Digital Wood Carver Implements a Collaborative Welding System with Support of an Indiana Manufacturing Readiness Grant
Digital Wood Carver LLC
Case Study
Key Stats
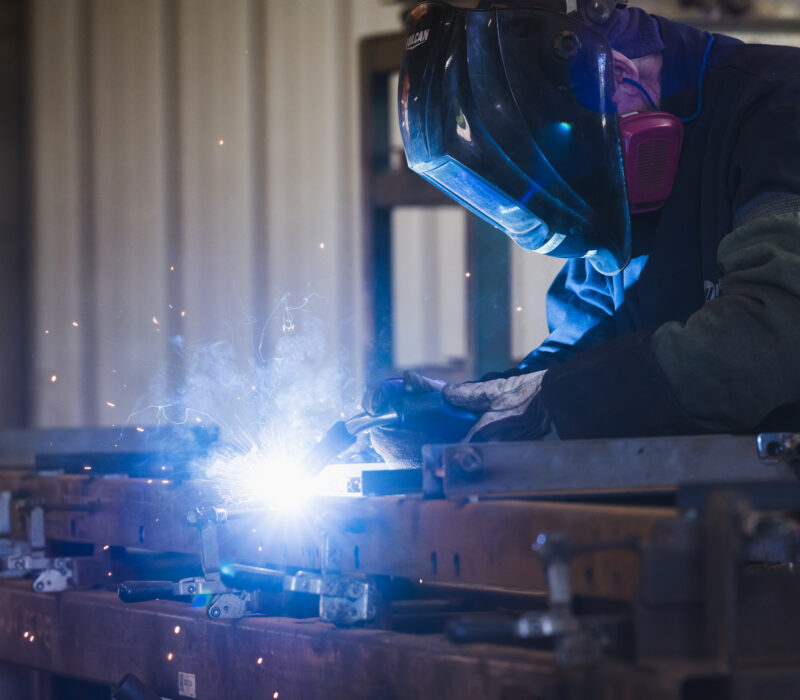
Company History
Burl Tichenor started his career at a local manufacturer in the timber and woodworking industry. Today that same company is one of his biggest customers at Digital Wood Carver.
Shortly after high school graduation, Burl Tichenor was hired for an entry-level job in assembly at Wood-Mizer LLC. Soon he was promoted to a spot in the engineering department’s customer service at the company’s headquarters. From there he moved into design engineering and took up woodworking as a hobby. Combining his new-found passion and his expertise as a design engineer, Burl began designing CNC cutting machines for his own use and building prototypes in the evenings. When his prototypes began to sell, Burl hired a part-time employee to help him, and soon the side gig grew, leading Burl to realize it was time to choose which career path he wanted to follow. After almost 28 years at Wood-Mizer, Burl left to become an entrepreneur and focus full-time on his new company, Digital Wood Carver. “You know, CNC technology used to be just for manufacturing,” he said. “Now we’ve made them an innovative tool for high-end hobbyists and entry-level business users. More people can get involved with woodworking and can do it well.”
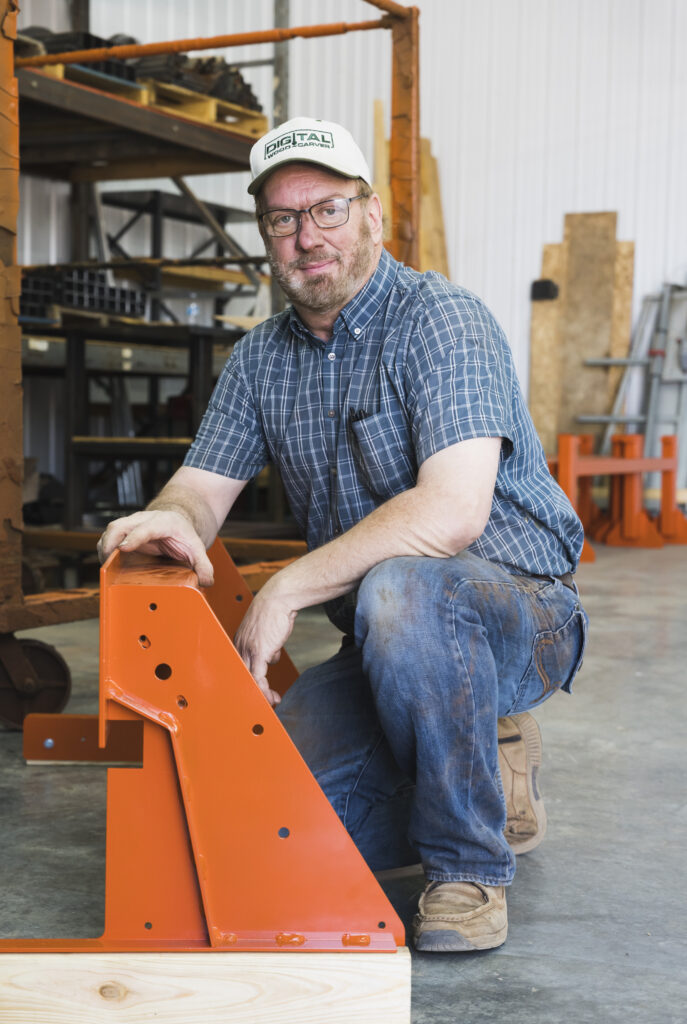
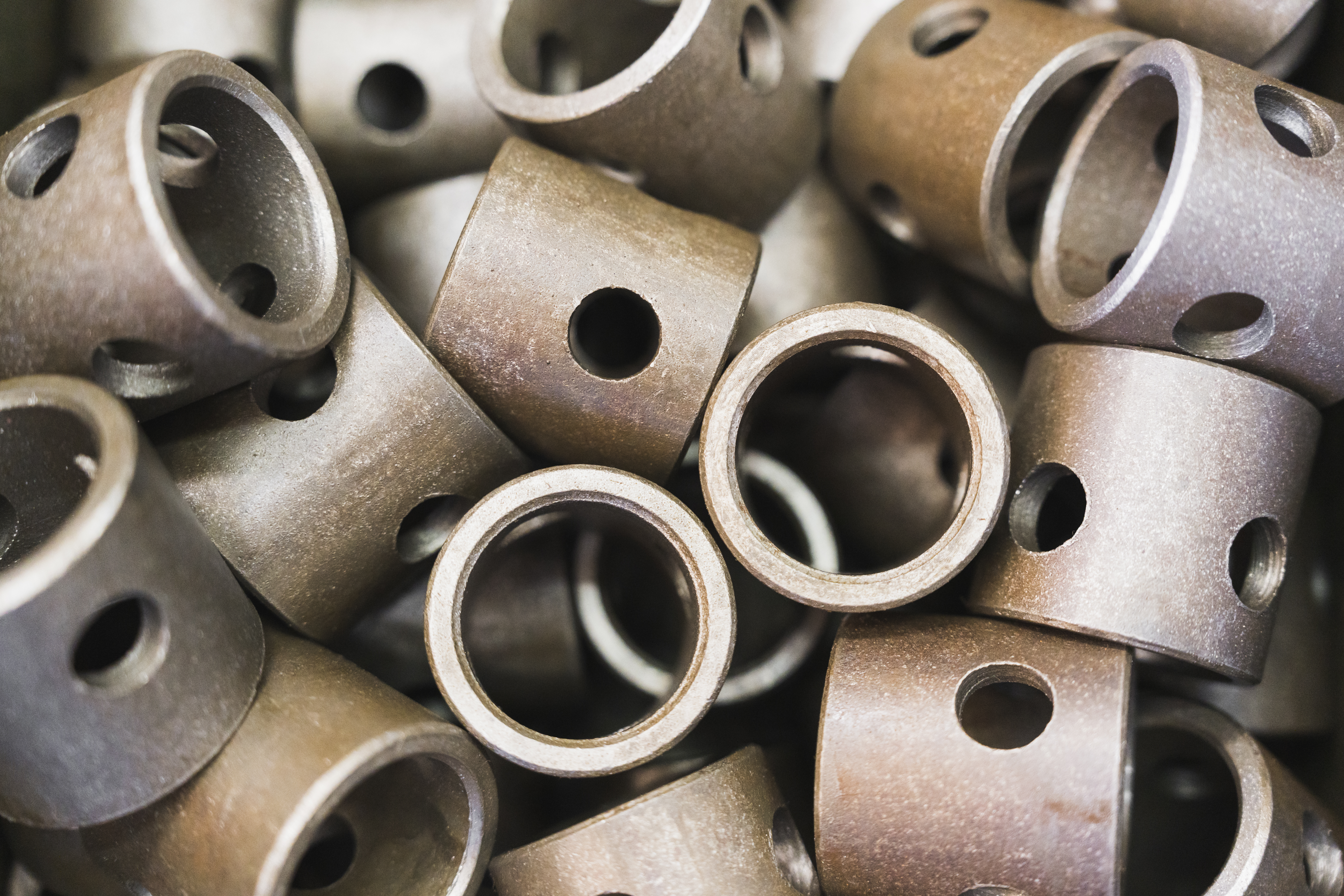
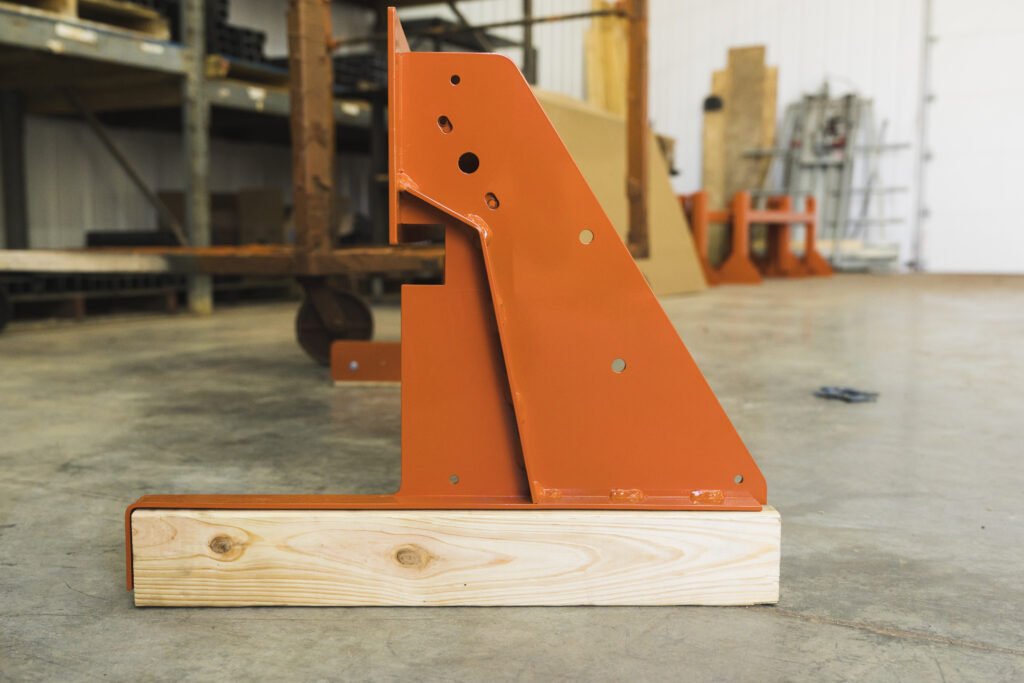
Four years after Burl left Wood-Mizer, his previous employer approached him to design one of that company’s products. Because its business development had outgrown its own capacity, Wood-Mizer asked Burl if the Digital Wood Carver shop could produce that product as well. Named Slab-Mizer, the new product was released 4 years ago, and Digital Wood Carver now produces multiple units each week for Wood-Mizer—a testament to Burl’s value first as an employee and now as a supplier for his former employer. While it wasn’t the most common path to success as a manufacturing entrepreneur, it is one that exemplifies Hoosier values of customer service and hospitality.
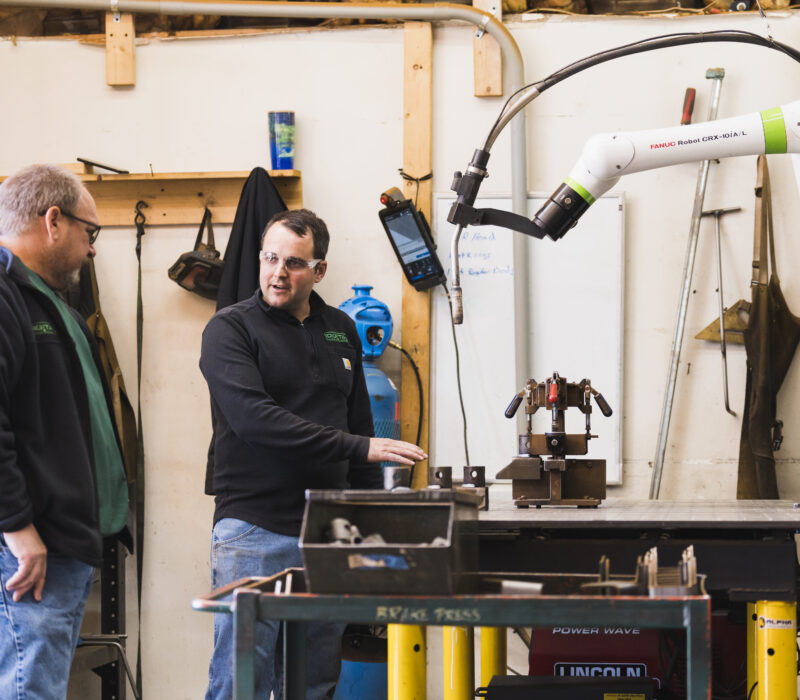
The Project
Implementation of a cobot welding system solved a physical space problem for Digital Wood Carver versus a robotic welding system and improved manufacturing flexibility for low-volume, high-mix products.
Burl’s young company was growing. With the increased business, welding became a bigger part of Digital’s production and space was an issue. “At times,” Burl said, “our team was literally welding in the hallway isles due to space constraints. Burl considered and researched robot welding systems as a smart technology solution, but quickly realized the safety requirements for even a single robot stretched beyond his factory’s available floor space. A robot must be enclosed in a large safety cage to protect workers. As a small- to medium-sized enterprise, Burl began to consider a cobot-based system as a solution. “That’s what made this so attractive,” he said. “We literally can set it up on a table and move it to wherever it is needed.”
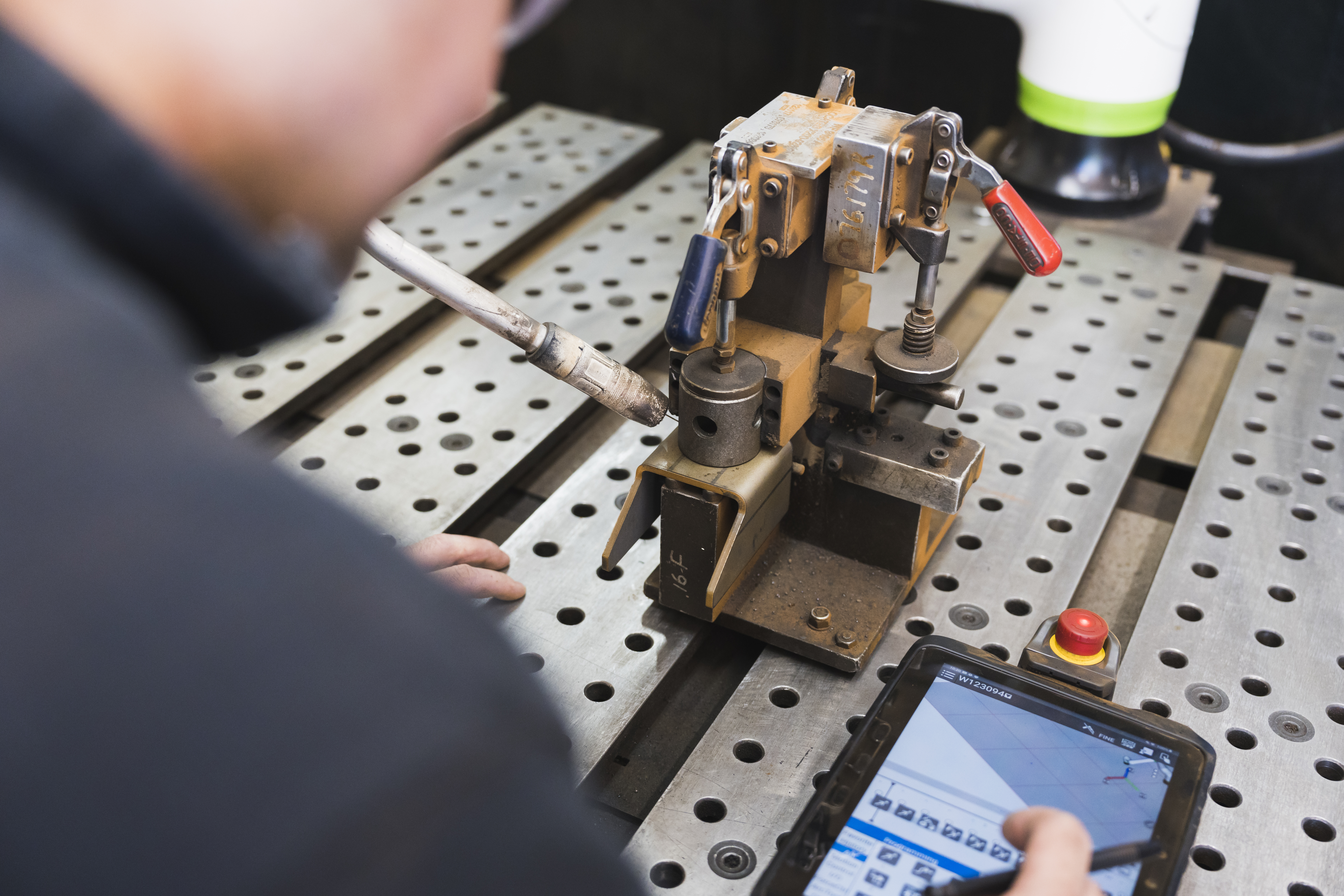
The cobot welding system can move in 3 dimensions around the machine, rather than requiring the worker to move the welding tools into place to complete a single product. It is just another space-, time- and expense-saving feature of the system. It’s also easy to adjust the control system for the cobot to match the different requirements of our product, too—another advantage that clearly made a cobot the better choice. Programming is straightforward and fairly simple to learn, especially for today’s computer-savvy employees. “We had to contact the manufacturer a couple of times, but it was easy for our welders to learn and then train others,” Burl said. Today, 3 of 4 welders at Digital Wood Carver can run the cobot whenever needed. “Probably the biggest piece of the technology implementation we wrestled with was the table and how to lay it out,” he explained.
Manufacturing Readiness Grants (MRG) provided by the Indiana Economic Development Corporation and administered by Conexus Indiana are available to Indiana manufacturers willing to make capital investments to integrate smart technologies and processes that improve capacity and productivity. Digital Wood Carver LLC made its next move into Industry 4.0 with the purchase of a collaborative welding system with help from an MRG of $32,500.
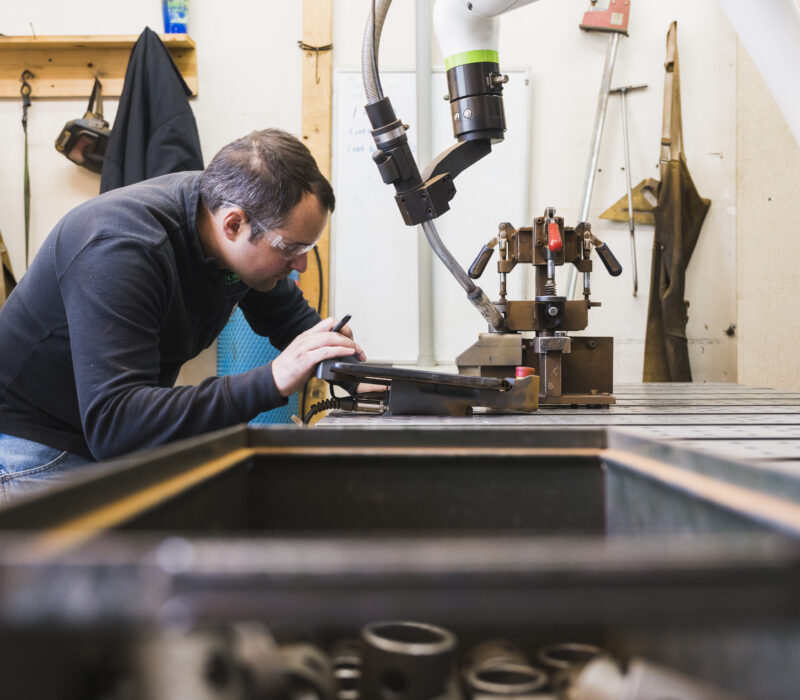
Key Learnings
The cobot welding system has made a positive impact, and Digital Wood Carver is eying the possibility of 2 more systems in the future.
“One of the things we often think about is whether the cobot welding system was worth it. If you think about a technology investment in the short term, it can be hard to justify. But over the next 5 years to 10 years, the life of the system, that’s where it really pays off.” Already he’s seeing one big pay-off: The quality of the welds is consistently better than a manual weld. Burl is convinced Industry 4.0 is where he wants to take his company, and he’s already planning for Digital’s second digital acquisition. In fact, he recently applied for another Manufacturing Readiness Grant under the $200k per company cap to help fund a new project too.
The welder’s skills and experience are crucial pieces of the human/cobot partnership.
Like most Indiana companies stepping into Industry 4.0, the smart technology wasn’t intended to and didn’t eliminate any workforce. It was designed to replace some of the repetitive parts of the job, leaving the humans to do work that requires human skills, in this case, fine-tuning the cobot welds to meet Digital Wood Carver standards. “Even with the cobot, you still need to know how to weld,” Burl said. “It’s estimated that welders only spend about 15% or 20% of their time—maybe even less—welding. The rest is moving materials around. You need the ‘eye’ to weld, and to program the CNC controller to weld.”
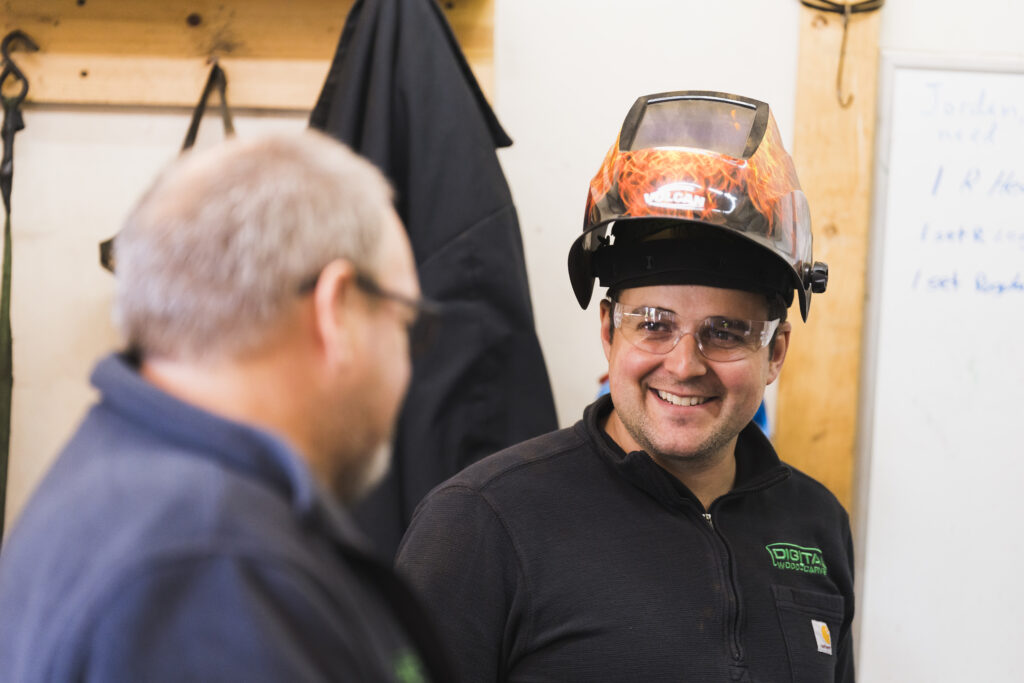
He went so far as to say that, if choosing between 2 candidates to supervise the cobot system, “I would much rather pick someone who knows how to weld,” he said. “We can teach them how to work with the cobot.” And prospective employees tend to lean into the prospect of working with the new technology, he finds. He acknowledges that a few of the older employees have hesitated at using the cobot, but most believe it will help them do a better job. “Even the ones who don’t want to use it, don’t bash it.” And if a candidate was offered welding jobs at 2 companies, one working with a cobot and 1 working manually, Burl believes the outcome would be close to unanimous. “I can’t say 100%, but I would say close to 90% would go toward the job that has the technology. That’s one of the cool things about smart technology. It does take the monotony out of the work.”
“What made this [the cobot welding system] so attractive … is we can literally set it up on a table and move it to wherever it is needed.”
Burl Tichenor
President at Digital Wood Carver, LLC
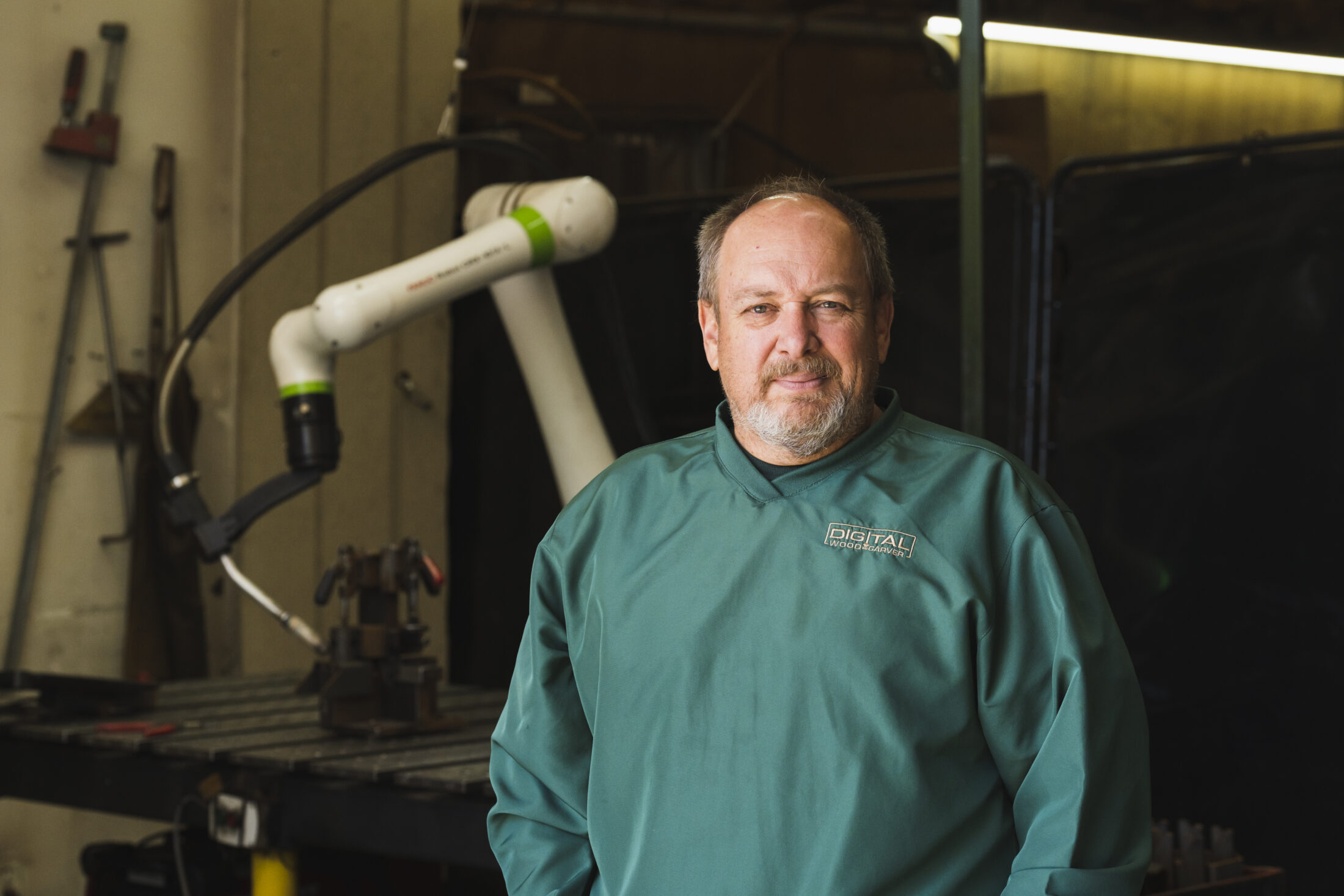