$2 Million of Investment in New Tech Capabilities and a Strong Business Case Earned Hammond Machine Works a Manufacturing Readiness Grants Award
Hammond Machine Works
Case Study
Key Stats
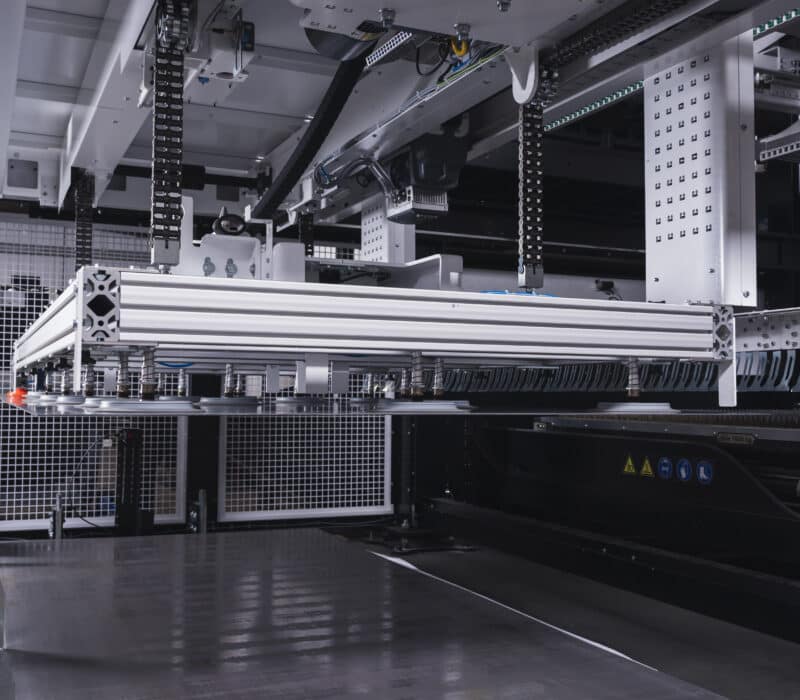
Company History
Following the 1st Industrial Revolution, Hammond Machine and Forge Works was founded in 1908 to support the rail car industry.
Gastavos A. Kuehl opened the doors of the new company in 1908 in a time of rapid industrial expansion and scientific discoveries. Railroad networks and technologies, including the telegraph and telephone, were becoming widely accepted and electrification was ushering in a new era of globalization. The First World War was just around the corner and, by the time it ended, the modern world of the 2nd Industrial Revolution would be entrenched. Gastavos’s original 12,000-square-foot building in Hammond, Indiana, housed a thriving operation, specifically serving the growing rail car industry.
As the 3rd Industrial Revolution was getting ready to onset in the late 1900s, D. N. Nau (“Mike”) purchased the company. He renamed it Hammond Machine Works (HMW) and relocated it to its current location where he established it as a family enterprise focused on expansion. Mike defined HMW not by the parts it manufactured, but by its relationships with customers, employees and the community. In 1990, HMW installed its first CNC machine, becoming an early adopter of that technology.
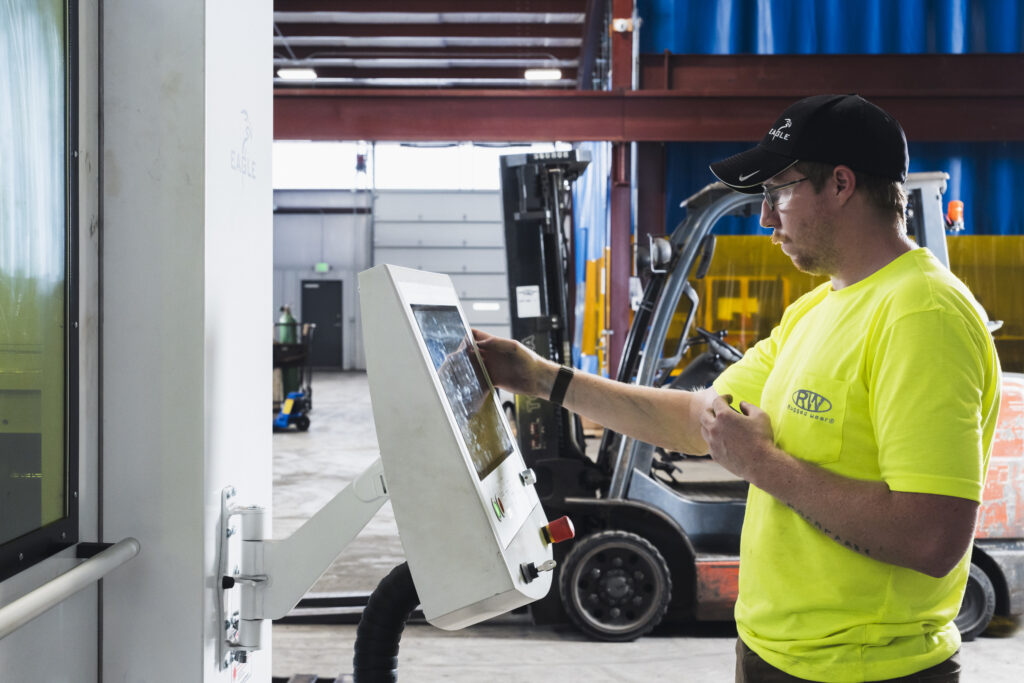
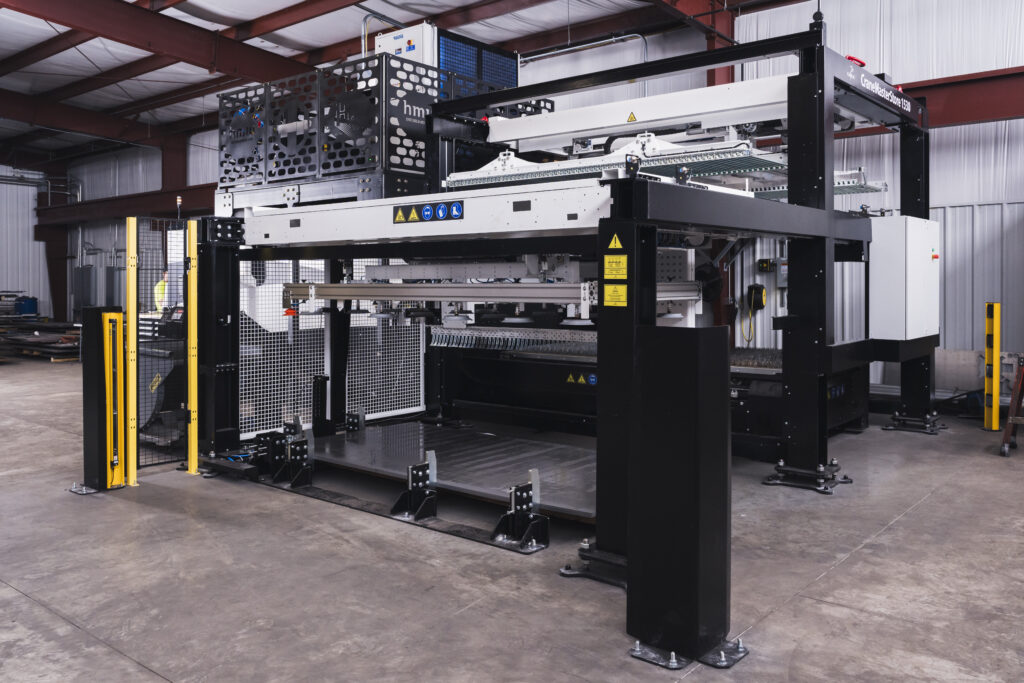
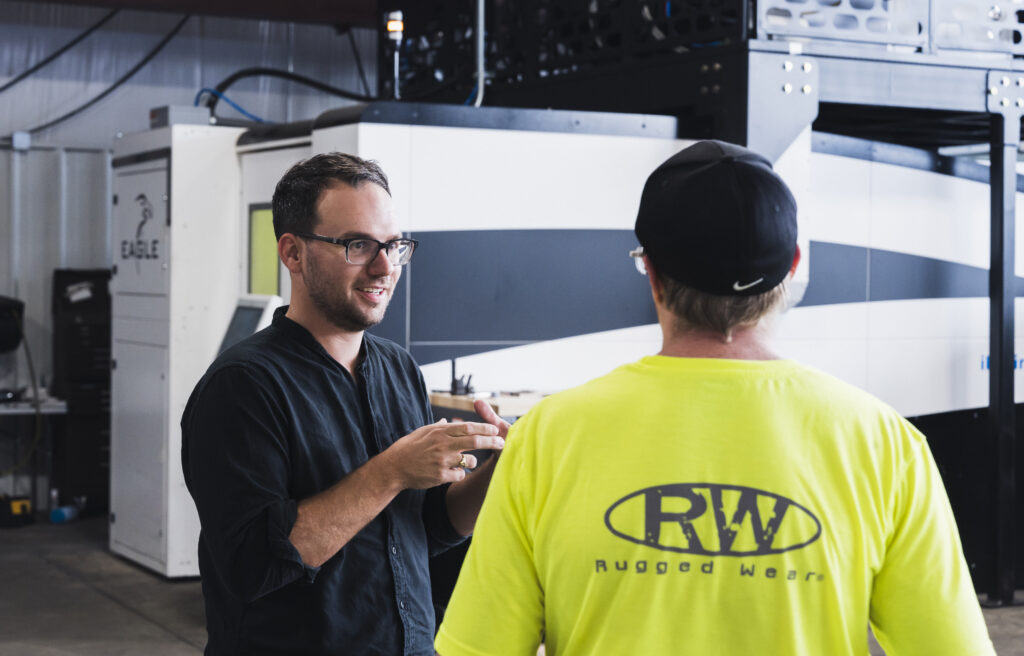
In 1992, Peter Nau purchased the company from his father and became president and CEO. He continued the automation path Mike had paved and added state-of-the-art equipment and expanded HMW’s footprint to 42,000 square feet. A second location in Addison, Texas, now serves customers in the South. “Now we concentrate on automation, CNC machining and robotics,” Peter said. HMW continues to grow and today has 75 employees, with 80% of sales serviced at the Indiana plant. The firm now partners with OEMs across industries to provide high-quality manufactured solutions, including precision machining, tooling, metal fabrication, assembly and finishing, along with engineering services.
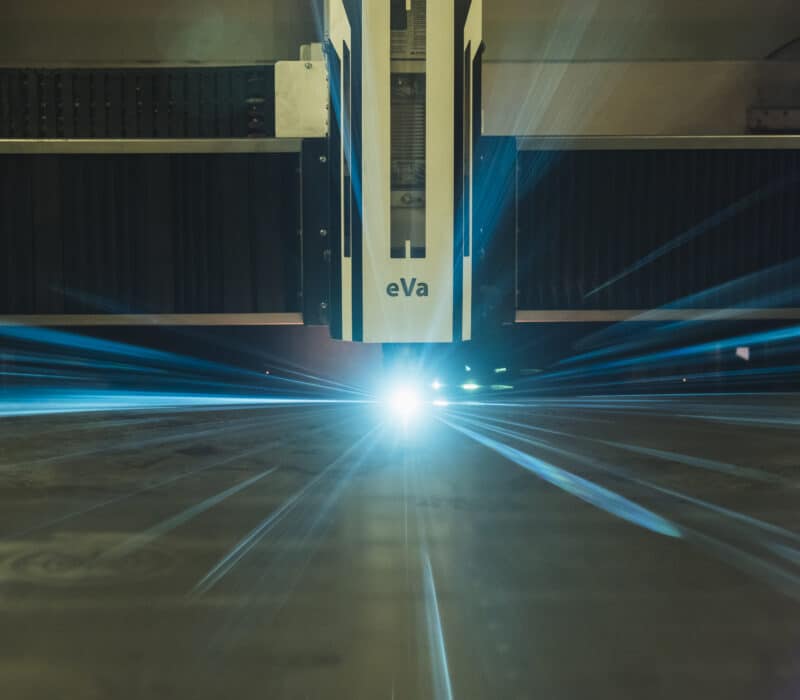
The Project
The $2M price tag for a 20kW fiber laser cutter was a large technology investment for HMW but had the tech packages to make it worth the while.
“From the beginning serving the rail car industry, we’ve gone on to partner with original equipment manufacturers (OEMs) across industries to provide high-quality manufactured solutions,” Peter explained. “Our 1-stop solution experience sets us apart and we deliver on budget and on time.” To continue that extraordinary service and the HMW commitment to investment in automation required a state-of-the-art 20kW fiber laser, leadership decided. That total project, including facility improvements to house the equipment, would cost over $2M. A fiber laser is the most technologically advanced laser currently manufactured, with the loading station and cutting process 100% automated.
The INspire machine developed and manufactured by Eagle eliminated most of the third-party contractors, realizing an estimated $300K in annual saving. “The timing of delivery is also very important,” Peter explained. “Stopping production of a rail car because of material shortages is devastating and not uncommon when third-party suppliers are involved. When the assembly line halts, there is no way to make that time up.”
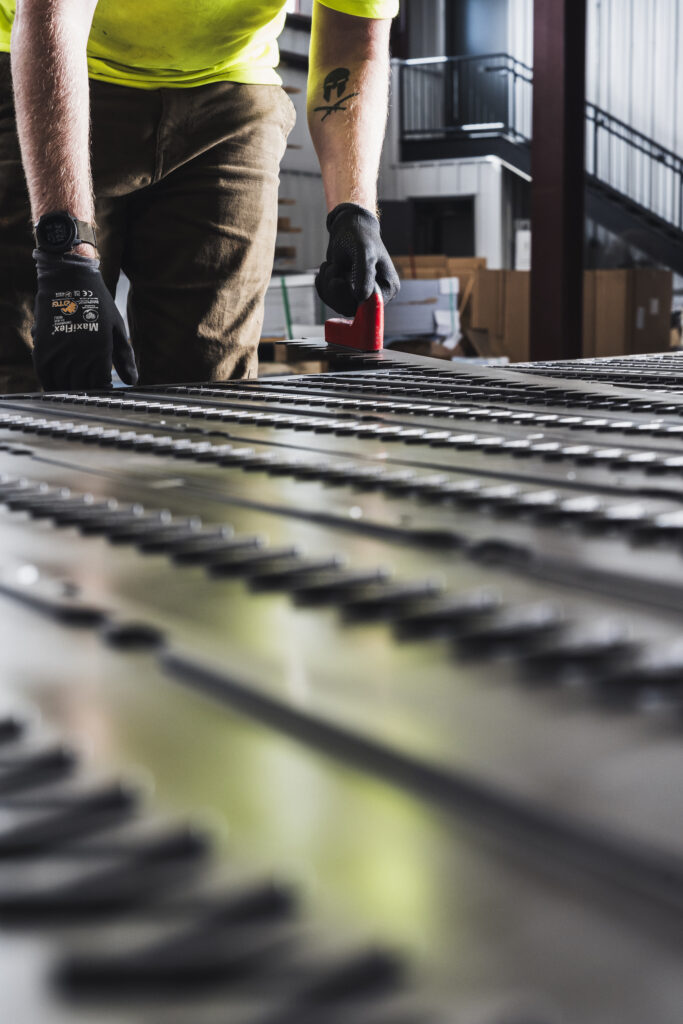
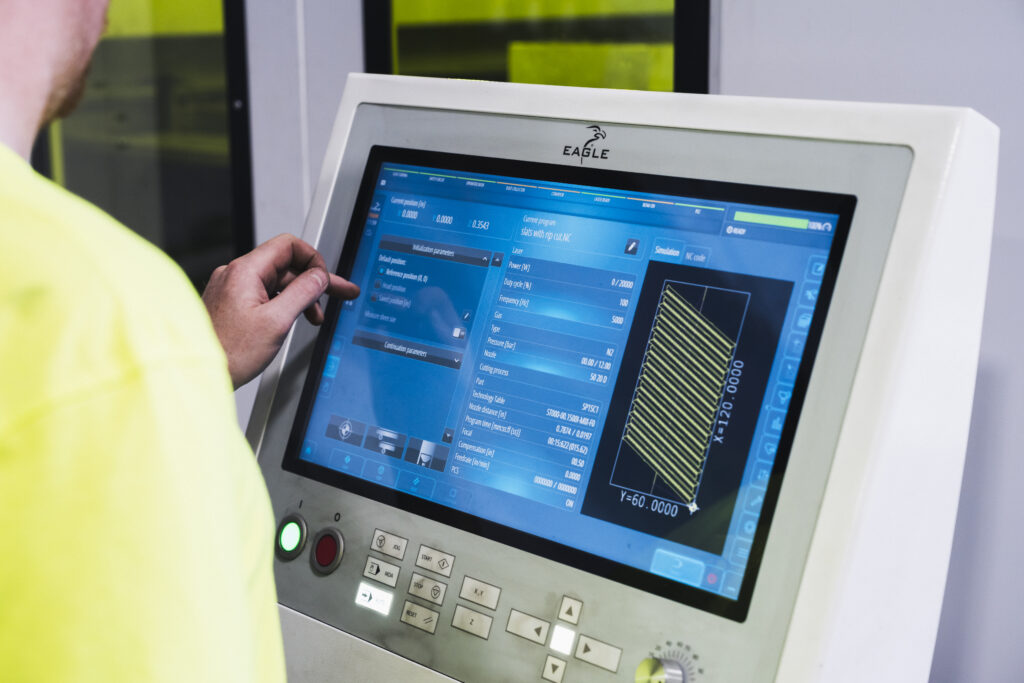
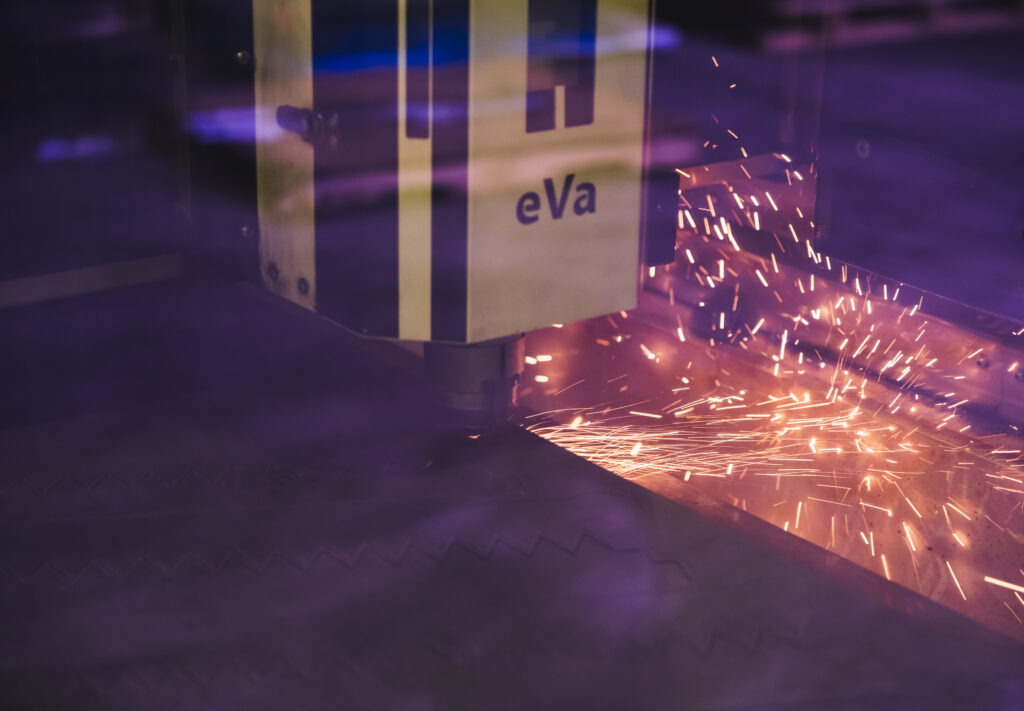
“It (the INspire) has significant controls and software integration,” Peter explained. “It has a library of parts and is capable of nesting.” He described “nesting” with a grin. “If you are baking cookies and you have 50 different shapes that you want to cut out with 50 different cookie cutters, you want to get the maximum number of cookies out of the dough that you can.” The INspire is the first laser cutter that can auto-nest, and that is very valuable. With it, he said, the laser also can run “lights-out,” dramatically increasing HMW’s capacity.
Manufacturing Readiness Grants (MRG) provided by the Indiana Economic Development Corporation and administered by Conexus Indiana are available to Indiana manufacturers willing to make capital investments to integrate smart technologies and processes that improve productivity and capacity. Hammond Machine Works expanded its manufacturing capabilities with a $2M project that was supported by a MRG of $187,500.
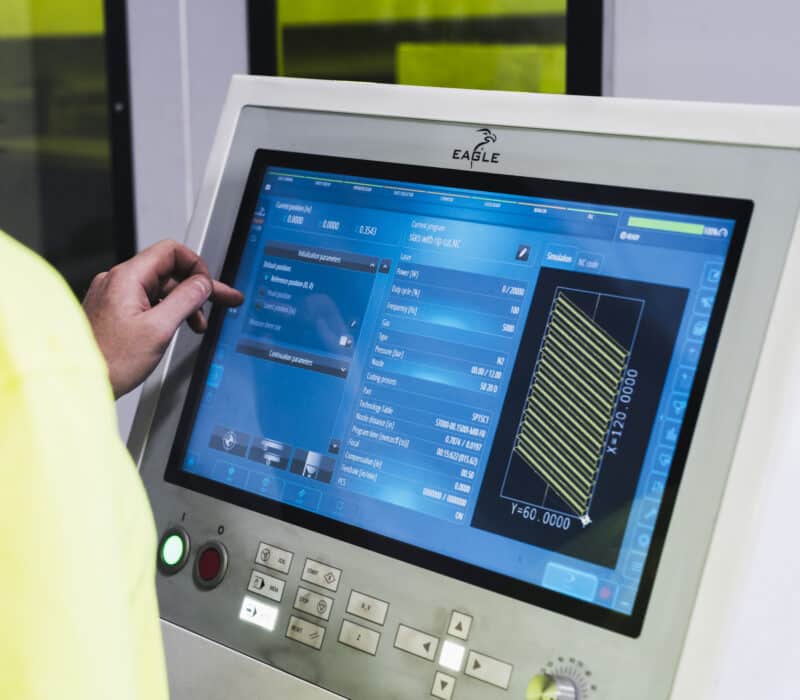
Key Learnings
Implementing smart manufacturing technology affects both upstream and downstream business operations.
“In the century we’ve been in business, there were times when you either moved forward or lost a potential opportunity,” Peter reminisced. “We have good people, loyal customers and love what we do. That’s a recipe for success.” With that in mind, Peter always keeps his eye on the horizon, and is already planning for HMW’s next 2 steps forward. One of those is the implementation of a robotic welding system, and the other is big data and analytics. “Production monitoring and automated job quoting are just 2 of the things data analytics can do for us,” he said. “It also can also help us monitor capacity utilization at all the machines, individually or simultaneously.”
Over the years, HMW has built a workforce with “aptitude and attitude,” Peter’s blueprint for employee and business success.
One employee—Brandon—demonstrated these traits to succeed with the new fiber laser. He quickly got a handle on the new tech and learned how to run parts on the new machine. Additionally, HMW worked with Ivy Tech Community College and the local chamber of commerce to access the trade schools. “We’ve hired 4 or 5 employees through those programs,” Peter said. “I look for people with aptitude and attitude. People who have those 2 traits together are hungry to learn, love to be challenged and ask tough questions. “If they’re not asking questions, they’re just going through the motions. Our culture is such that we try to keep the energy up, keep the workforce curious and balance that with some challenge. That’s how you keep the team performing at an optimum level.”
“We have good people, loyal customers and love what we do. That’s a recipe for success.”
Peter Nau
President and CEO at Hammond Machine Works
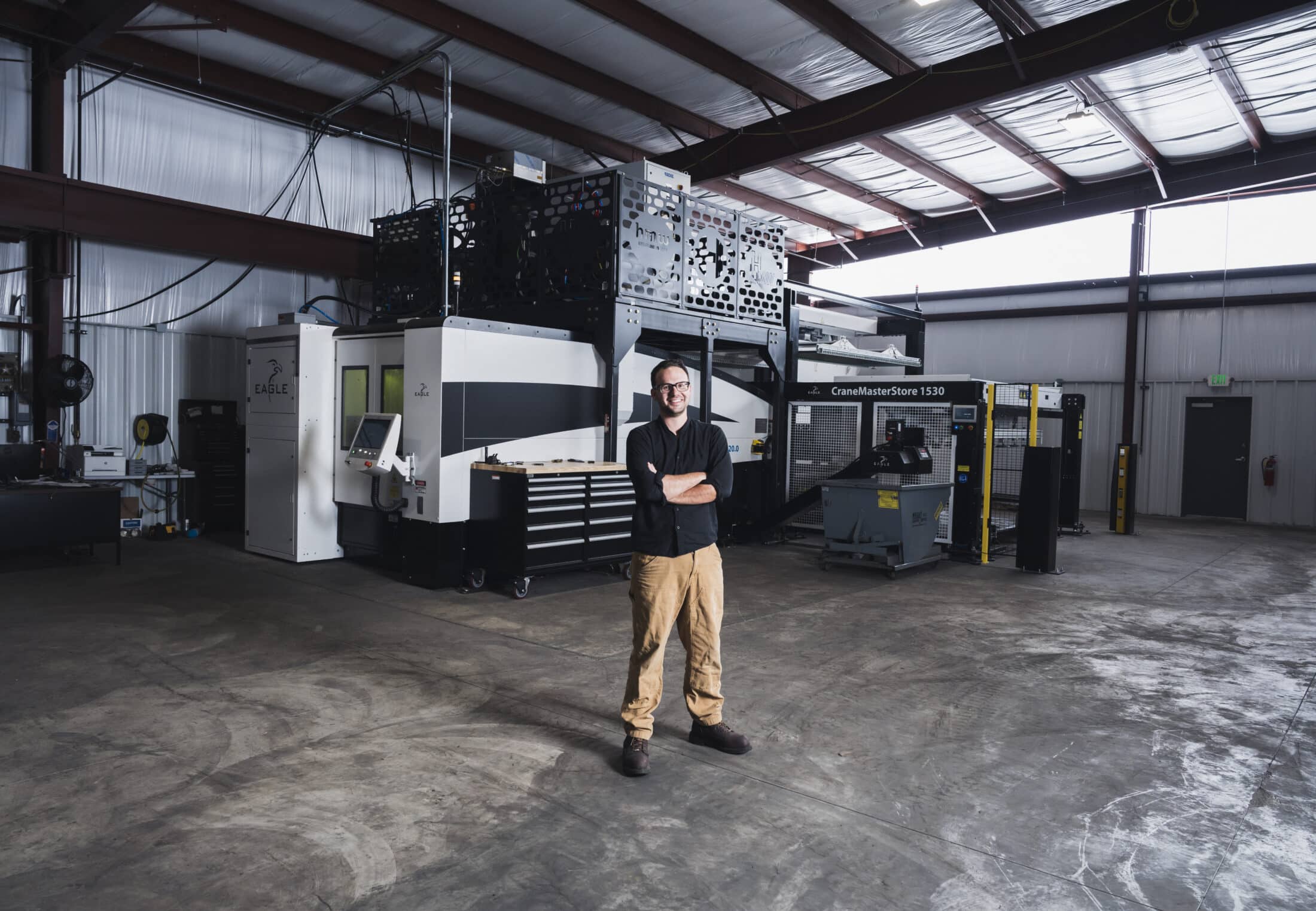