Marion Manufacturing Increases Its Competitive Edge by Digitizing Product and Quality Inspection Data
Marion Manufacturing
Case Study
Key Stats
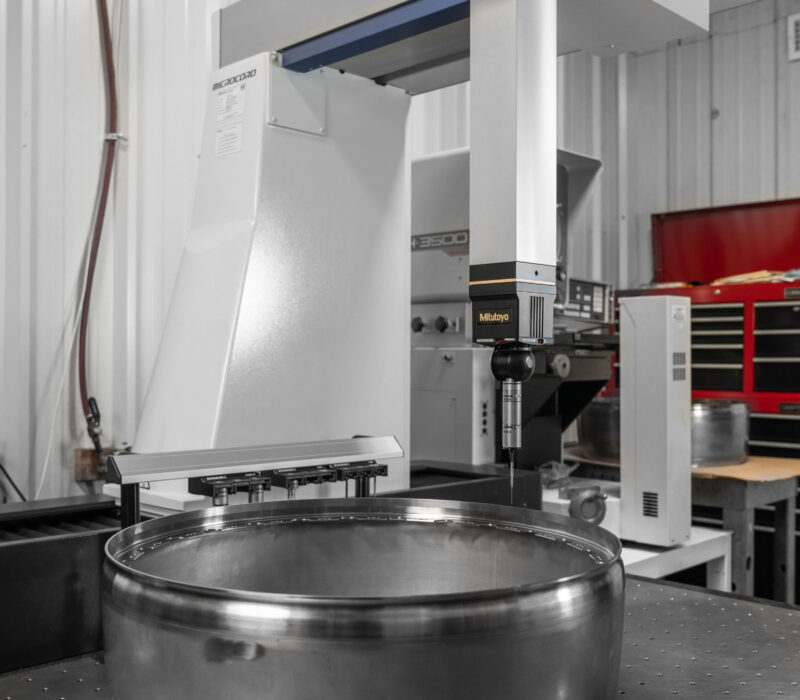
Company History
Marion Manufacturing grew from a 22’x22’ garage in 1996 to a high-precision CNC machining operation serving the heavy equipment, fluid systems, energy, agriculture, defense and aerospace industries.
Tamara (Tammy) Marion was one of five family members who founded Marion Manufacturing 26 years ago in West Terre Haute, Indiana, along with Babe, Carole, Timothy and Leonard. Today the company remains family- and women-owned, and retains three family members in senior leadership. Tammy became the company’s general manager in 2001 and acquired 34% ownership and the role of president in 2008. In the intervening years at Marion, Tammy led her team to increase annual revenue from six figures well into the millions. Tammy’s husband, Tim, and Leonard, also original owners, continue in leadership positions—Tim as vice president of innovation and technology, and Leonard as vice president of sales.
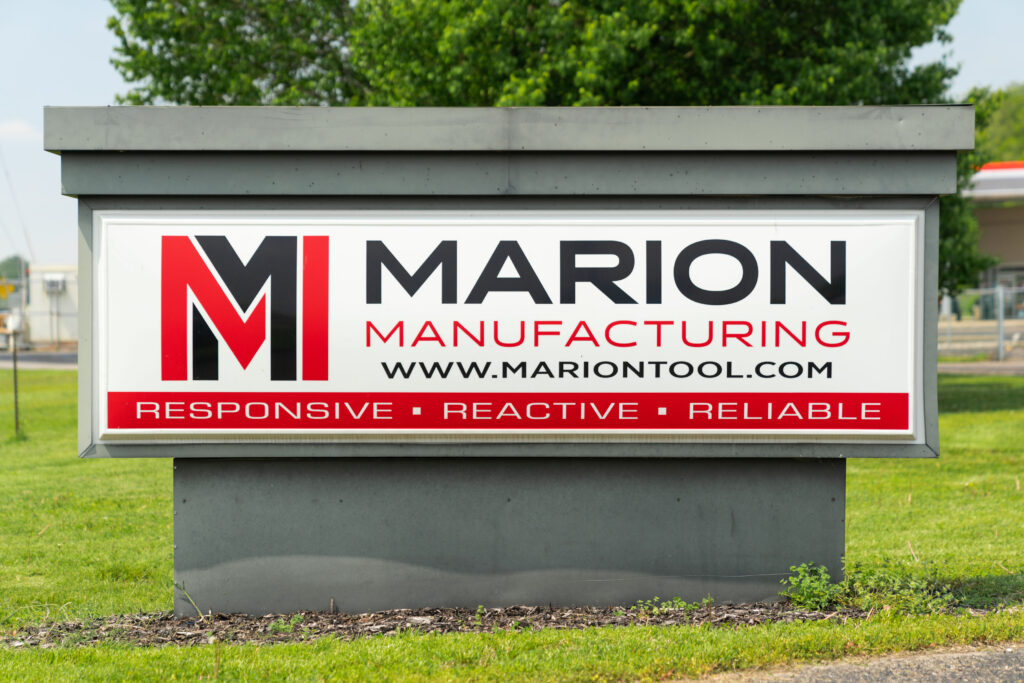
In 2008, Marion expanded its West Terre Haute distribution footprint with a 24,000-square-foot addition to house a new automated robotic cell and CNC lathes and mills. In 2015, the company merged with Morton Machining increasing employment to 80 people and adding a Morton, Illinois, location. Today the company employs over 130 people and is recognized as an industry leader in high-precision CNC machining operations for aerospace, defense and infrastructure.

The Project
What started as a technology adoption project to digitize data entry and inspection capabilities will ultimately develop into a strategic roadmap.
Marion Manufacturing had its sights set on moving the company’s physical binder to a digitized system that hosts information about individual parts—from dimensional specs to quality assurance and other product information. The impact on the manufacturing process would be significant as employees would no longer need to haul a physical binder around the shop floor on each part; rather, they could access work instructions on a convenient mobile tablet and record inspection details on that same device.
“We started on the shop floor because there was still a lot of paper involved there,” Tammy explained. “Before we began this program, when a job went to the floor there was a binder—all paper—and all work accomplished was recorded on paper and added to that binder. Now we’ve started integrating digital binders in a testing phase. Employees can pull up prints with a tablet and all the instructions and the inspection plan are built in.” But that’s just the beginning, she said. “We started with the IT piece as well as cybersecurity, and now we are working on robotics to help address workforce challenges and skill up our current workforce.”
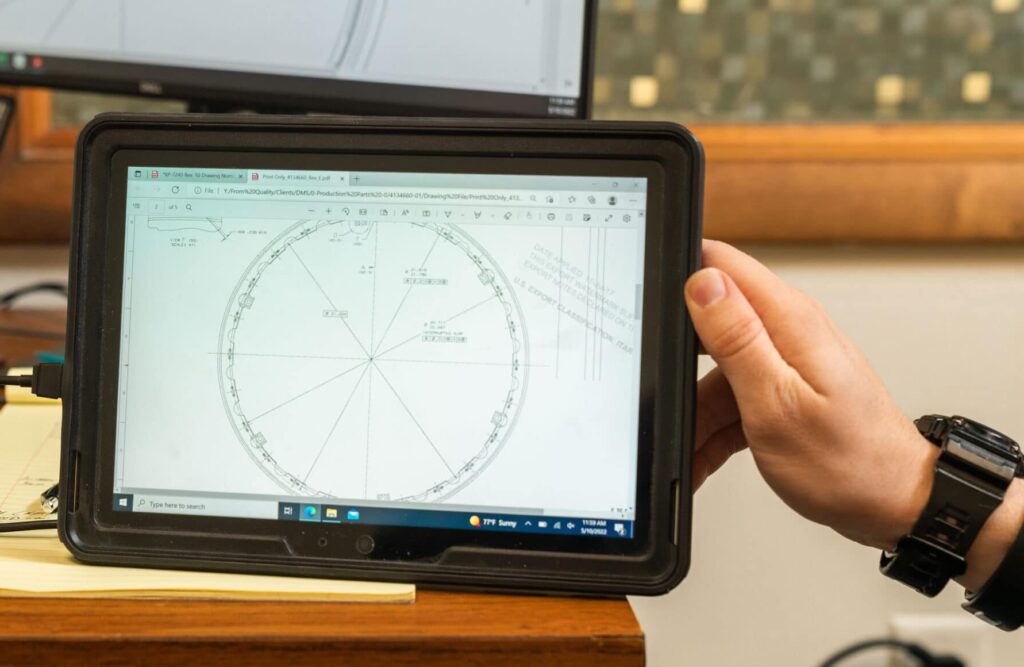
Explaining the impact of the project, Tammy said, “In our aerospace and defense department, we’re working on anywhere from 90 to 120 new product introductions at any given time. To process the data manually, create the binders, check and recheck sheets and spreadsheets was killing productivity. We would never be able to handle additional volume without this technology adoption project.”
Cybersecurity investment is another vital part of Marion’s strategic roadmap.
Along with the digitized product information, the Cybersecurity Maturity Model Certification (CMMC) is an essential part of Marion Manufacturing’s strategic roadmap. With cybersecurity threats on the rise, companies must increasingly adhere to strict cybersecurity standards to work with confidential Department of Defense and aerospace information. According to a recent Congressional Research Service report (Sept. 9, 2019), the certification determines the maturity of a provider’s cybersecurity initiatives. While Marion was already on the certification ladder, company leadership wanted to be at level 5, the highest certification. Level 5, in short, includes proactive software systems to detect and mitigate threats before they become a problem.
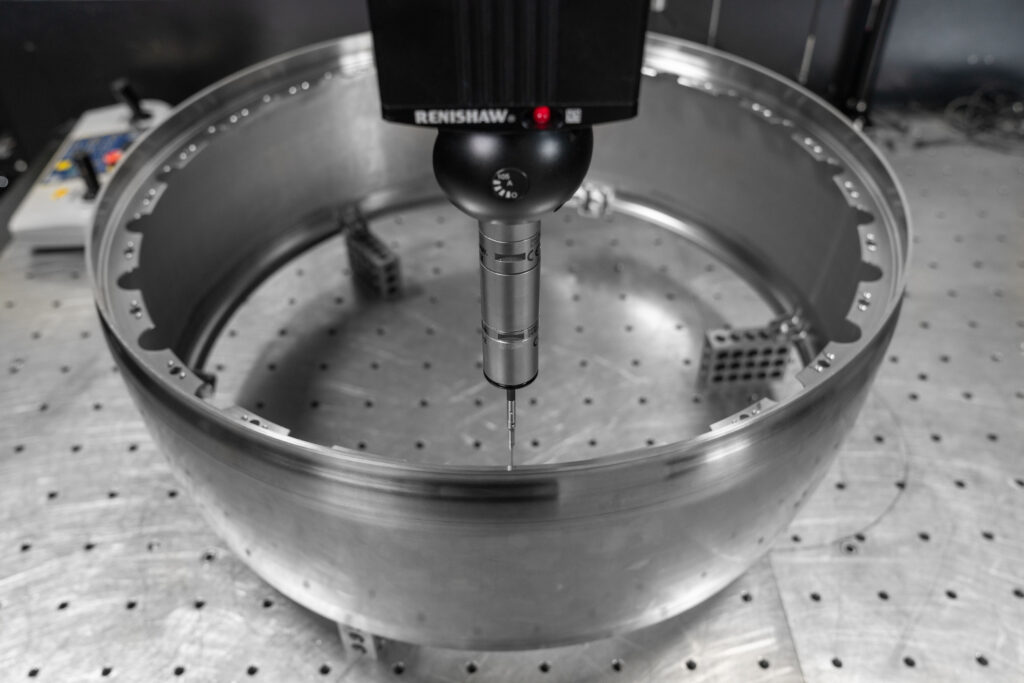
To ensure success of the cybersecurity certification project, Marion has been working closely with a local partner, Purdue MEP (Manufacturing Extension Partnership), on compliance requirements to achieve its goal of the Level 5 certification. The partnership with Purdue MEP ensures Marion Manufacturing remains on the cutting edge of regulatory expectations for its defense and aerospace customers and establishes systems to monitor and identify potential threats in Marion’s enterprise network.
Manufacturing Readiness Grants (MRG) provided by the Indiana Economic Development Corporation and administered by Conexus Indiana are available to Indiana manufacturers willing to make capital investments to integrate smart technologies and processes that improve capacity. Marion Manufacturing was awarded grant funding to digitize its product data, inspections and quality assurance, and increase its competitive edge.
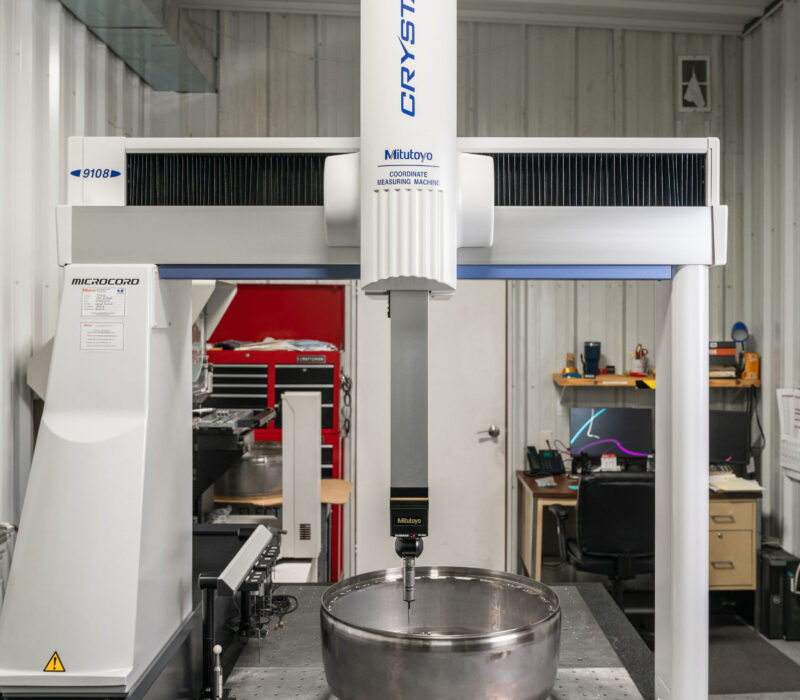
Key Learnings
At first, there’s some resistance in the workforce, followed by excitement and increased job satisfaction.
“Anytime there is change, there is a little bit of resistance,” Tammy said. “But for the most part, people are excited about the new technology we’re introducing.” She recalled that automating the payroll system so employees could print their own pay stubs required a dedicated workstation just a few years ago. “It was for people who didn’t have a cell phone or smartphone, or a computer at home,” she said. The project has not only increased employee satisfaction, but it has also increased a sense of growth and success among the workforce, Tammy said.
Digitizing product and inspection data increased Marion’s customer responsiveness and the cybersecurity investments continue to grow new business.
Measuring the success of the project can be done in many ways, Tammy said. “Capacity, efficiency, quality. Those are all measurements of success,” she said. “But it’s really a combination of many things. The true test for us is when a customer calls in to see inspection data from the shop floor and we can go right into the software system and pull up everything, versus flipping through pages and scanning documents to find it. Our responsiveness is significantly improved.”
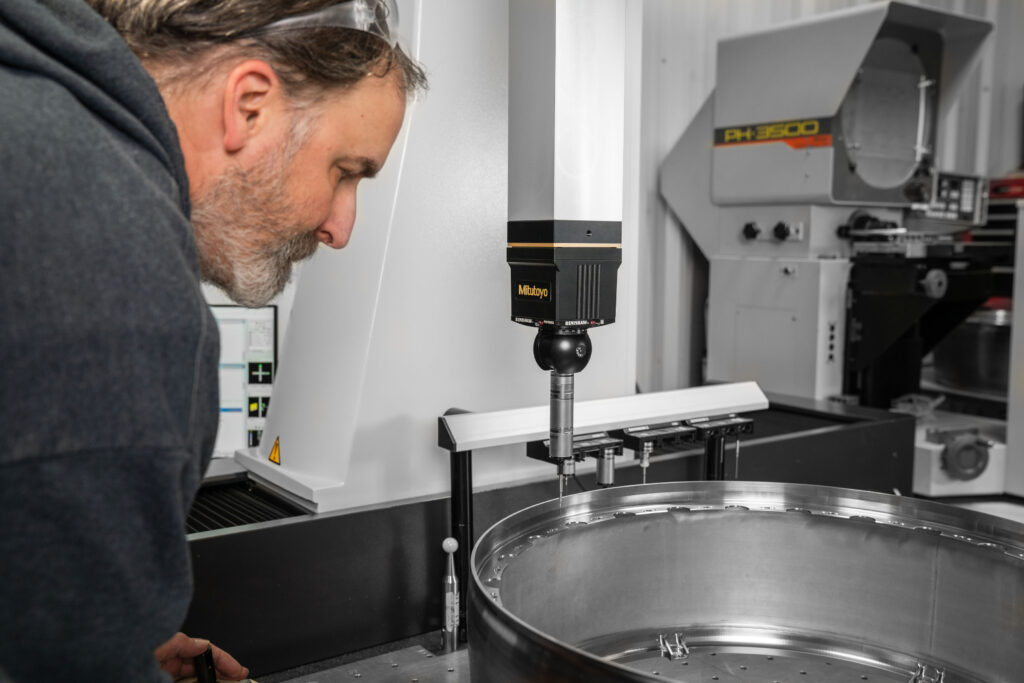
The ultimate measure of success though, is growing your business, Tammy pointed out. “In order to be a successful small manufacturer in the United States,” she said, “no matter how much some small business owners might resist, they’re going to have to comply with these cybersecurity regulations. Your business is not going to grow if you don’t. Building a workforce that understands how critical cybersecurity is to your operations gives your customers a sense that their information is secure with you… and that’s critical.”
“Building a workforce that understands how critical cybersecurity is to your operations gives your customers a sense that their information is secure with you.”
Tammy Marion
President at Marion Manufacturing
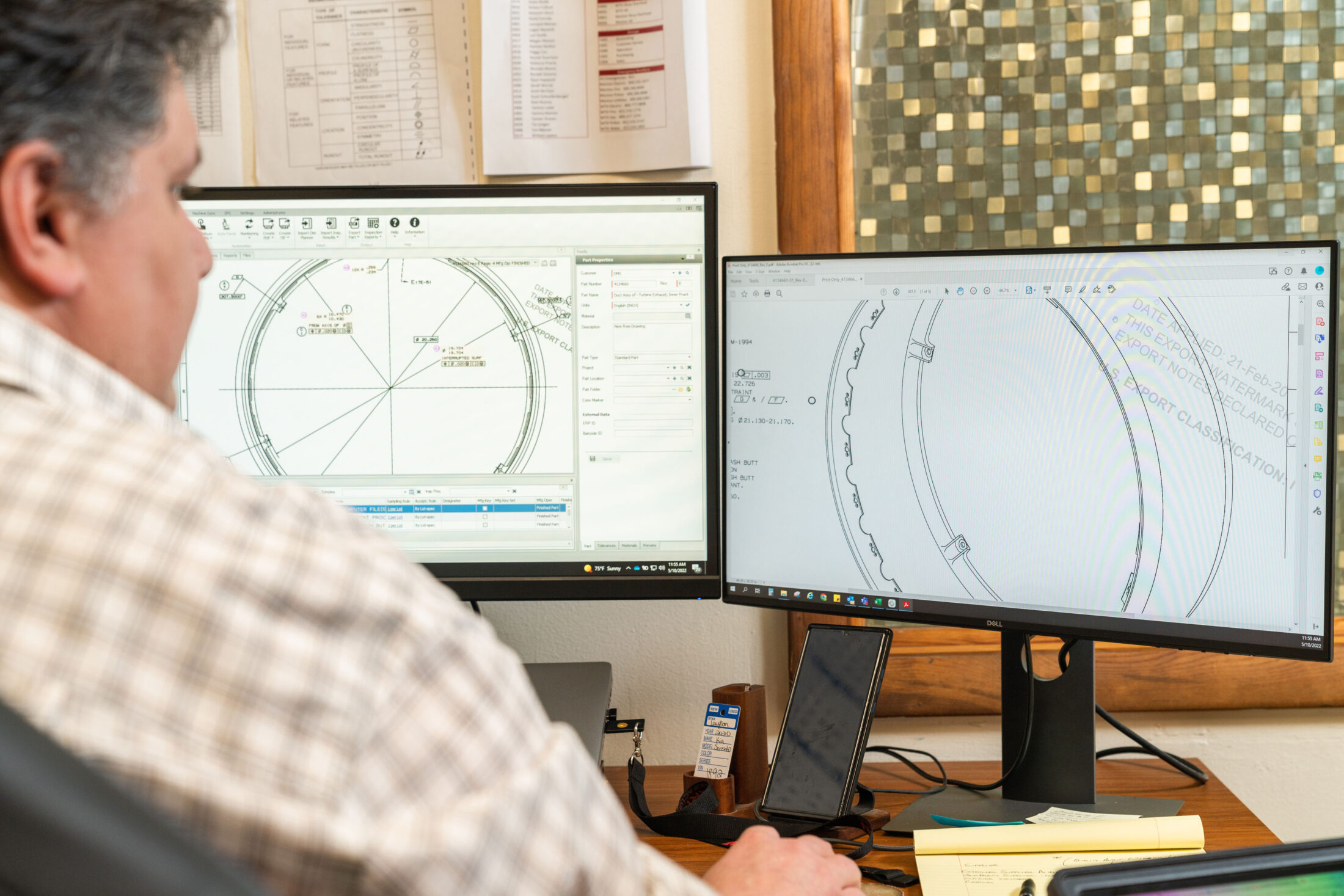