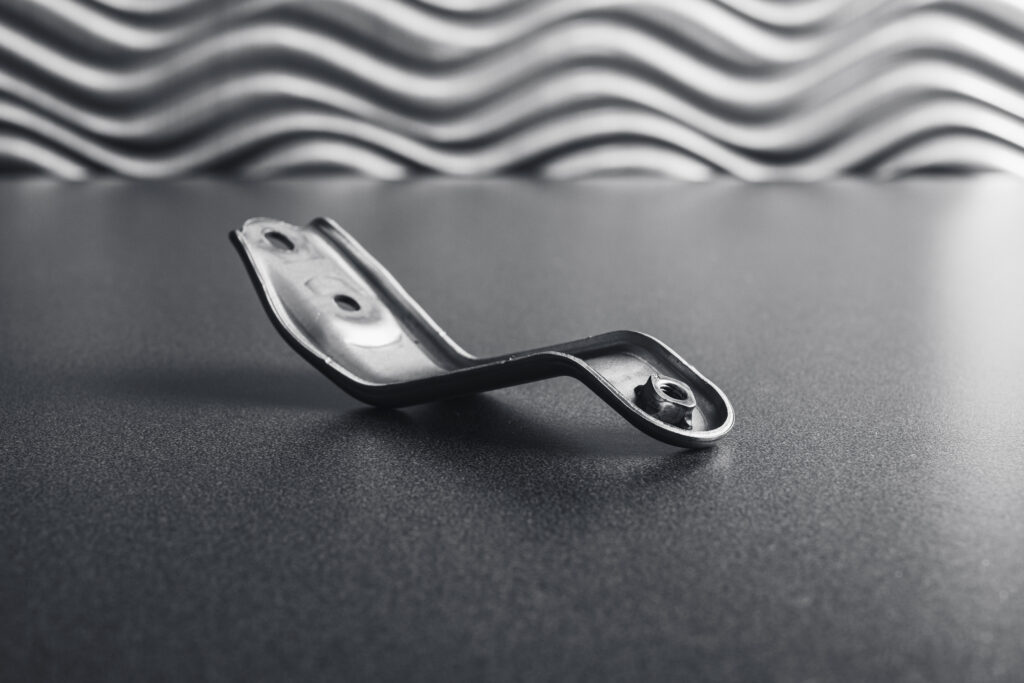
Bob Holtel is now President of BTD, having risen through the tooling, machining, design and sales department ranks over his nearly 40 years with the company. He was joined to talk about the company’s technology adoption journey by Jorge Lopez, vice president of finance, who started his BTD career in the company’s Mexico facility in 2001; Dave Lynch, vice president of tooling, who spent 35 years at BTD in tooling; and Automation Manager Justin Fledderman whose 15-year career with BTD began as a summer employee while he was in high school and continued full-time after he graduated from Purdue University in 2010.
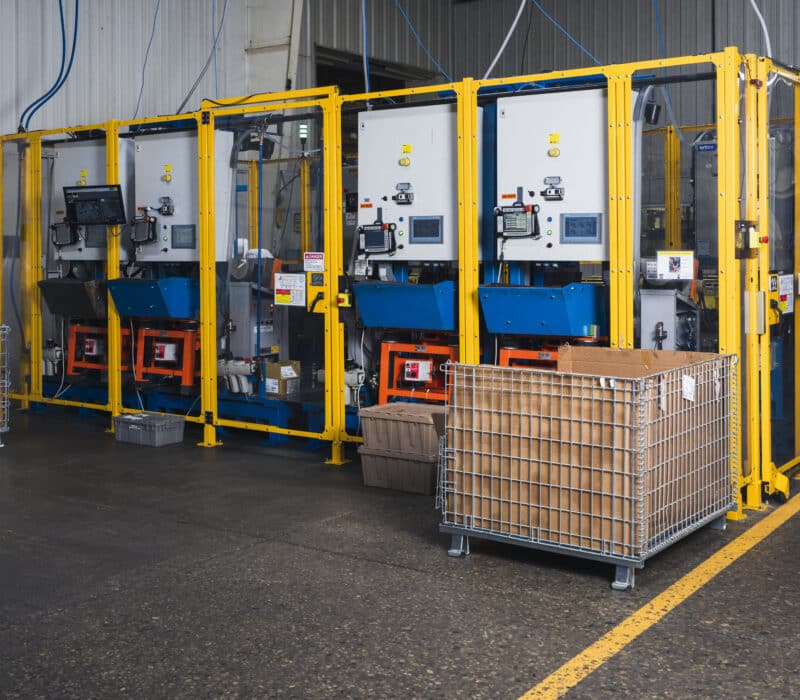
The Project
BTD invested in a customized solution with robotics and machine vision to automate its bin picking process.
BTD’s high-volume manufacturing processes and part complexity called for innovative technology and a customized robotics solution. The goal was to deploy robots with integrated cameras to pick up parts from a random position out of a bin using a gripper tool. The technology investment enables BTD to increase its volume with the consistent quality required by its automotive customers. “Under the new bin picking process, a machine vision system tells a robot to verify that it is the correct part and in the correct orientation for the next step in manufacturing. The robots are also programmed to understand that, if the part is bad, it needs to be put in a separate bin,” Justin explained.
Because many of BTD’s parts and metal components have a different geometry, each part had to be programmed independently. The machine vision system must be able to differentiate between the shadows, outlines and pickup points. “Each part is ‘unique’ due to where it is randomly located in the bin,” Bob said. “The technology integration required a lot of learning as we completed it and there were some adjustments, but once we had the ‘aha’ moment, adjusting the process for different parts became easier and easier.” Justin added, “the sheer amount of data crunching was another big piece for our team internally. Behind what sounds like a relatively simple bin picking project turned out to be a very technical process.”
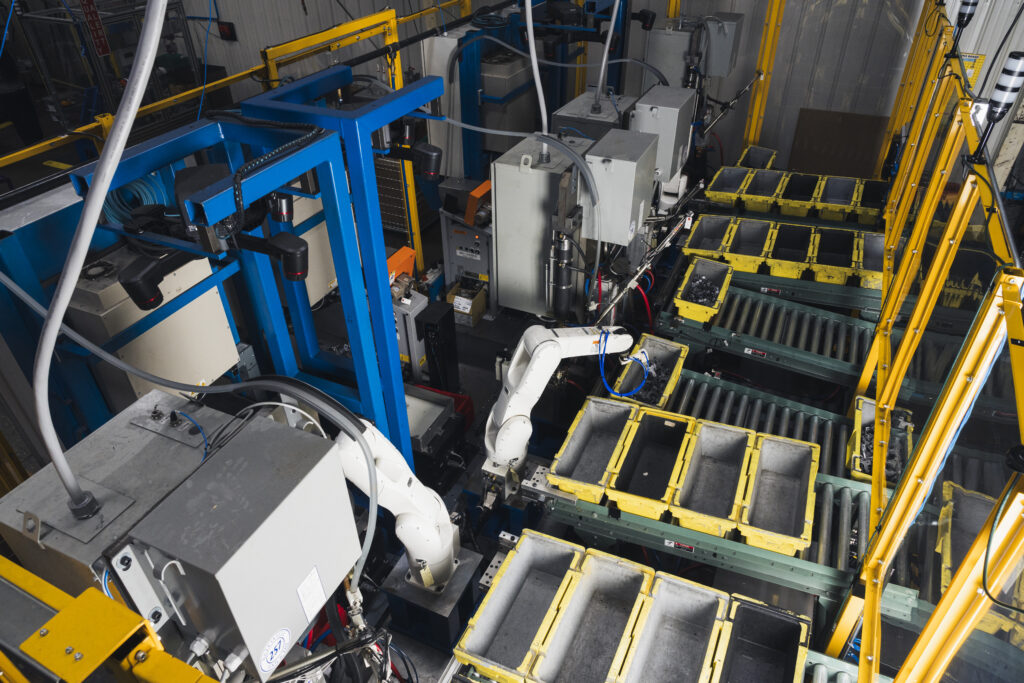
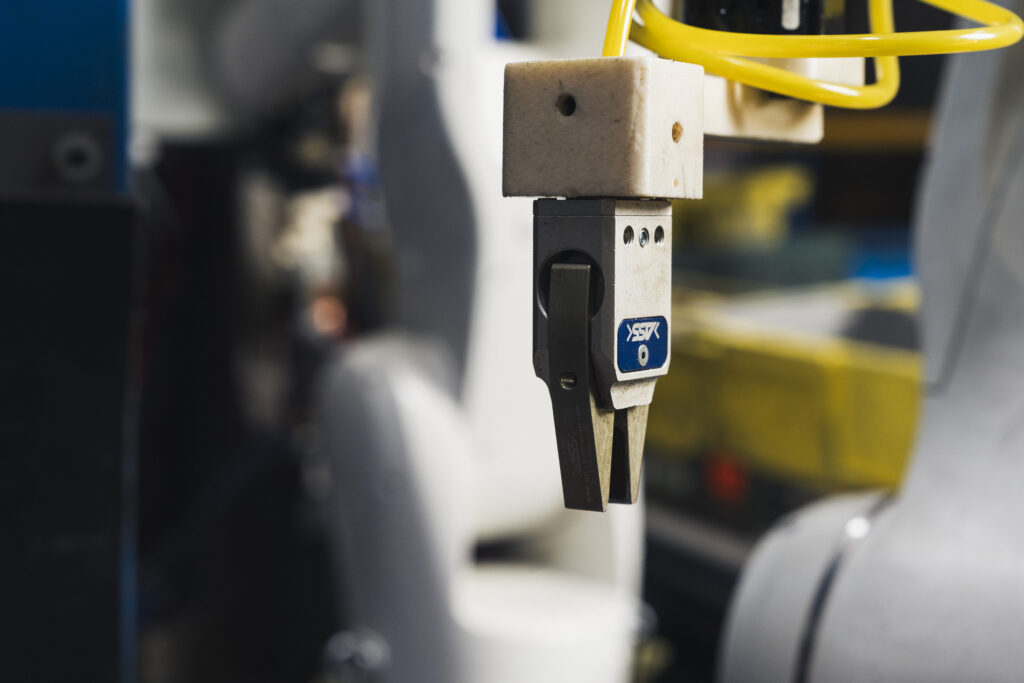
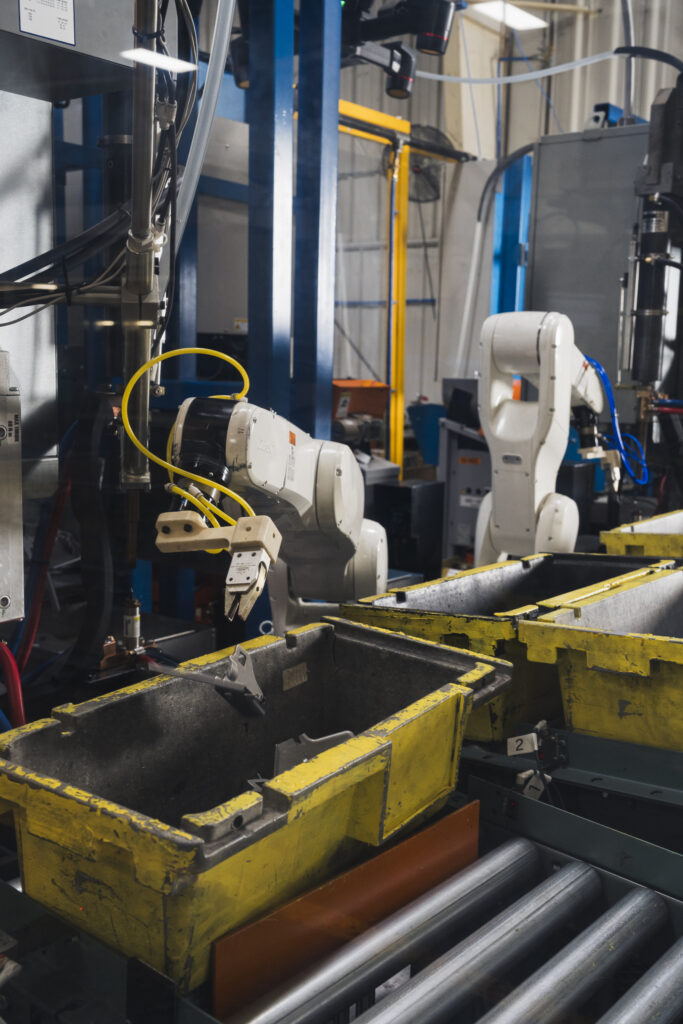
“This was our first experience with bin picking automation,” Bob continued. “We also knew that we wanted an automated system that can be adjusted from part to part. Maintaining flexibility is crucial for our manufacturing processes, and the system had to be adaptable to assemble 8-millimeter nuts or 10-millimeter nuts, for example. We can already adapt our welding cells to weld different size nuts, but the big jump for us is in bin picking automation.”
Manufacturing Readiness Grants (MRG) provided by the Indiana Economic Development Corporation and administered by Conexus Indiana are available to Indiana manufacturers willing to make capital investments to integrate smart technologies and processes that improve capacity and productivity. The MRG of $71,912 awarded to Batesville Tool & Die (BTD, Inc.) supported the adoption of an automated bin picking system with integrated machine vision that adjusts from part to part.

Key Learnings
BTD’s technology adoption project was based on a strategic plan formulated and shaped over nearly six years – and was developed as a custom solution in-house.
The decision to develop a customized automation solution in-house wasn’t a spur-of-the-moment choice. “We started thinking about how to improve our post-processing after pressing and stamping,” Justin said. “We do millions and millions of 6-millimeter nuts every year, and I talked to probably 30 different integrators, machine vision and automation companies. There was one common theme to each of these discussions. They all said yes, they could do it, but none of them had any evidence that they are doing it for a current customer. I began to have a feeling that if we presented them with eight different parts that all had completely different geometrics, they weren’t going to be able to create us something that was within our price range.”
The best solution, Justin decided, was to develop a custom solution in-house. BTD purchased one of the camera systems and set it up internally. “Eventually we had a meeting with company leadership to determine if we all felt comfortable taking the next step.” The leadership team included several people at different levels and different positions within the company. “We talked to many different people in the company to hear their concerns and we kept product quality top of mind,” Justin said.
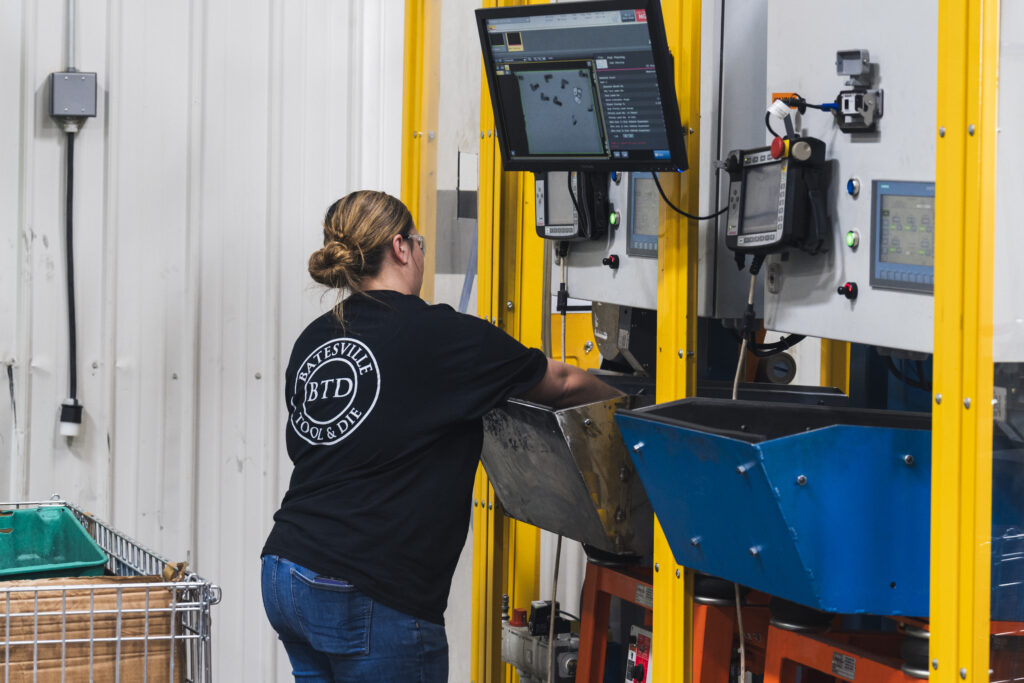
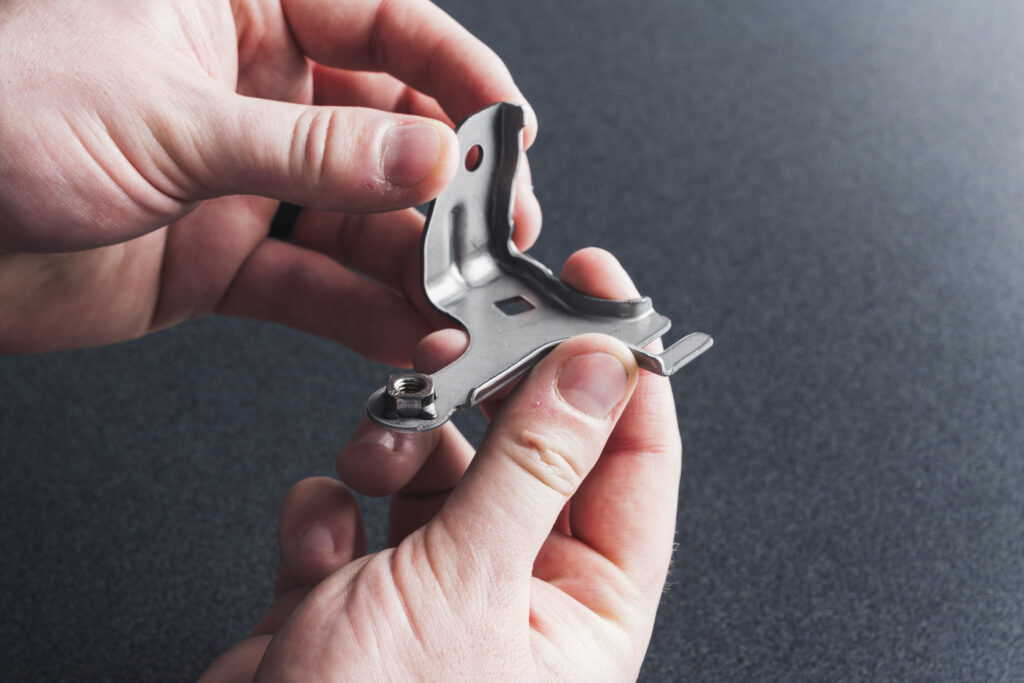
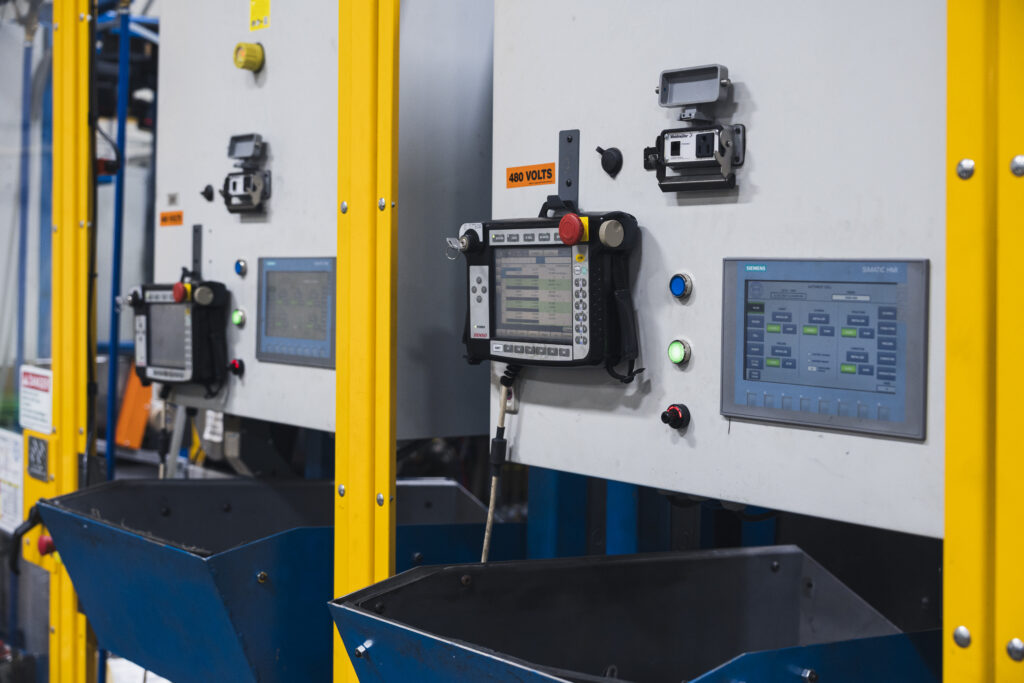
Once BTD had piloted the custom solution on a small scale, everyone, including upper management, came together. “One of the challenges of technology adoption is determining the ROI. It’s a series of steps, and you have to justify a little bit of budget along the way, and a little bit more budget to take the next step,” Bob said. “Ultimately, the process is like the way venture capitalists fund start-ups. They don’t give all the money up-front. They commit blocks of money in a series of investments to hit specific milestones. It was a process of hitting internal process development milestones and getting closer to the end goal. We all had dreams and aspirations of what this might look like in the end, and we challenged Justin’s team to go execute on it.”
Implementing new technology and automation is changing the nature of BTD’s manufacturing workforce in its Batesville facility.
Justin pointed to the increased opportunities for upskilling that automation and technology have provided at the plant. “It creates new positions and opportunities for advancement,” he said, adding that the company sees different kinds of applications since increasing its investments in automation. “Robotics, machine vision and 3D printing all contribute to a facility that accelerates its overall productivity and quality control,” Justin said. To make these upskilling opportunities a reality, BTD also offers on-site educational opportunities. An Ivy Tech Community College lab located at BTD offers tuition reimbursement and tuition deferment to employees who work toward a degree or certification.
“One of the challenges of technology adoption is determining the ROI. It’s a series of steps, and you have to justify a little bit of budget along the way, and a little bit more budget to take the next step.”
Bob Holtel
President at Batesville Tool & Die Inc.
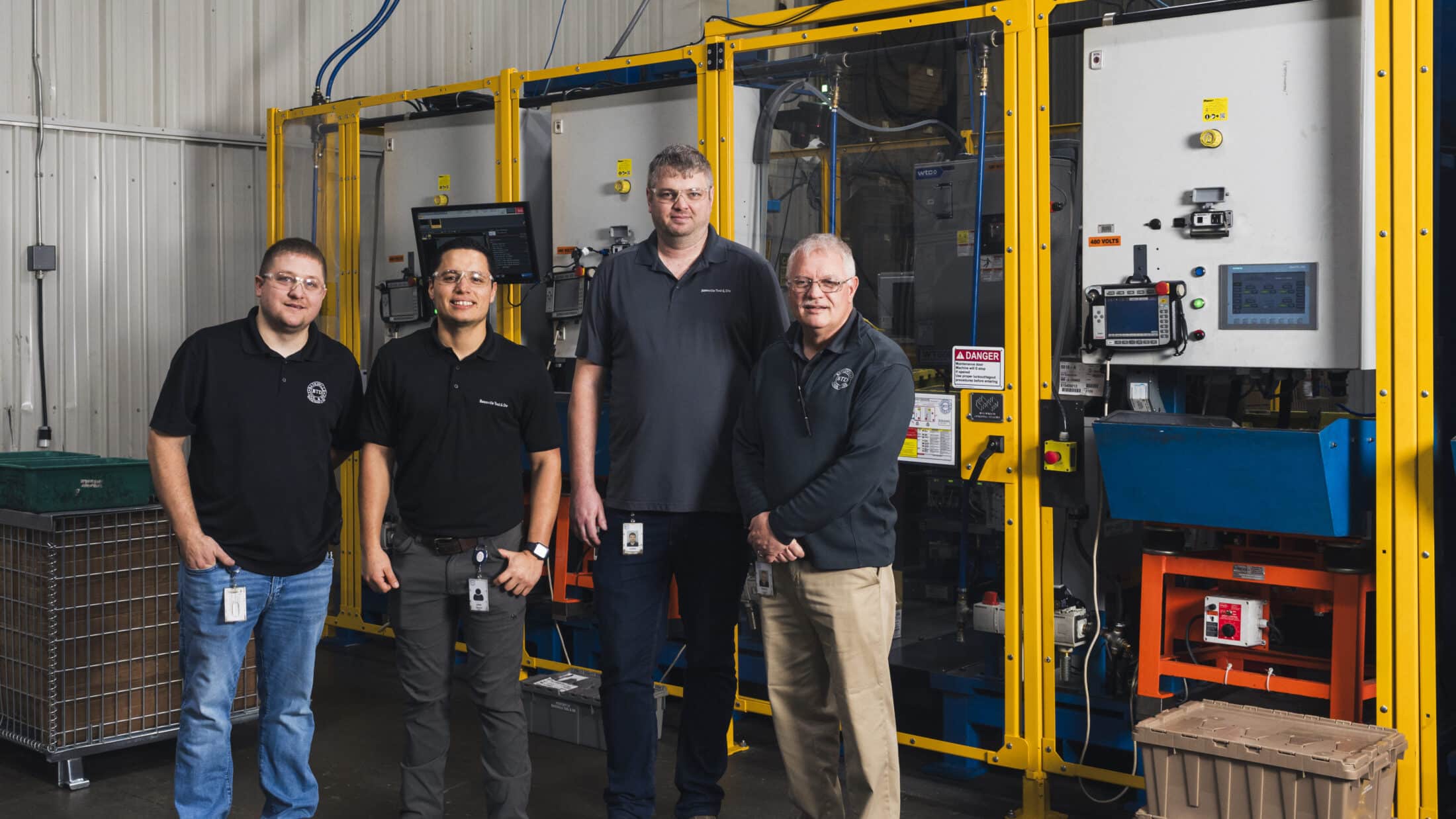