A Manufacturing Readiness Grant Helped Kick-start “Operation Phoenix,” MSP Manufacturing’s 4-phase Strategic Plan for Smart Technology Upgrades
MSP Manufacturing
Case Study
Key Stats
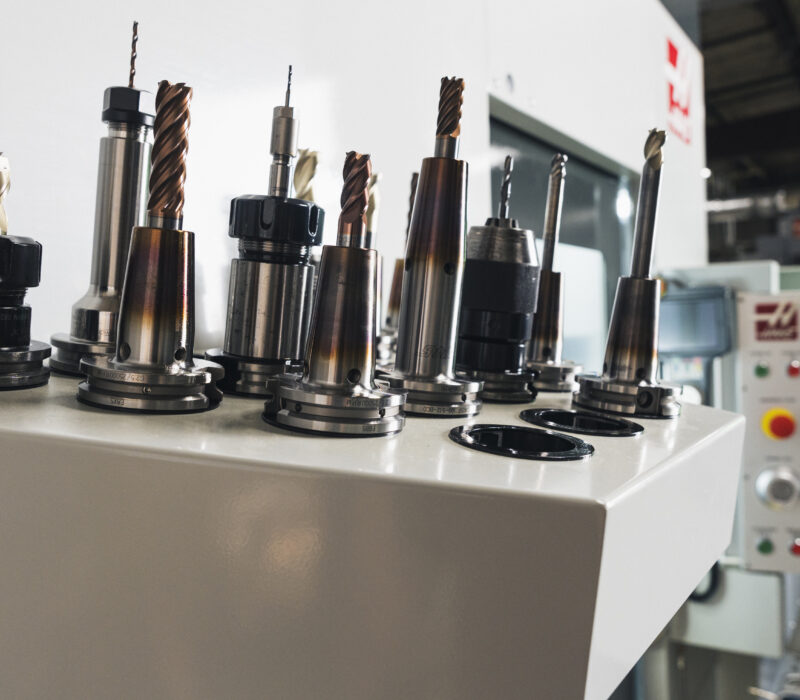
Company History
Building on its long history in avionics, MSP Manufacturing expands its portfolio to include armory, automotive, medical, military and sanitation products.
MSP Manufacturing’s history began in Marion, Indiana, in 1943 as Marion Screw Products, and for the next half-century, it expanded its role in Indiana’s manufacturing industry, becoming MSP Aviation focusing on avionics components—cases, clamps and assemblies. But the company’s present story really began in 2002, when John Goode purchased the business. By then it was operating from Gnaw Bone, a small community in Brown County, known mostly for its 3 flea markets and a reputation as the home of a nationally famous fried tenderloin sandwich. John moved the company to nearby Bloomington and added new product lines, building a solid reputation for excellence among corporate, commercial, general and military aircraft companies.
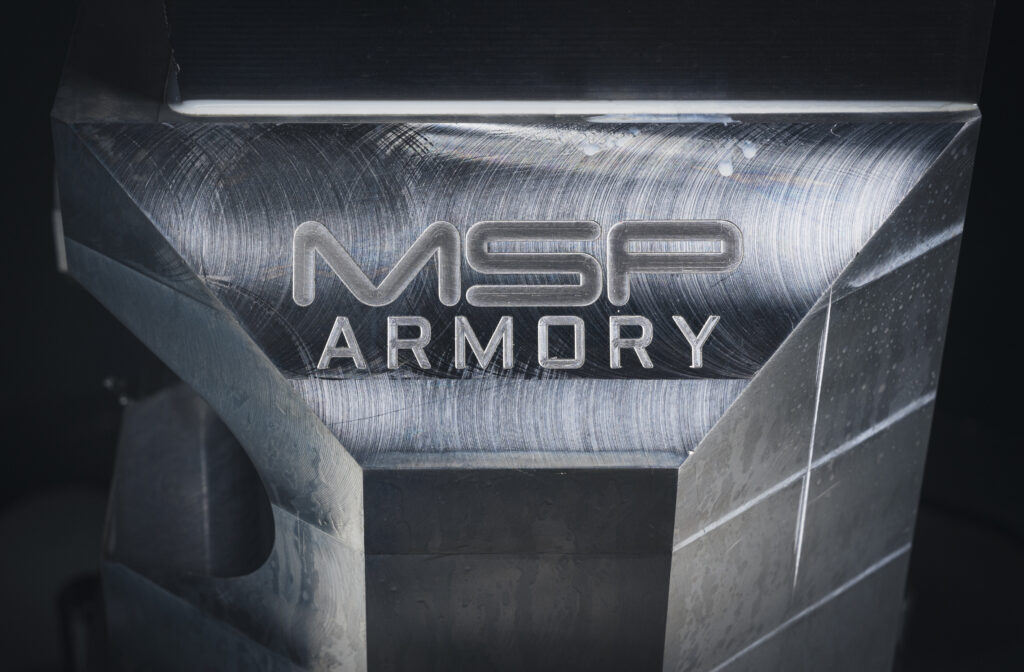
By the time John had transitioned into his current position as company chair and his son Johnny Goode became president and COO, MSP was doing business as MSP Manufacturing and was expanding its portfolio to include armory, automotive, medical, military and sanitation products. Along with that expansion came growth exceeding 1000% and quadrupling the workforce, all operating from the 25,000-square-foot Bloomington plant. Still, aviation remains a key element of MSP’s business, serving industry titans that include Boeing, Curtiss-Wright, Bell Helicopter, Cessna, Gulfstream and other major aviation leaders. Precision machined parts for these industry customers remain the company’s focus and strength.
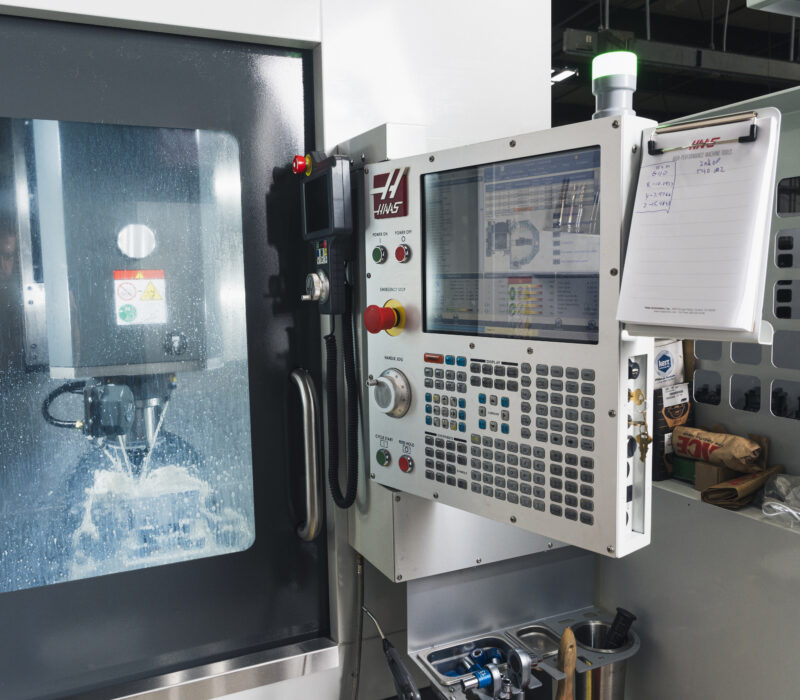
The Project
The name “Operation Phoenix” was intentional, signifying a bold new strategic plan to build a smart technology operation to better serve industry customers–it included a next-generation machine and new software packages.
The two Goodes developed a 5-year, 4-phase plan that included developing and expanding the company’s workforce and moving to adopt smart manufacturing technologies throughout the organization. They titled it “Operation Phoenix,” to signify the company’s intent to create a new and better way to succeed in the fourth industrial revolution. “The old technologies we were using were just not communicating well with each other,” Johnny said. “The data and know-how were all in one person’s head.” With its expanded customer base, it was important that MSP Manufacturing behaved like a large company in terms of its technology capabilities, while retaining the agility of a small company. “Just adding a new machine or two in the shop wasn’t going to get us to that level,” Johhny said. “Smart manufacturing would require a mix of next-generation machines and software systems that organize all manufacturing functions in a single place.”
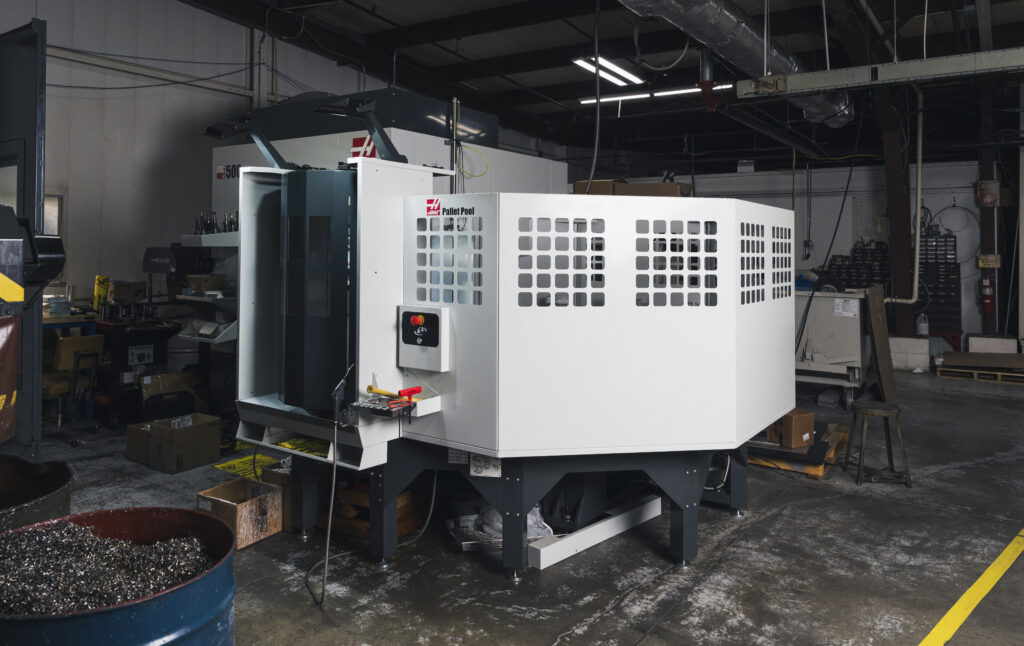
With the company’s focus on aviation and military and defense, those plans needed to include cybersecurity, too. MSP Manufacturing is currently certified at Cyber Maturity Model Certifications (CMMC) Level 1 and working toward Level 2 certification. The CMMC certification system, previously organized at 5 levels, is now just 3 levels, so the next step is an essential piece of the company’s certification process. All businesses in the defense supply chain must have CMMC certification. “It’s not something that happens overnight,” he said. “The next-generation machine was the biggest cost of the project, but by no means was it the project itself. It’s just one piece of the smart manufacturing and software integration puzzle.”
Manufacturing Readiness Grants (MRG) provided by the Indiana Economic Development Corporation and administered by Conexus Indiana are available to Indiana manufacturers willing to make capital investments to integrate smart technologies and processes that improve capacity and productivity. A Manufacturing Readiness Grant of $170,000 helped MSP Manufacturing introduce its 4-phase strategic plan for recovery as it emerged from the Covid-19 pandemic.
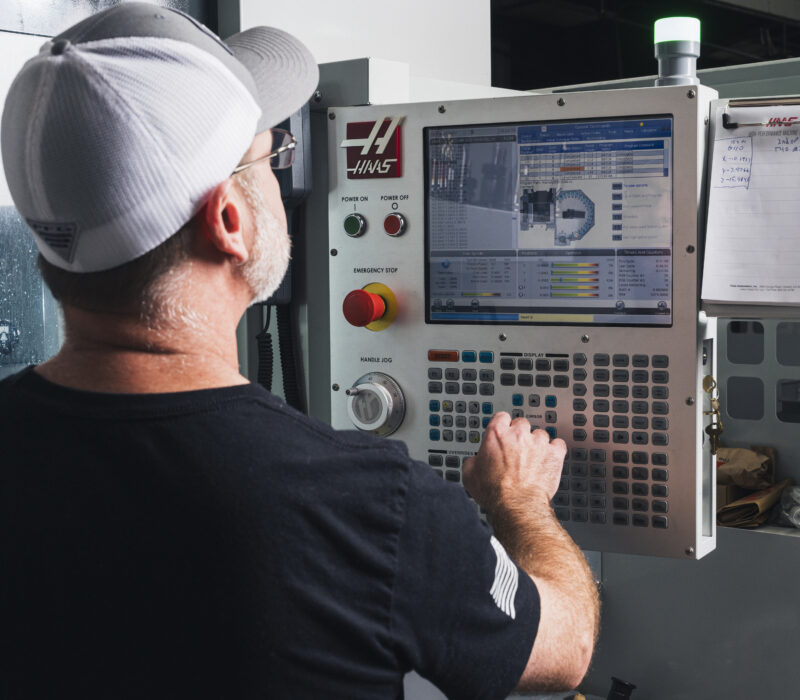
Key Learnings
Leverage the local ecosystem of technology providers and integrators to upskill the workforce and implement new technologies.
A consultant working with MSP was a source of workforce training and upskilling. The company connected with a workforce consultant through the Purdue Manufacturing Extension Partnership (MEP), and the consultant helped train and upskill the MSP Manufacturing programmers on the next-generation machines. “He was exposing us to different ways of thinking and reassured us that it was a misconception to believe that automation eliminated positions,” Johnny said. “We eliminated many of the tasks that our workforce doesn’t really like to do, and trained them on new responsibilities in production.
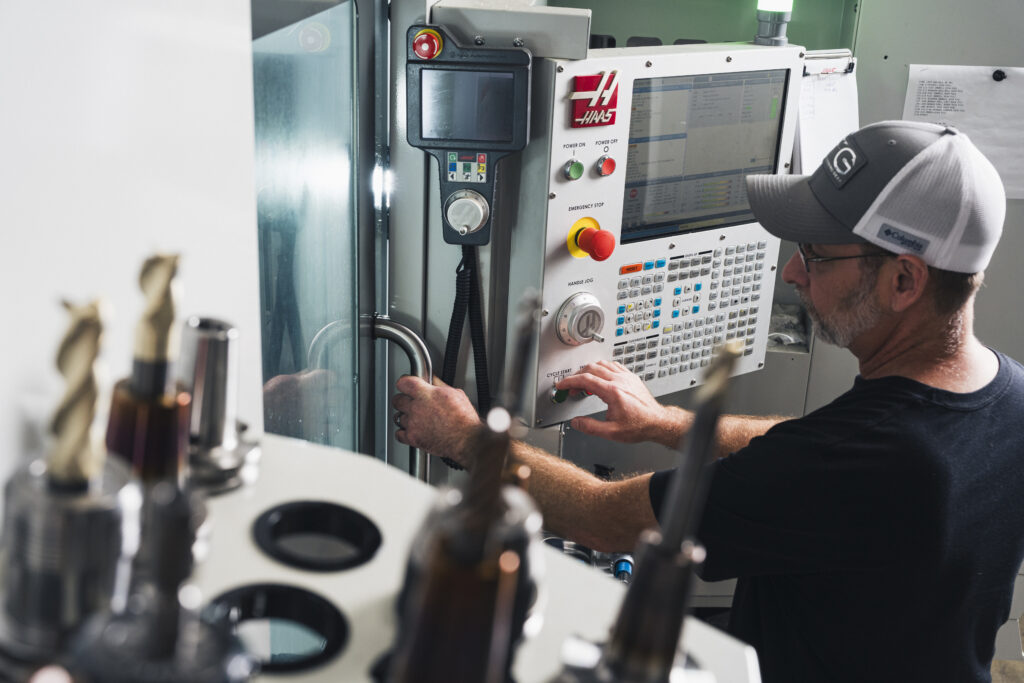
“It’s important to think strategically while you’re trying to take care of the day-to-day,” Johnny continued. He credits both the MSP leadership and its manufacturing workforce with the success of the project–the consultant showed the employees what was possible, and the employees recognized that the Goodes were willing to accept new ideas and technology. The workforce began to champion the new technology, and Johnny acknowledged that “a lot of it was driven by the employees. Researching and writing the application for the Manufacturing Readiness Grant and other funding avenues was my responsibility, but the employees were definitely a fundamental part of the project team.”
Training the workforce in the new software system was another essential piece of the project, and it involved working with Indiana’s education system—from the local high school to Purdue University.
Like most Indiana companies stepping into Industry 4.0, MSP Manufacturing didn’t develop its smart technology roadmap and strategic plan to reduce its workforce or eliminate jobs. It was designed to replace manual tasks and streamline operations. “It’s crazy to think we were manually typing data and scheduling the production runs,” Johnny said. “We have some 15,000 to 20,000 different part numbers, and nothing was being done with the data.” With the new technology and software systems in place, production runs are automated through the night. According to Johnny, “The entire workforce wanted it [the new technology] and wanted more opportunities to learn. We have a culture of trust that makes these projects easier. We were transparent with our team: ‘This is where we want to go, and this is how we’re going to do it,’” he said. These are large changes, and everyone must be on board, otherwise it can be a painful process, Johnny mentioned.
Ensuring the necessary training to help support the project—and each employee—was a critical part of the program. Much of it came through education programs with the costs supported by MSP Manufacturing. One example Johnny offered was an intern hired through the 21st Century Scholar program at Bloomington North High School’s Hoosier Hills Career Center in partnership with Ivy Tech Community College and Vincennes University. That program offers dual high school/college credit and industry-recognized certifications. “We funded everything other than his tuition—tools, books, travel and so on. He was one of our additional hires,” Johnny said. “We’re trying to build a workforce a pipeline not just for us, but for other local manufacturers who have a hard time finding the right people, too.”
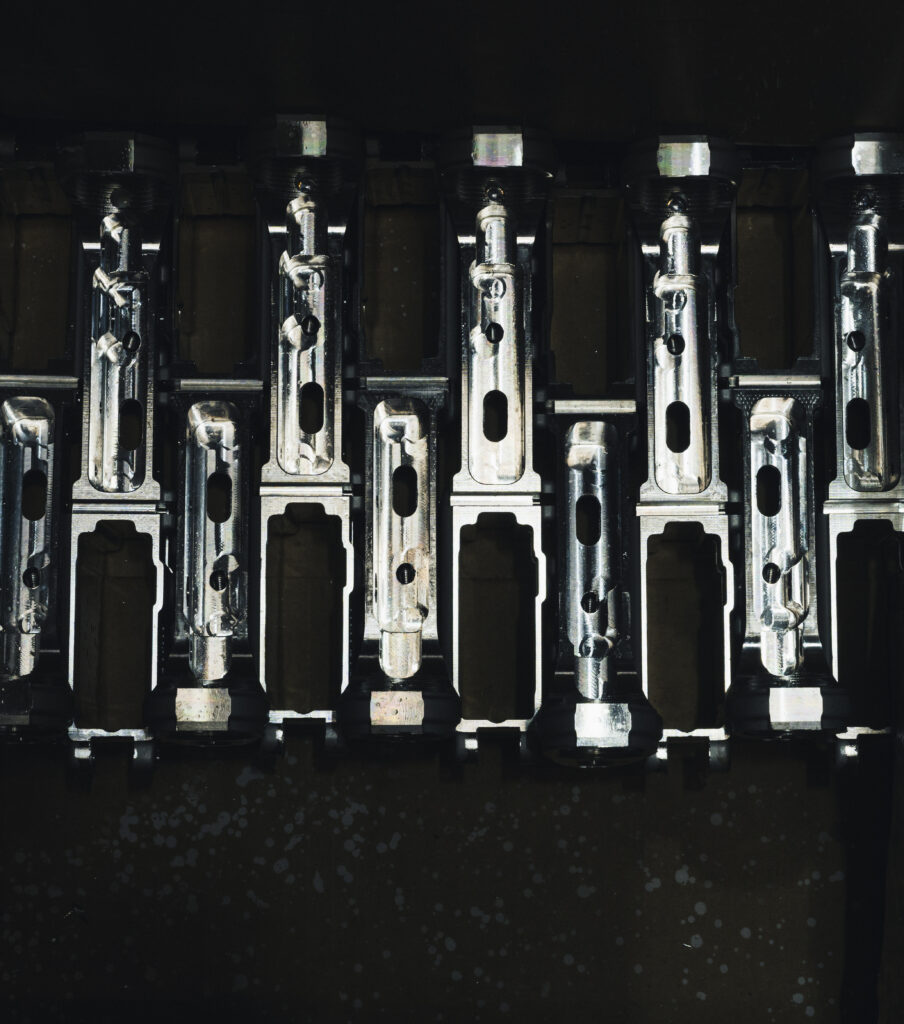
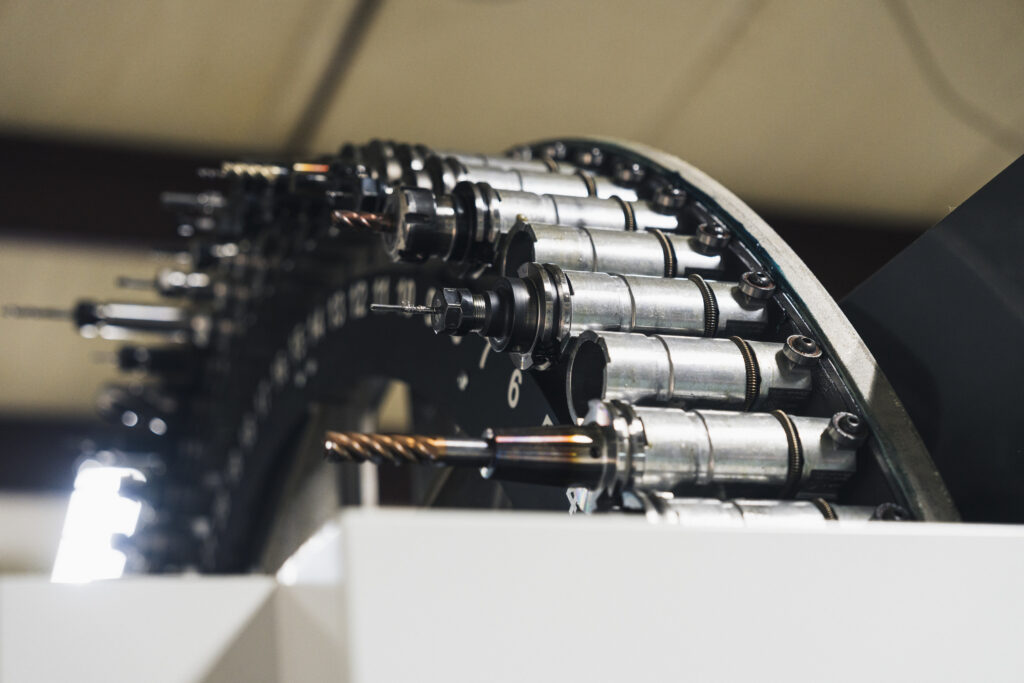
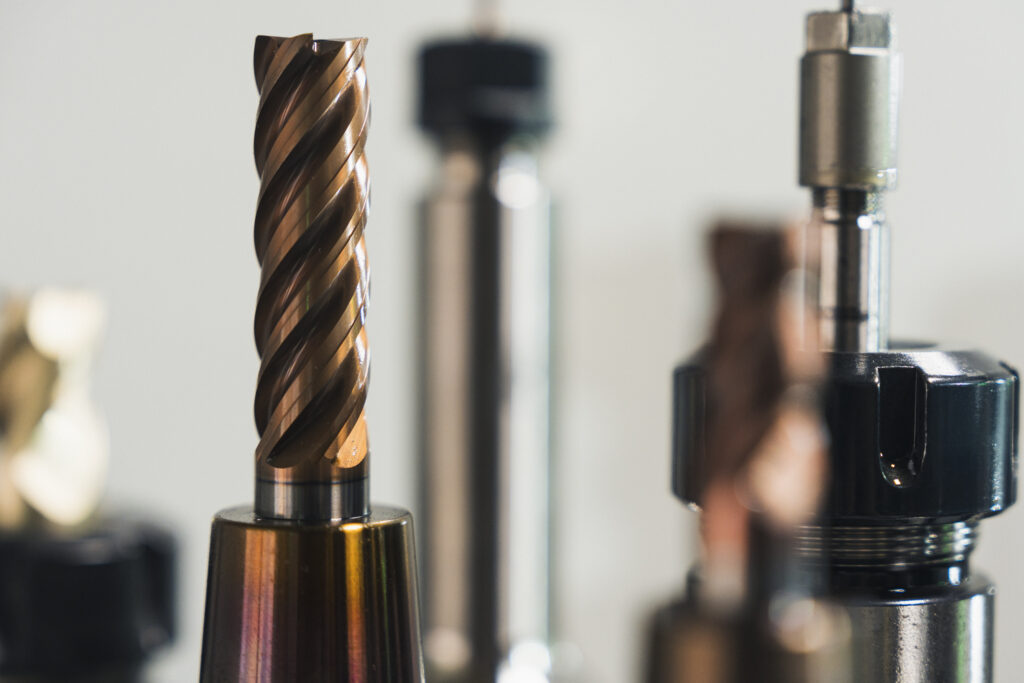
Another training program MSP Manufacturing took advantage of was Purdue University’s IN-MaC (Indiana Manufacturing Competitiveness Center) workforce development programs, which were created as an economic engine to drive innovation and prosperity in Indiana’s manufacturing industry. IN-MaC helped MSP with both training the workforce and integrating new technologies as part of its strategic plan. “These educational partnerships really helped make this project successful and sustainable in the long run,” Johnny said.
“Just adding a new machine or two in the shop wasn’t going to get us to that level … Smart manufacturing would require a mix of next-generation machines and software systems that organize all manufacturing functions in a single place.”
Johnny Goode
President and COO at MSP Manufacturing
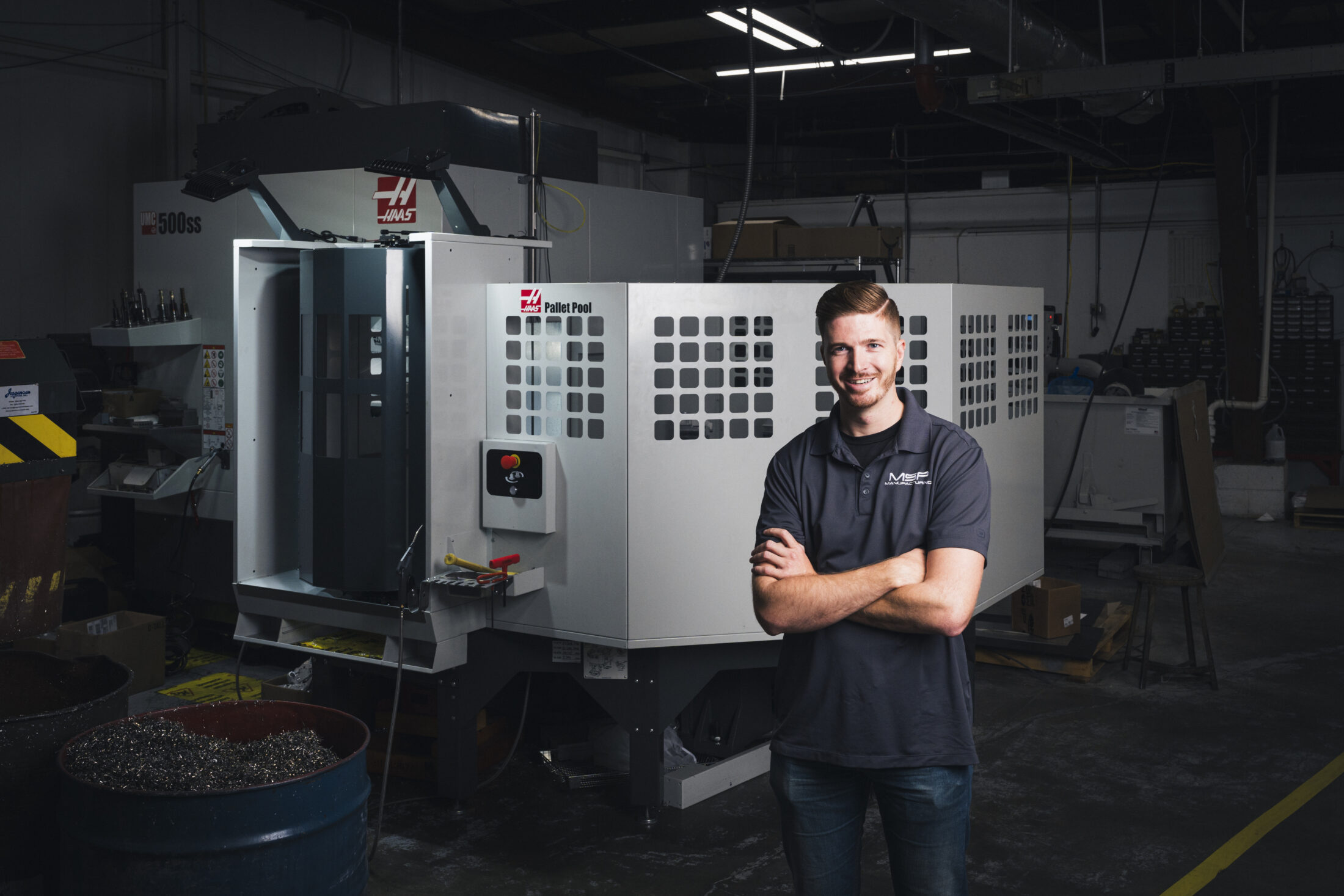