Lippert Makes Large Investment in Automation to Upgrade its Bristol Facility with Support of a Manufacturing Readiness Grant
Lippert
Case Study
Key Stats
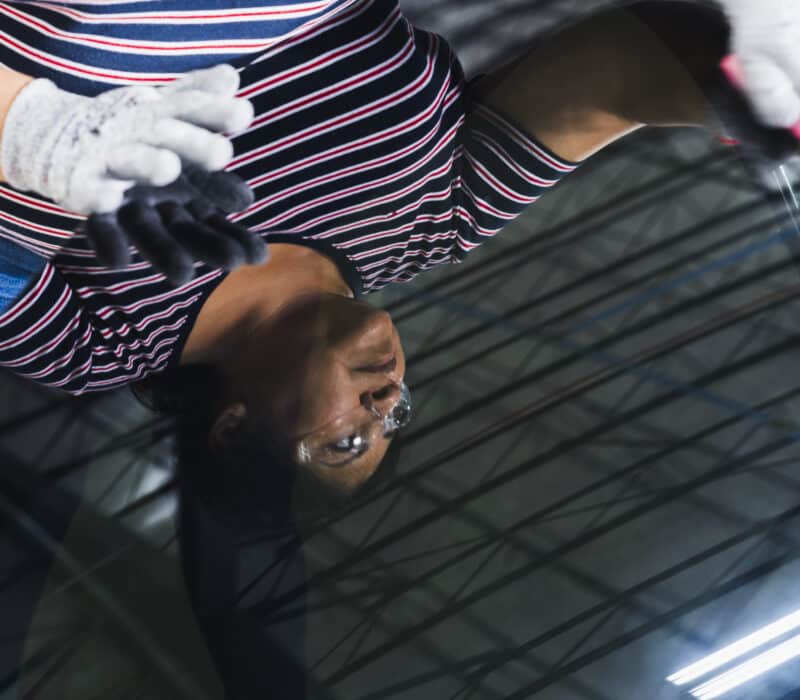
Company History
Lippert continues decades-long legacy of manufacturing components for the recreational vehicle, manufactured housing, trailer, bus, marine and heavy truck industries.
Lawrence (Larry) Lippert co-founded a galvanized and aluminum roofing business for the manufactured housing industry 67 years ago in Elkhart, Indiana. Just a year after Larry and a partner established their small business in Northern Indiana, the partner sold his interest in the company to Larry. Since then, three generations of the Lippert family have shepherded the company to its current international reputation as an industry leader of premium components in the recreational vehicle, manufactured housing, trailer, bus, marine and heavy truck industries. Today, Lippert Components, Inc. (Lippert®) has a global presence and more than $5 billion in annual revenue. Of the company’s 120 facilities around the world, over 80 are in the U.S. (approximately 50 in Indiana) with others in Canada, Mexico, Africa, Europe and Asia.
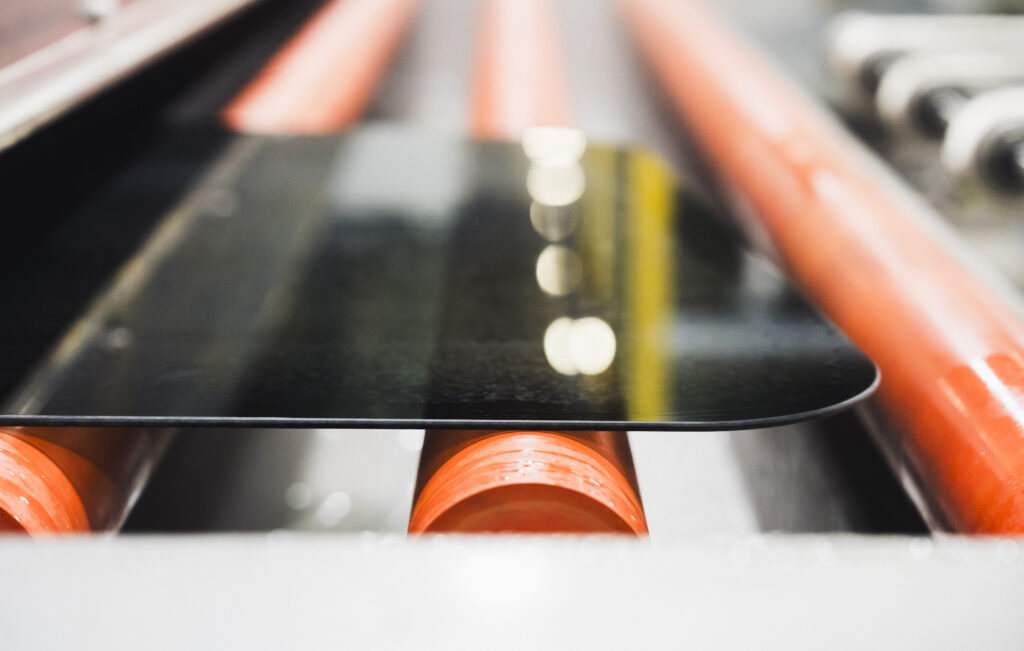
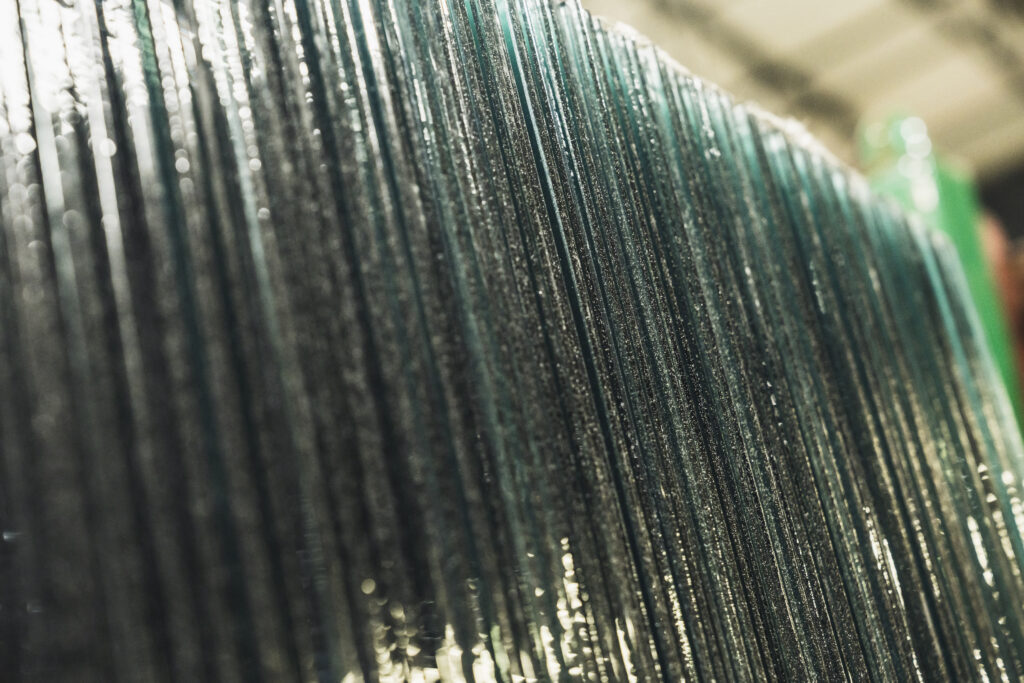
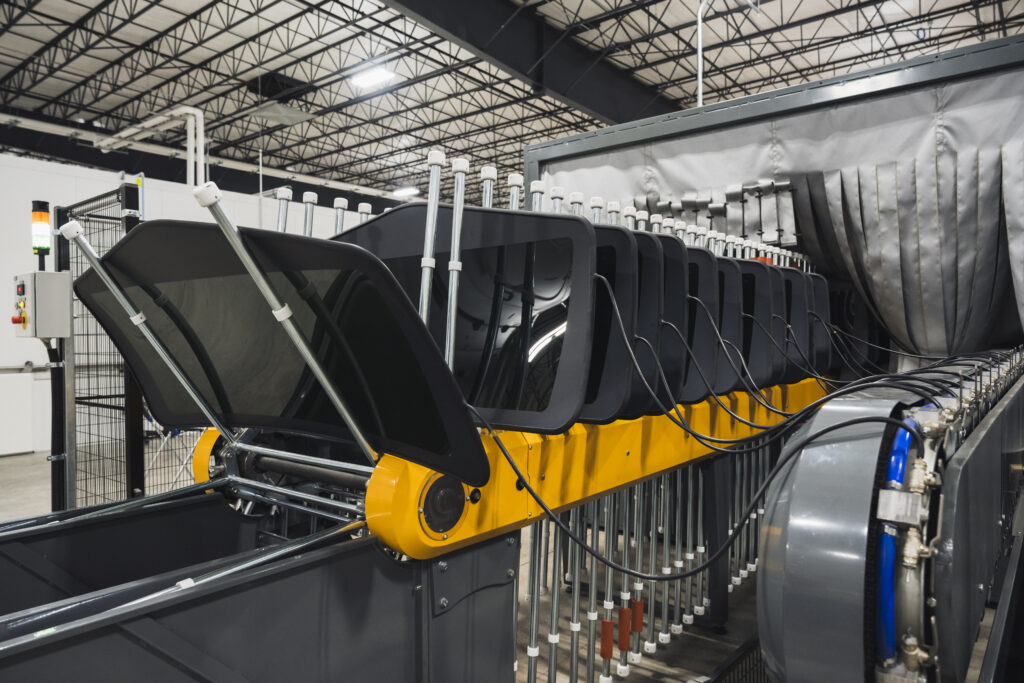
The company credits its success to a commitment to put people first, and a worldwide workforce of more than 12,500 stands as evidence of that commitment. Over half of those employees are in Indiana. The Bristol plant is in a South Bend suburb and processes more than 20,000 square feet of glass every hour, but even more growth is planned on the heels of this smart technology investment.
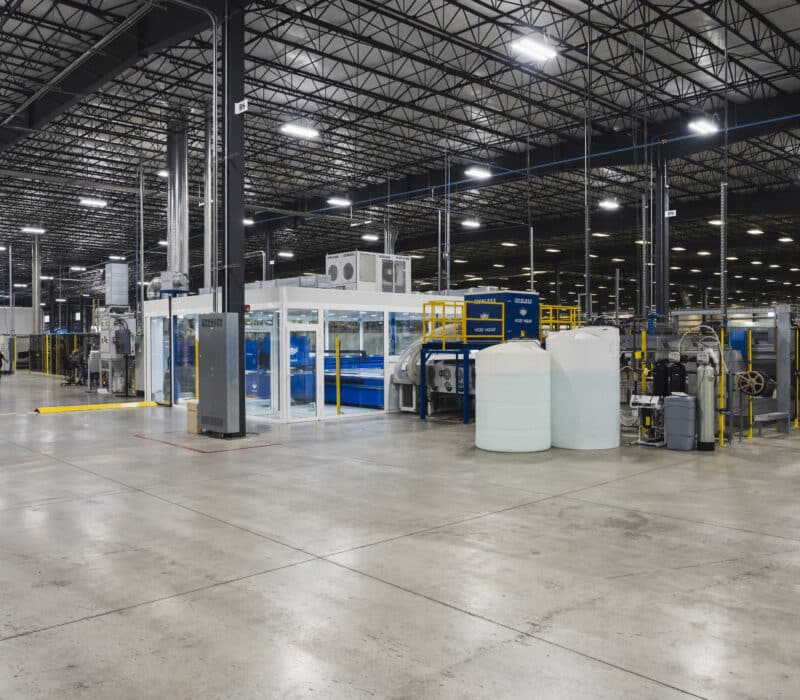
The Project
The unique way Lippert connected the new software, hardware and machinery used in the automated production line is now the ‘secret sauce’ in its glass manufacturing process.
Lippert Vice President of Glass and Transparent Plastics Tim Widner painted a picture of the project as one piece of a total project investment of $60 million on the horizon for the global enterprise. The specific project supported by the MRG is the system built to consolidate, under one roof, Lippert’s business related to glass and transparent plastics. “We’ve developed a highly automated glass manufacturing plant,” he said, “using advanced software for maximum raw material utilization and minimal waste.” The array of equipment includes glass cutting; high-tech CNC fabrication and water-jetting allowing tight tolerances, unique shapes and complex geometries; digital printing from detailed designs to realistic replications of marble, ceramic tiles and more; and proprietary glass tempering and furnace operations that can form complex shapes with superior optical clarity. Our connected and automated system moves each job seamlessly through the production line. “If you were to go into the Bristol plant and compare it to one of our legacy plants, you’d see they look entirely different from a cleanliness and organization standpoint,” Tim said. “Cleanliness is crucial. Anything that can affect sensors and communication is crucial.”
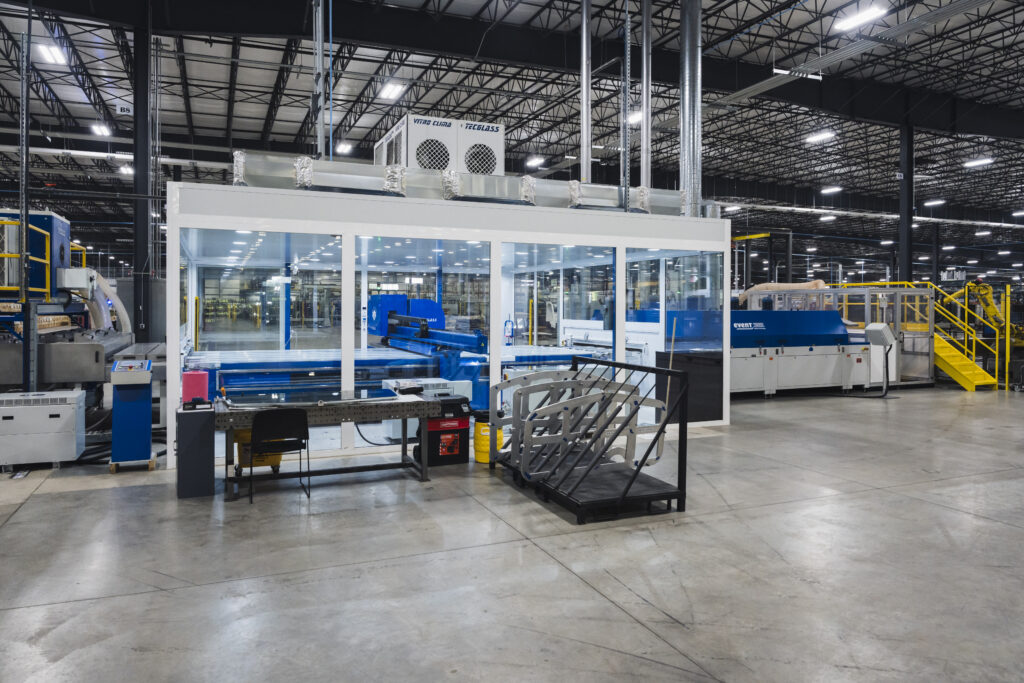
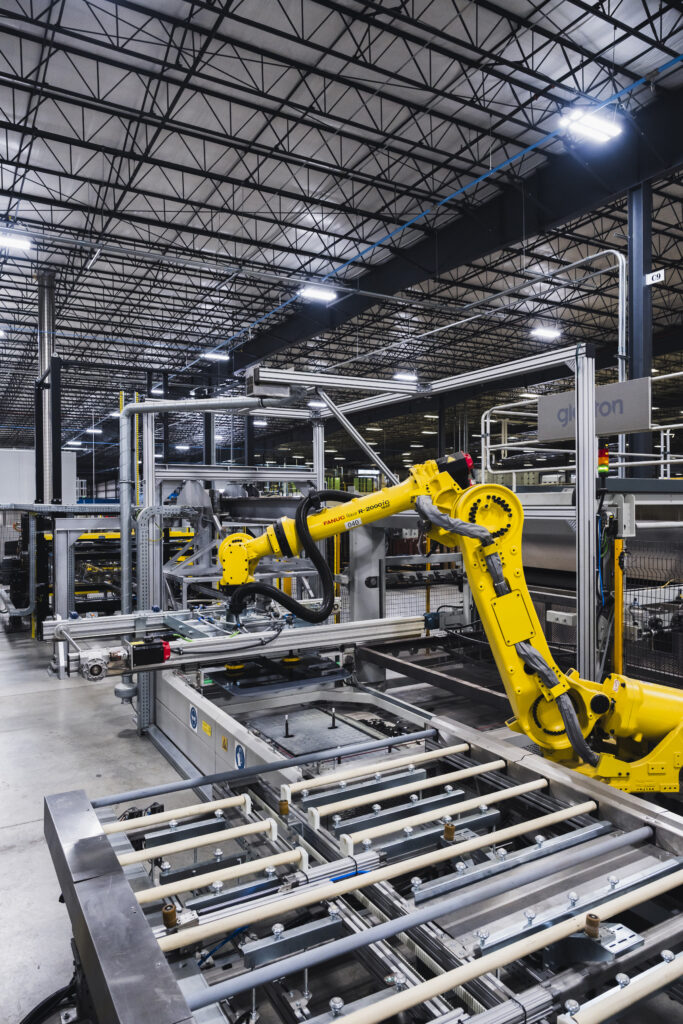

He stressed that the Bristol plant’s technology transformation is a “long game” for the company. Lippert plans to continue upgrading to transition the plant from a manual labor company to a highly automated operation. While the broader goal is productivity and profitability, Lippert is working toward a plant that will attract talent, retain employees and grow with customers for the next 15 to 30 years. “We want to expand our capabilities into other markets that are adjacent to our primary RV and marine markets,” Tim said. “We’re looking toward entering a much broader range of industries, and the ability to increase our production 100- to 200-fold over one of our traditional plants is key. Automation adds the firepower to compete in those new markets.” As an example, he pointed to a recent contract that brought in Point of Purchased cooler doors as a product. “We weren’t in that industry prior to this plant. Now it’s something we do.”
“While the software and equipment used in this project are not custom or proprietary, it’s the way the system works together. It provides us a suite of capabilities and each piece communicates intelligently back and forth,” Tim said.
Manufacturing Readiness Grants (MRG) provided by the Indiana Economic Development Corporation and administered by Conexus Indiana are available to Indiana manufacturers willing to make capital investments to integrate smart technologies and processes that improve capacity and productivity. A $100,000 Manufacturing Readiness Grants award contributed to Lippert’s large investment in automation for its glass production line in Bristol, Indiana.
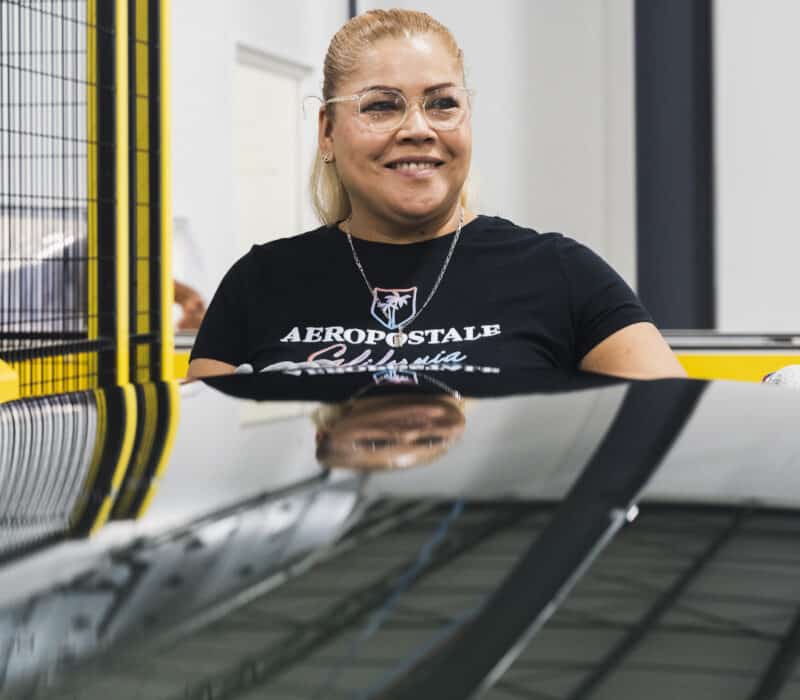
Key Learnings
You must invest in yourself and in new technologies to maintain your legacy.
The automation project for the glass manufacturing plant was a major investment for the company — more than $86M — and involved a great deal of time, money and workforce training. “Technology transitions are always tricky to manage and navigate,” Tim said. “But when you add the complexities of something like a global pandemic, the ROI calculation and implementation timeline is dramatically different.” Lippert already has over 60 years of experience with technology adoption and has navigated the 3rd Industrial Revolution. “Fortunately, Lippert is a size that perhaps can weather unprecedented events better than small- or mid-sized manufacturers,” he said. “You can invest in the right equipment, you can invest in the right people, and you must have the staying power to see it through and execute it well. We know that we’re building something that’s going to attract people and employees and customers for the future, not just right now. It’s a long game for sure.”
The revolutionary change in how Lippert produces glass in Bristol won’t eliminate workers, but it will change how employees work day-to-day.
“Adapting to the challenges our workforce faces in a high-tech environment, calls for different skills,” Tim explained. “Blue-collar factory work has always been seen as hard work, manual-intensive labor. With new technology and automation, we’re not asking people to do that. We’re asking them to bring critical thinking and problem-solving skills.” Concentration is essential to ensure the equipment is functioning properly and automated systems require persistent troubleshooting.

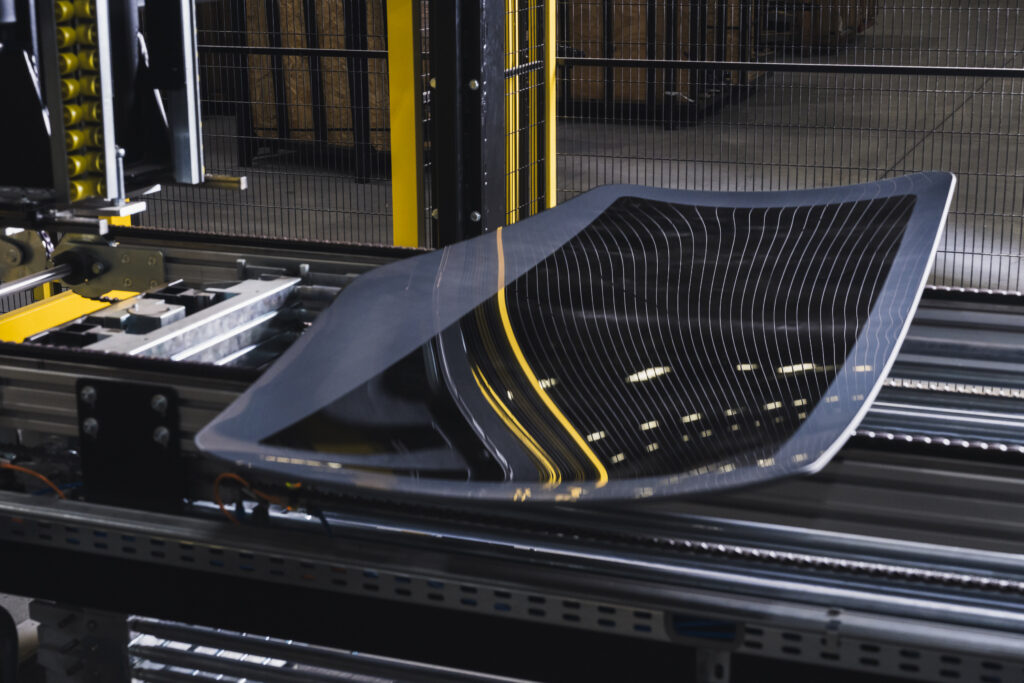
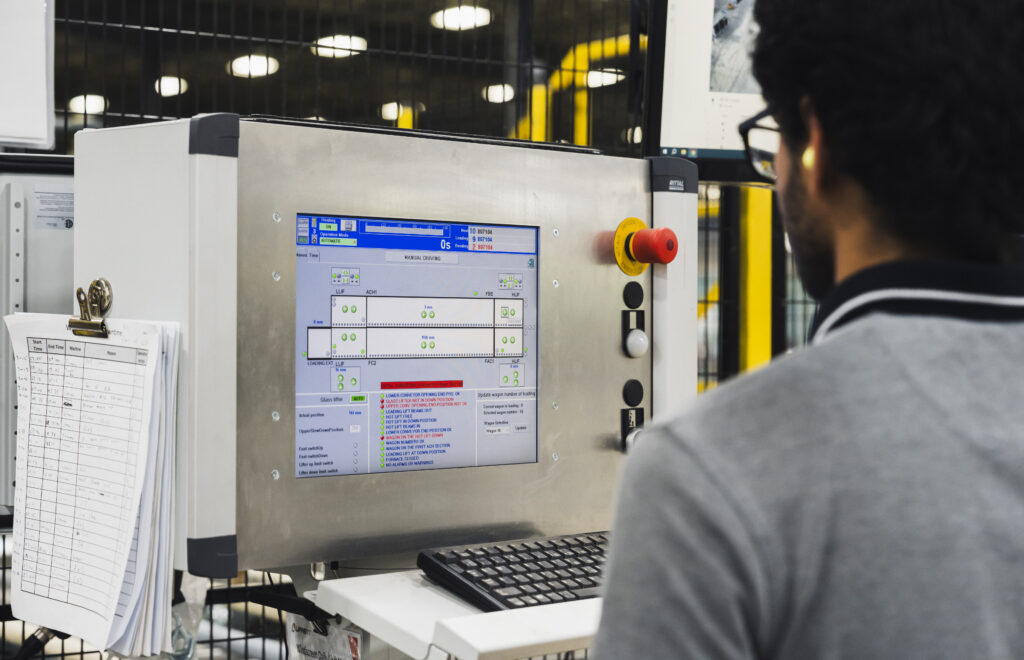
Other benefits to automation are more subtle but equally appreciated. The fully automated plant is a safer environment. “It’s cleaner, more organized, more environmentally friendly,” and Tim continued, “No matter who you are or where you’re from, if you can bring problem solving skills to our environment, you’re going to thrive.”
In the Bristol plant, people from all walks of life collaborate with one another. Degreed engineers work on the floor next to trade school or high school graduates. Most workforce training at Lippert is through the company’s own education system. A skills training program is provided and offers the opportunity to “test” and “certify” into certain jobs. With those skills comes higher wages. The company also has a long-standing series of one-on-one and group training opportunities: A rotation-styled Leadership Training Program kickstarts the leadership experience providing trainees with unique culture and product-based training. The Mentoring Program, Coaching Program and Lippert University Series and Courses are each designed to equip employees with additional digital and tech skills. The Dream Achiever Program is described as a journey of personal coaching, with an emphasis on developing a productive mindset toward achieving personal career goals. Additionally, Lippert team members develop meaningful relationships with each other to create a unique system of support.
“We want to expand our capabilities into other markets that are adjacent to our primary RV and marine markets.”
Tim Widner
Vice President of Glass and Transparent Plastics at Lippert
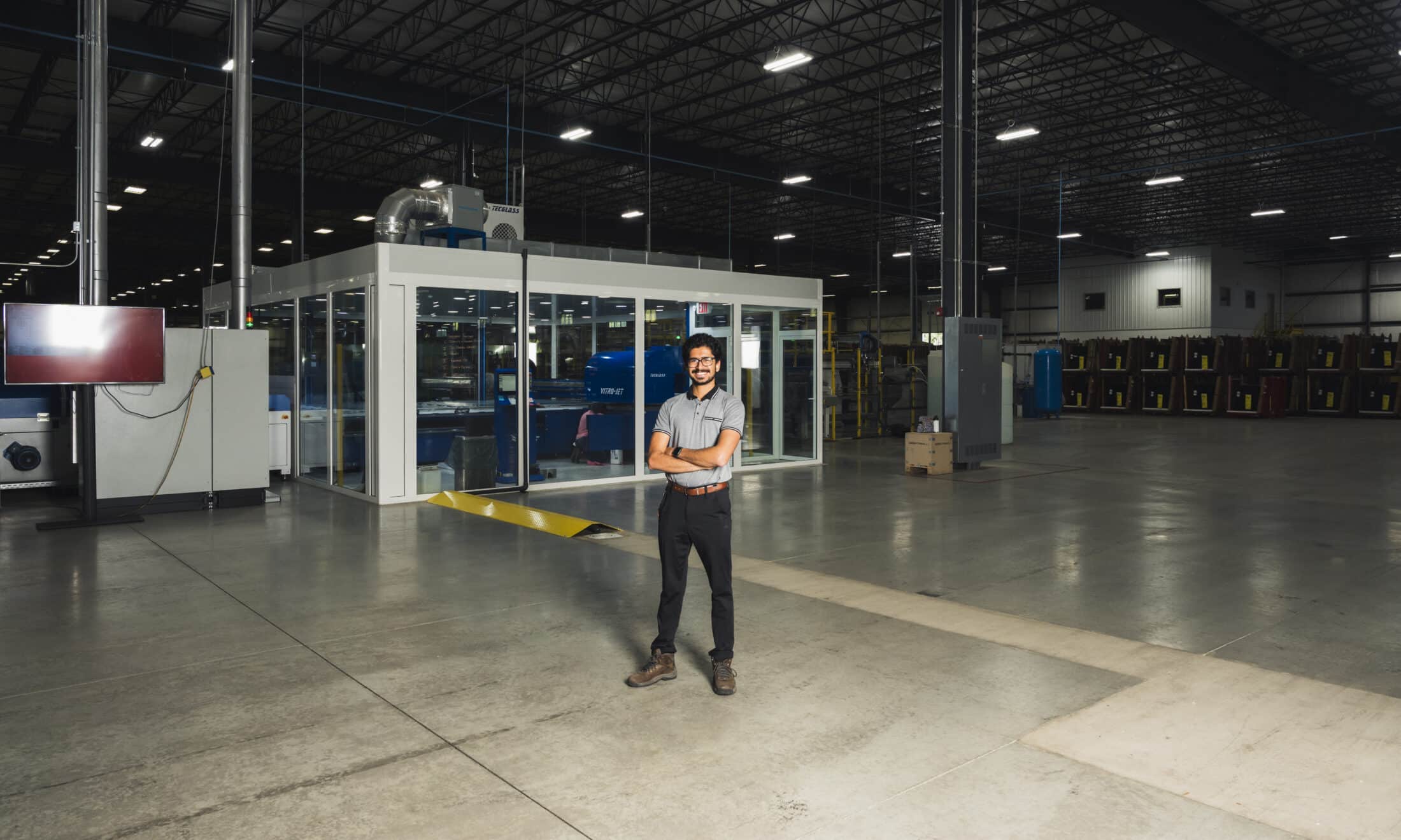