Soil-Max Implements an Innovative Robotic Welding System to Create a Dynamic Manufacturing Process
Soil-Max Inc.
Case Study
Key Stats
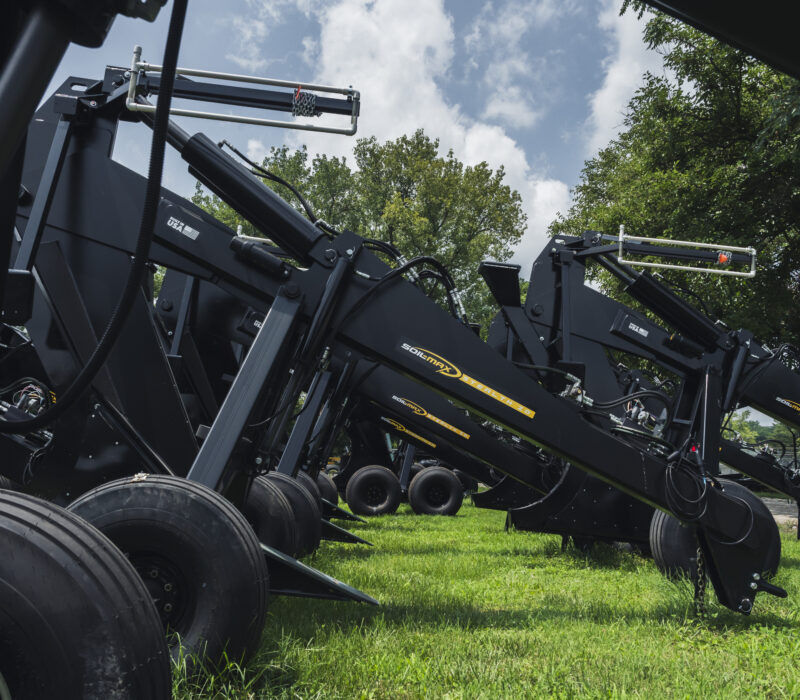
Company History
Soil-Max brings the Gold Digger® tile plow to market in 1997, allowing farmers to tackle their drainage needs.
Indiana farmer and founder of Soil-Max, Denny Bell, recognized that agricultural water management was not just a necessity, but proper field drainage was one of the only solutions that consistently impacted crop yield. While drainage equipment existed on the market, Soil-Max’s Gold Digger® Pro Plow allowed the farmer to accurately install field tile independently. In 2011, Soil-Max redesigned its tile plow and introduced the patented Stealth ZD tile plow, which decreased the power required to pull the tile plow through the soil and eliminated crushing the pipe during grade changes. In 2012, Al Myers, owner of Ag Leader, acquired Soil-Max and Gradient, incorporating Gradient into the Ag Leader Technology® structure. Soil-Max Inc. remained a stand-alone company.
In 2015, Soil-Max introduced the ZD48 tile plow, which allowed farmers with smaller tractors to install tile. Soil-Max’s patented trench closing machine, Shaper Pro, was launched at the Farm Progress Show in 2017. After moving its facility to Terre Haute in 2017, Soil-Max expanded its market with its European plow models. Over the years, Soil-Max’s 18 North American, New Zealand, and Denmark dealer networks have expanded to 60 dealers on five continents. In a rebuilding phase during the COVID-19 pandemic, Soil-Max began growing and seeking additional workers to augment its current employees.
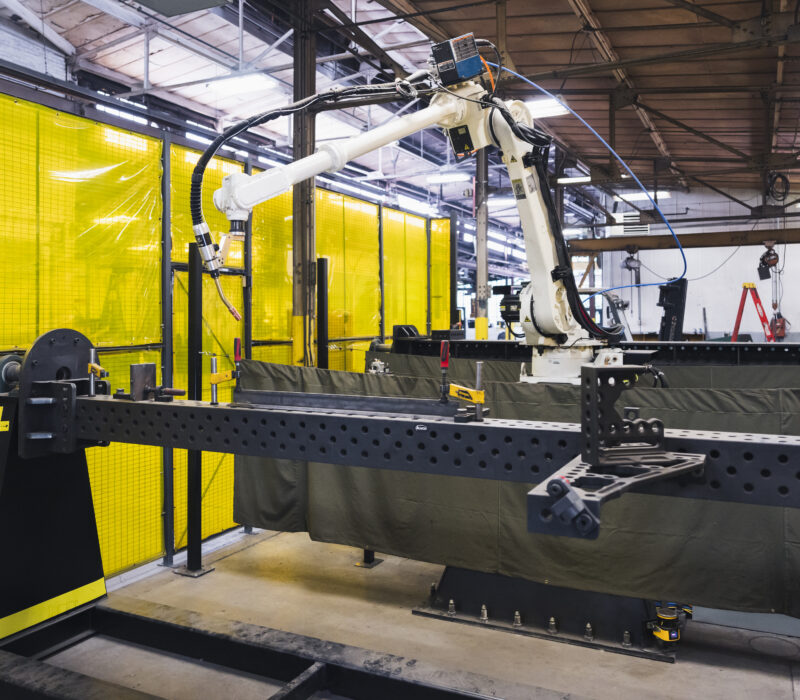
The Project
An innovative robotic welding system handles Soil-Max’s thick steel parts using seam tracking, touch sensing and material moving functions.
Soil-Max’s manufacturing process requires welding steel plates ranging from ⅛ -inch to 1-¼-inch thick. “Everything has been hand-welded in the past, which is a lot of manual work. It takes our welders about 6 hours to complete one sub-assembly or 30-40 hours per completed product. Putting that work through our new robotic welding system reduces employee fatigue and increases manufacturing efficiencies. The integrated touch-sensing and seam tracking allows for consistency and repeatability,” stated Bryan Horsman, engineering manager. The system leverages machine learning (ML) algorithms during the first part of a weld and adapts to the variances found in large plate steel. The system will adjust as necessary, allowing the operator to focus on the overall process and weld quality.
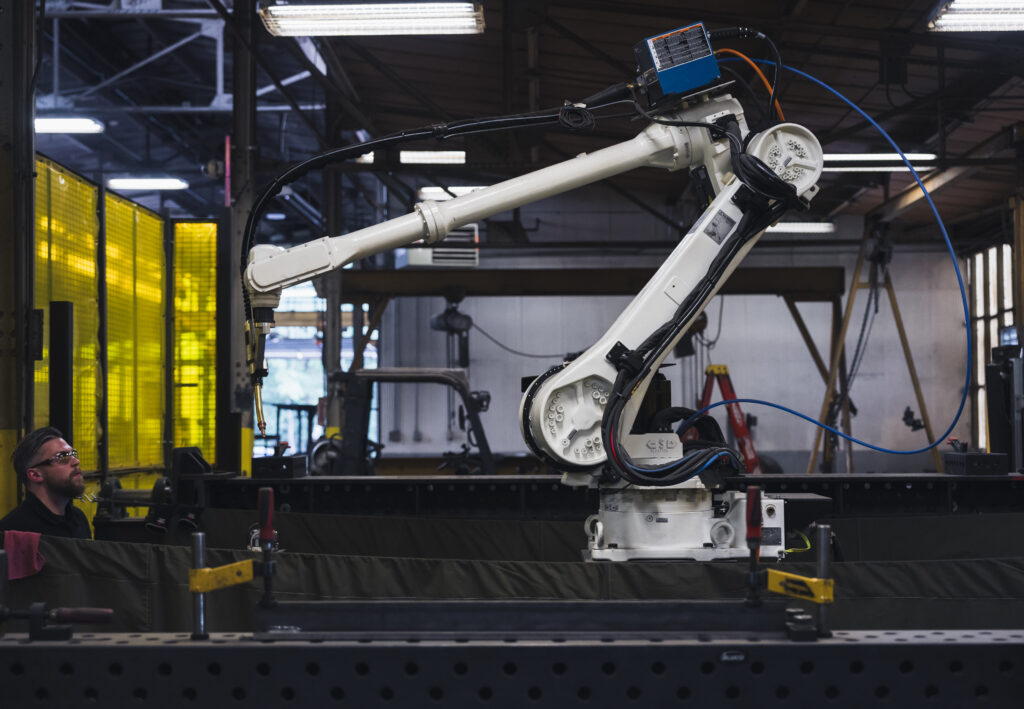
“Understanding how a new smart manufacturing machine works is crucial to getting it up and running,” Bryan said. The Soil-Max robotic welding cell measures 25’ x 30’, making operator training a must. “The vendor can’t just drop it off and say, ‘You guys are good to go; see you later,’” Bryan pointed out. Soil-Max sent two employees to the vendor’s Chicago lab for training that started with robot programming, including touch-sensing, seam tracking technologies and other system capabilities, as well as maintenance. After the equipment was delivered and installed, a vendor trainer was dispatched to the Soil-Max plant to familiarize the operators with the machine and how to get up and running.
“The vendor also has a good support system with a toll-free number where a technician is readily available and will walk one of our operators through problems on the phone,” Bryan explained. Additionally, two vendor reps are located less than an hour from the Soil-Max plant if a problem needs hands-on expertise from the technology provider. “We had a robust approach to identify a vendor, thinking through the workforce training and support in particular,” he said, explaining how the technology provider was selected.
Manufacturing Readiness Grants (MRG) provided by the Indiana Economic Development Corporation and administered by Conexus Indiana are available to Indiana manufacturers willing to make capital investments to integrate smart technologies and processes that improve capacity and productivity. While robotic welding is common in larger manufacturing firms, Soil-Max’s project went beyond the industry standard, designing a system that integrates multiple material moving functions to create a dynamic manufacturing process.
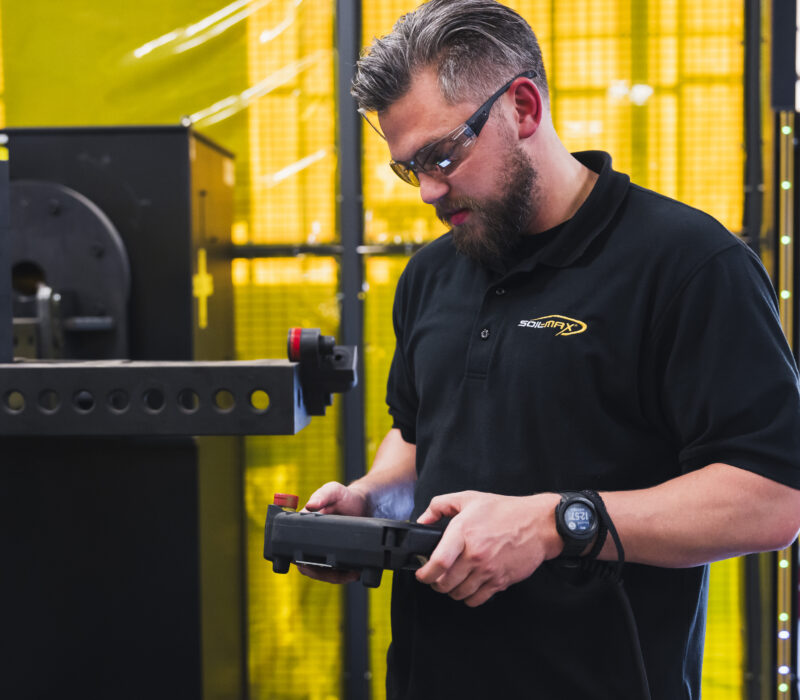
Key Learnings
Implementing smart manufacturing technology affects both upstream and downstream business operations.
Bryan advised that integrating this kind of advanced technology is not a simple task. “One has to consider the entire manufacturing process,” he said. “You’re putting something on the floor that will increase production, and that’s great for that department. But, you might find yourself purchasing more inventory and receiving more products through the door. How does your warehouse and inventory team react? All areas of the company are affected when bringing in new smart equipment,” Bryan explained.
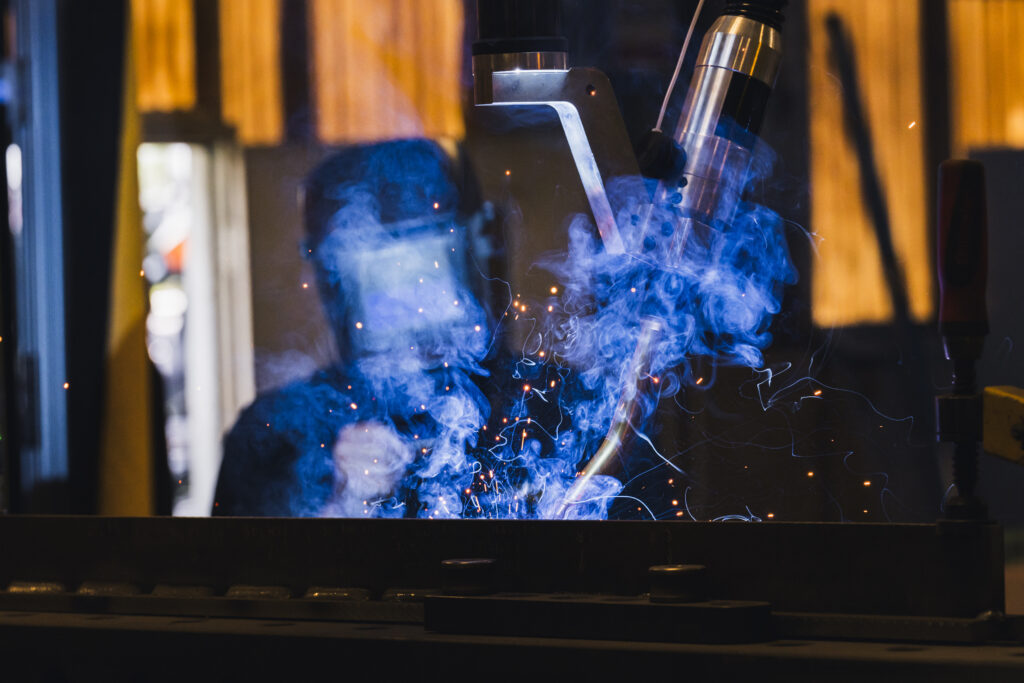
He also recommends having a technology adoption roadmap and keeping it in view. “As far as our next steps, we are looking at other technologies to help reduce lead times and decrease inefficiencies,” Bryan shared. “Technologies that can be brought in-house help with prototyping, which allows us to bring products to market faster while also making us leaner as a company.”
Appoint an internal champion for technology adoption.
Having an employee champion the process is vital. “It’s important to have a champion pushing the project to get done on time and ensuring other departments know how they’ll be impacted and are up to speed. Otherwise, the new equipment can sit in the corner from the day it arrives,” Bryan says. “And if that champion is just one person, and that person leaves the company, you’ll need to appoint and train a new person. Don’t be afraid to share the learning and technology with everybody.”
Bryan is also an advocate for the Manufacturing Readiness Grants (MRG) program. He acknowledged that the cost of new technology is always an issue for smaller companies. Soil-Max had already decided to move forward with technology improvements on a smaller scale. “We had a smaller budget, which meant a smaller machine that would have handled only a few of our products. Maybe 30% or 40% of the products in our building would have fit on the smaller machine,” Bryan recalled. The MRG funds enabled the company to move to the next size of the machine and train the employees to operate it.
“When I was driving home for Christmas break with family, I heard about the Manufacturing Readiness Grants program on the radio. Later that night, I saw a Facebook ad about it and emailed my boss. ‘Hey, we need to look into this,’” Bryan remembers. “I spent part of my Christmas and New Year’s break researching.” The final piece fell into place when he learned how responsive the MRG program was and how quickly the process could be completed – in about 3 months total.
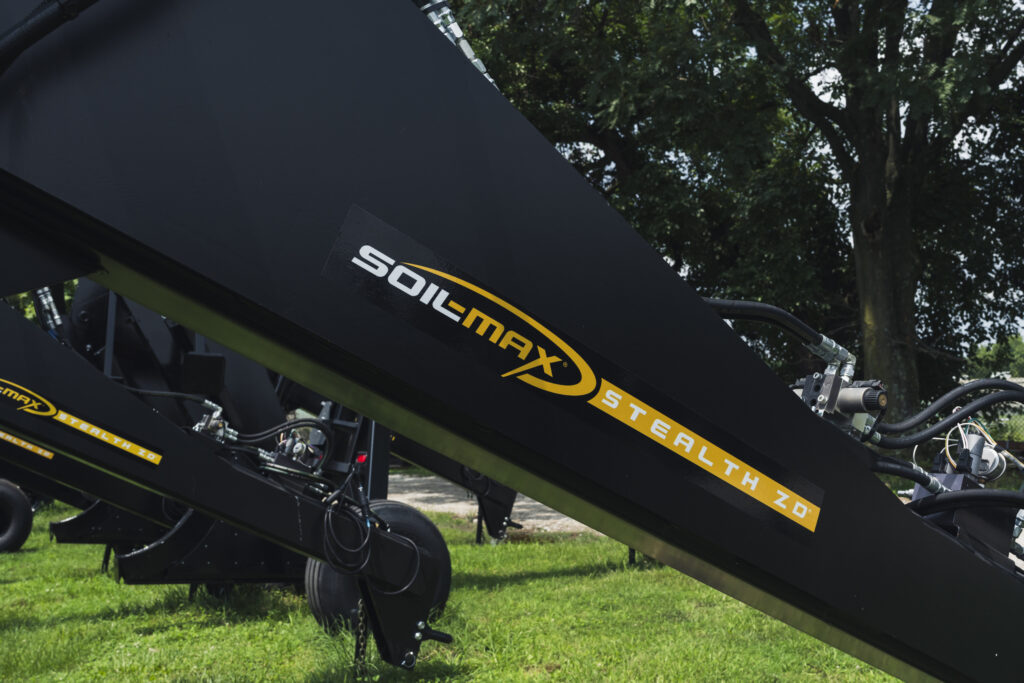
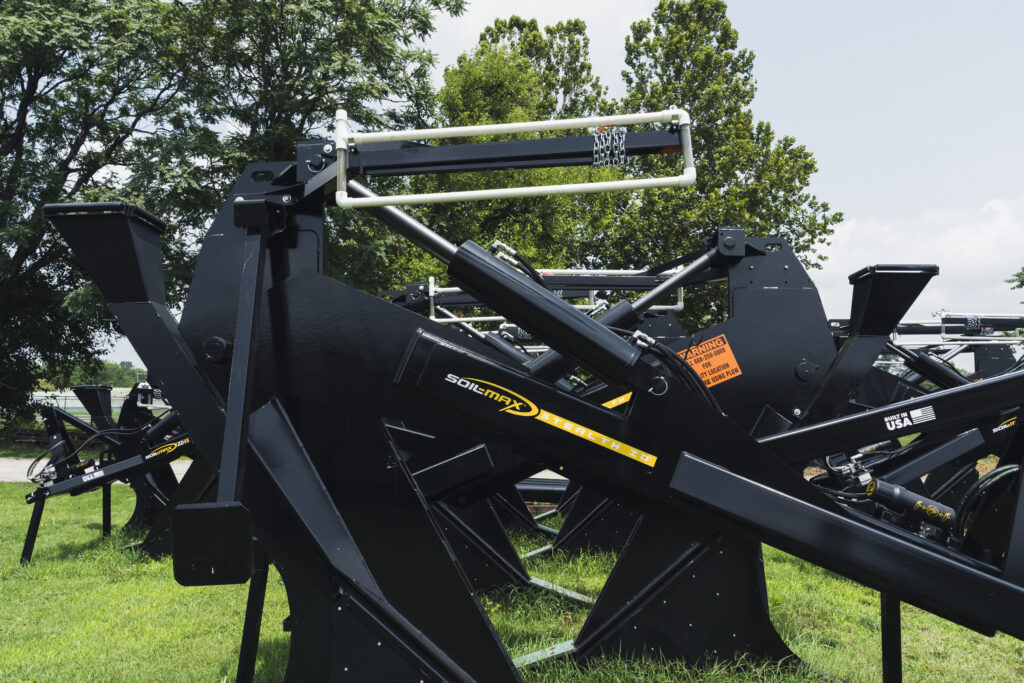
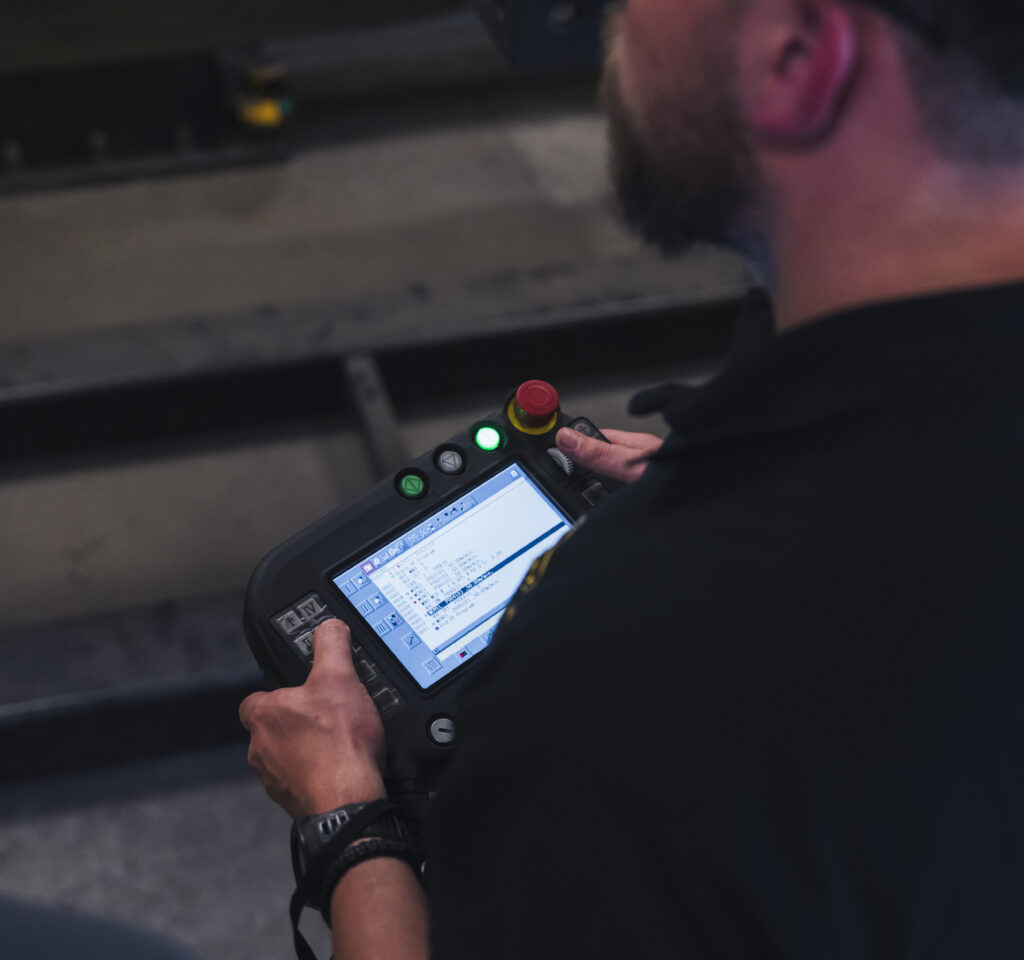
The robotic welding system was deployed to augment the workforce, not eliminate jobs.
When the equipment arrived, employees were still concerned, Bryan acknowledged. As with any new technology, employees weren’t sure what to expect, but positive reinforcement relieved most of that anxiety. “You just keep emphasizing that the robot isn’t here to take a job,” he said. “It’s here to improve our day-to-day.” Soil-Max’s head welder and one of its engineers were sent for training on the new equipment. They learned how to program and operate the features of the equipment. “We rely on his knowledge, and he works closely with the engineering team,” stated Bryan about Soil-Max’s head welder.
Employee downtime can cause significant delays in manufacturing. “Before the new robot welder, even with five full-time welders, one individual taking time off was a 20% loss in production for the day. When production numbers drop off like that, you understand the importance of smart manufacturing machines. Being able to train anyone in our building to go in and load the robotic welding system, hit the buttons, and press ‘Start’ eliminates some of that downtime,” Bryan explained. Increasing manufacturing capacities opens the window for Soil-Max to grow in all departments.
“As far as our next steps, we are looking at other technologies to help reduce lead times and decrease inefficiencies.”
Bryan Horsman
Engineering Manager at Soil-Max Inc.
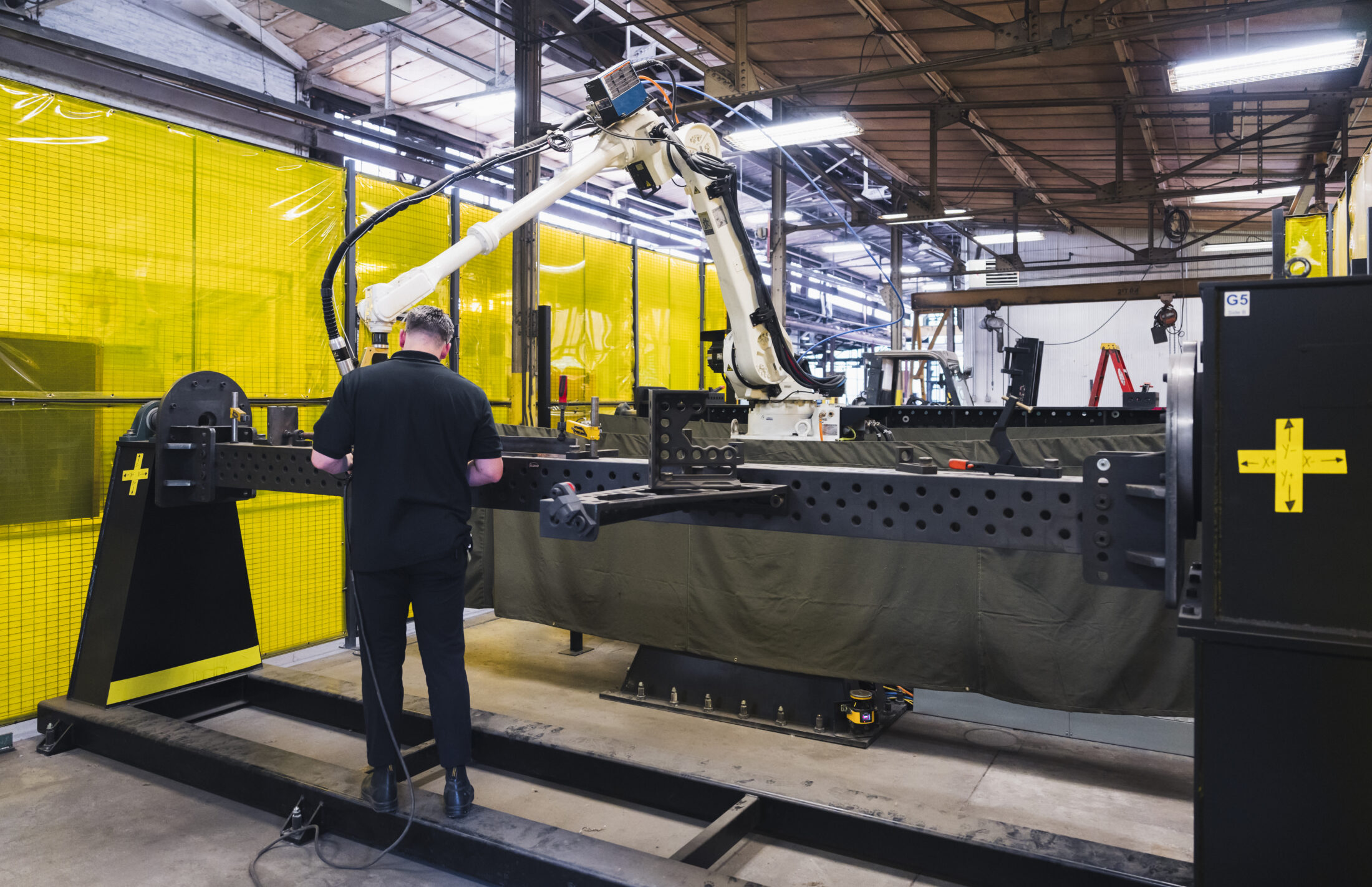