Real-world experiences feed Indiana’s worker pipeline
Butler University
Matthew Caito loves it when a student says, “I didn’t know.” As in, “I didn’t know that’s what the inside of a manufacturing facility was like,” or “I didn’t know that this kind of work was being done around here.”
A lecturer in operations management at Butler University’s Andre B. Lacy School of Business, Caito knows that when students have realizations like that, they have connected with the world of advanced manufacturing and logistics. That means there’s a good chance they will follow that connection to a career. And, in the most ideal situation, that career will be right here in Indiana.
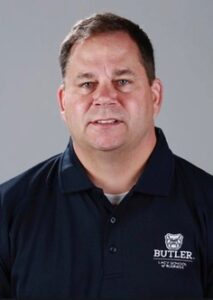
Of course, Butler’s emphasis on experiential learning gets a lot of credit for moments like that. The school brings leaders from area makers and movers into the classroom regularly, sends students to visit nearby manufacturing facilities and distribution centers, and requires every Lacy School of Business student to complete two internships. The fact that one of those internships must be in Indianapolis simply helps to feed the area worker pipeline, notes Lori Coe, Butler’s associate director of Career and Professional Success.
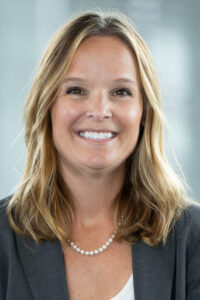
As one might expect, those internships make a big impression on students. By exposing them to local workplaces, the internships not only give students practical experience but also help them enter the working world with realistic expectations of what it’s like to work in advanced manufacturing and logistics, increasing the odds that they’ll find and settle into the right job after school.
Those odds increase even more if students get to truly feel they made meaningful contributions to the company where they’re doing their internships, Caito says. In best-case scenarios, students have reported having internship opportunities to lead initiatives or contribute new ideas, and some have even earned recognition from their employers.
“If you have an intern who gets recognized and makes a difference, I’m telling you that kid looks at the industry differently,” Caito says.
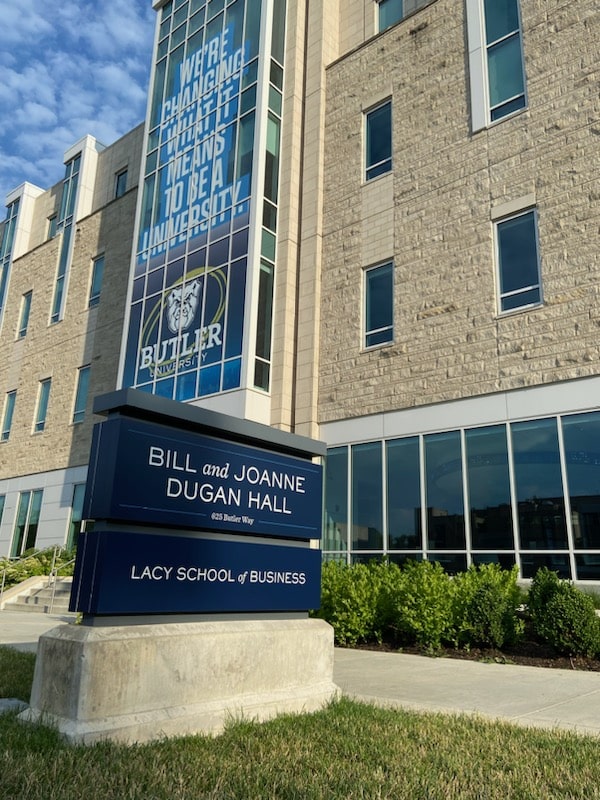
Caito seeks to further prepare students for the realities of the workplace by helping them develop soft skills, coaching them on things such as how to communicate effectively in the workplace, even if they have to discuss difficult topics with people who don’t see eye-to-eye with them. Caito also works to help students learn about workplace expectations, creating classroom models that help them understand operational standards, performance measures, productivity data and more.
Through this combination of tangible experiences, classroom learning and immersions in area manufacturing and supply chain operations, Caito hopes that he can help to develop young professionals who take positions with Indiana firms, contribute quickly through their knowledge and talent, and succeed because they have a clear picture of the careers they want to have.
“When they graduate, I don’t want my students to be surprised by what it takes to succeed,” Caito says. On the contrary: He hopes they know exactly what it takes – that they never again say, “I didn’t know” – and, as a result, are happy to be working with Indiana makers and movers.
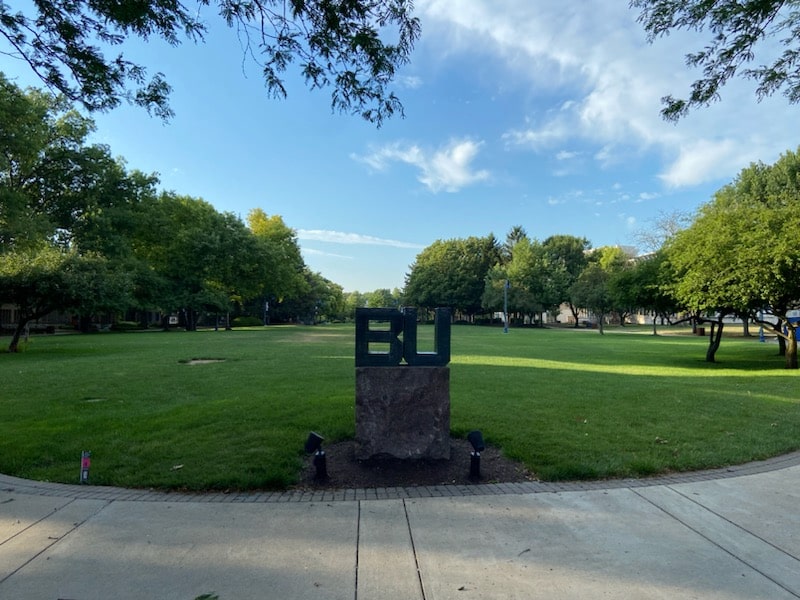