Trifecta Medical LLC Increases its Hoosier Footprint with an Investment in New Automation and Manufacturing Capabilities
Trifecta Medical
Case Study
Key Stats
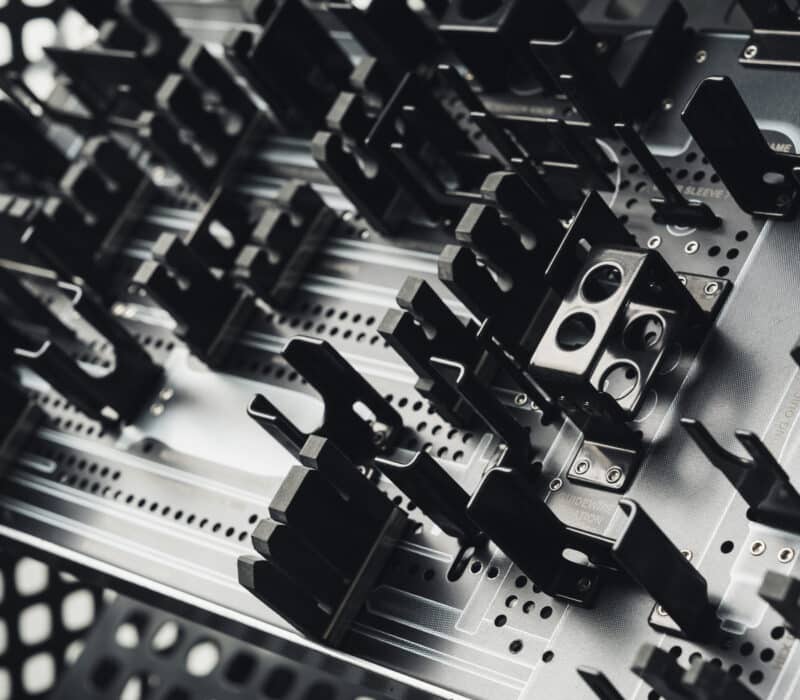
Company History
Trifecta Medical manufactures medical cases, trays and delivery systems for implant procedures happening in operating rooms everywhere around the world.
Trifecta Medical LLC was founded on New Year’s Day 2017, and opened its Centennial, Colorado, manufacturing plant just 3 months later. While the new company was doing well in its initial location, “Indiana is the best place to be,” said Steve Spencer, Vice President of Corporate Development at Trifecta Medical. “It’s one of the best places in the world to manufacture medical devices. There’s something about being a home-grown Hoosier that has an X-factor for medical device manufacturing.” So, 4 years after its founding, the company moved its headquarters to Plainfield, Indiana, in 2021 with the opening of its second facility.
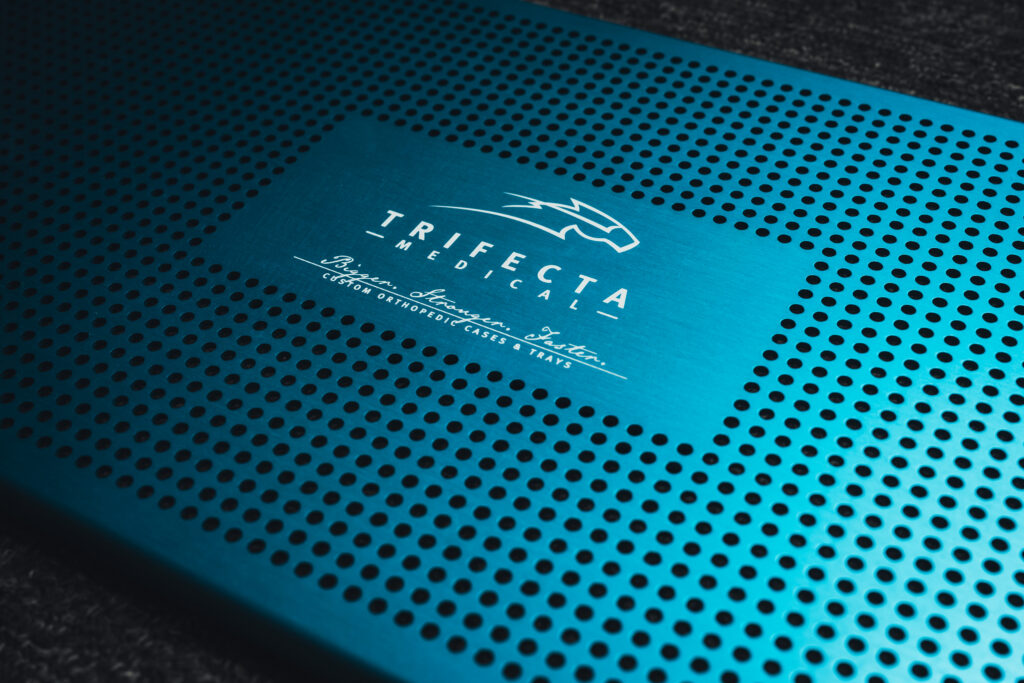
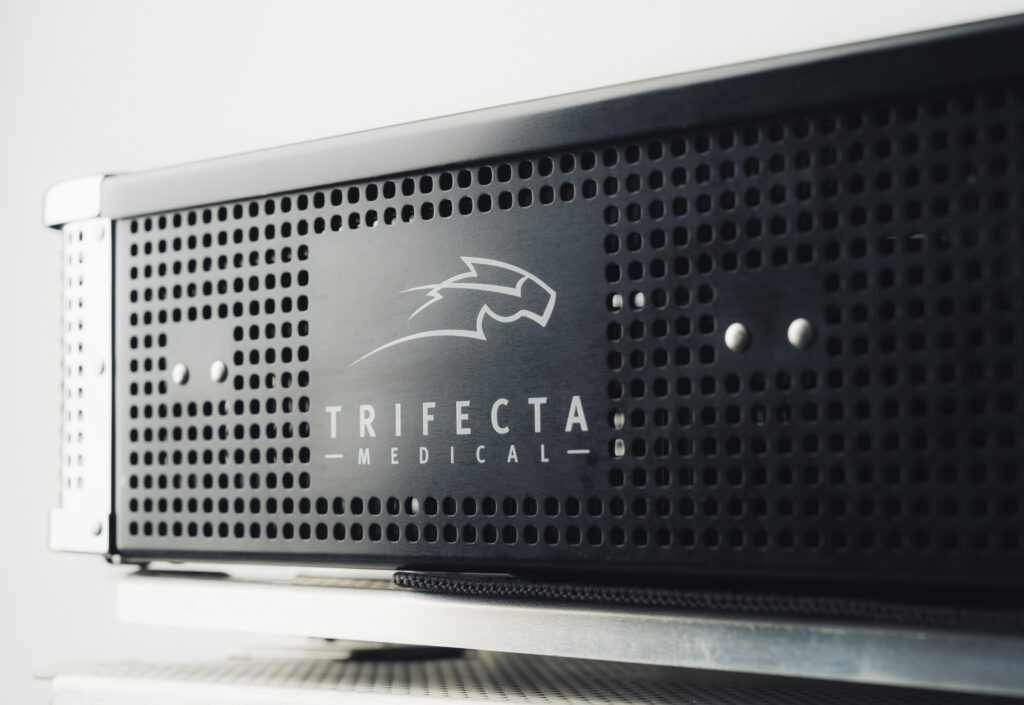
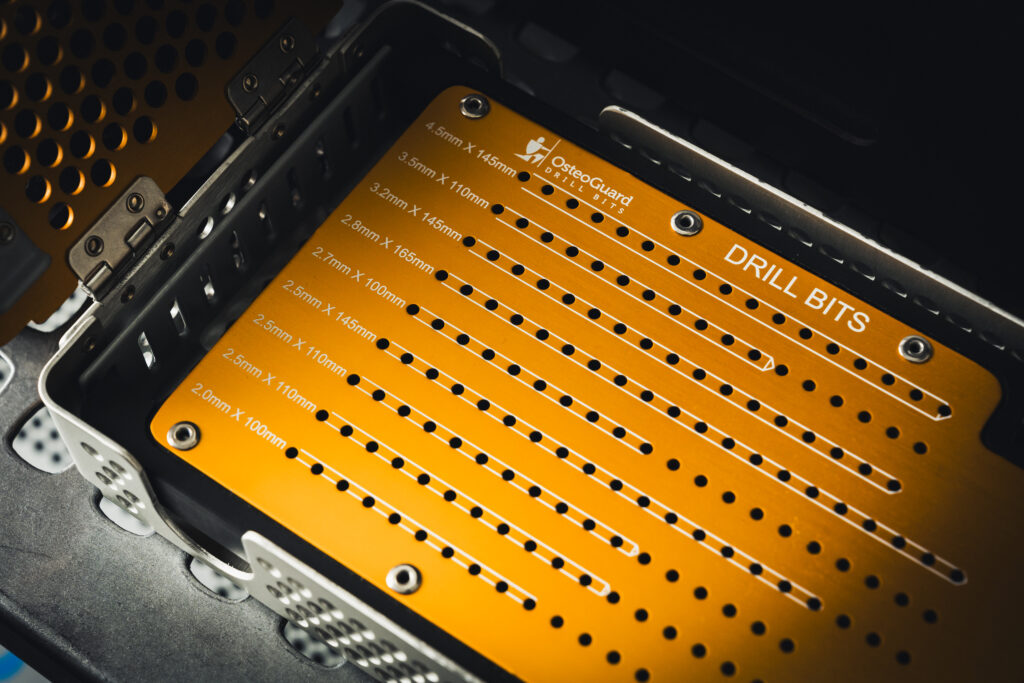
The Trifecta Medical trays are important because a surgeon uses each instrument in a medical tray during a surgical procedure. Each tray (or case) may cost up to several thousand dollars, but the equipment inside costs even more, sometimes in the hundreds of thousands of dollars. The case/tray set houses all the tools and instruments needed before, during and after surgery, so it must be compact and durable. It also needs to withstand sterilization and cleaning, and each component must be easily identified by the surgeon and surgical team.
Trifecta Medical has excelled at manufacturing orthopedic and surgical cases, growing rapidly and achieving double-digit growth yearly since opening its Indiana plant. More than 60 employees work 1st, 2nd and weekend shifts in Plainfield.
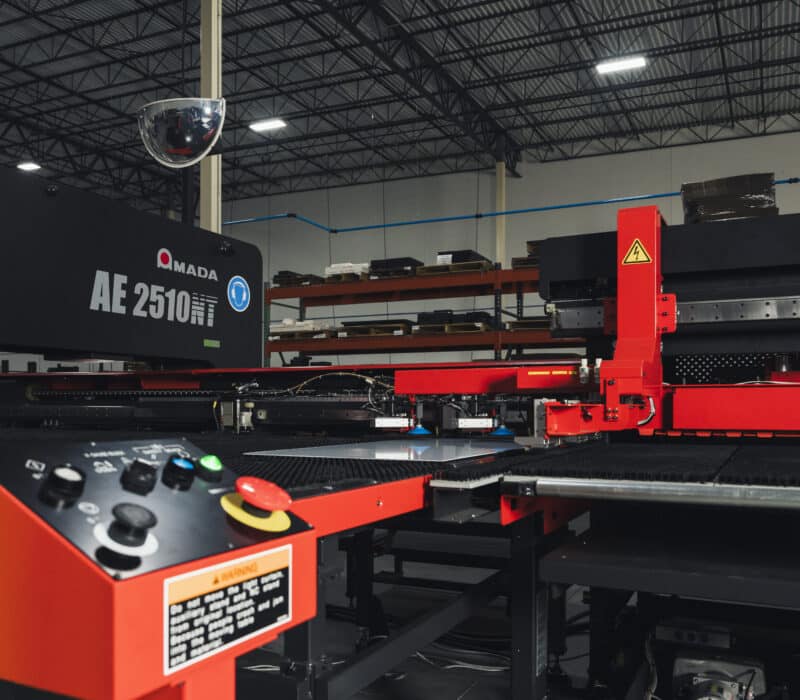
The Project
New tech-enabled equipment would increase Trifecta Medical’s manufacturing efficiency and provide significant energy savings.
Trifecta Medical’s early success was earned despite its reliance on older, less automated equipment. Its original hydraulic presses were undependable, and it was never possible for Trifecta Medical to operate all 4 machines simultaneously. There was also a risk of compromised on-time delivery of its products, so Trifecta Medical was exploring alternatives to finance the purchase of a new AE2510 turret press with an automated loader. The MRG program presented that opportunity and would allow Trifecta Medical to bring new technology into its Plainfield plant with “state-of-the-art” manufacturing capabilities.
The single most important advantage of the new AE2510 is its power plant. Unlike the 4 existing machines at Trifecta Medical, it is extremely energy-efficient, using less electricity to operate and earning an “ECO Product” designation by the Japan Forming Machine Association. Its power plant is not only more environmentally friendly, but operates with just 64 parts, compared with more than 500 in each of the earlier machines. It reduces the need for frequent tool changes between production runs and its 45-station turret offers a greater inventory of standard tooling, so multiple jobs can be run with no tool changeovers. That alone creates significant savings.
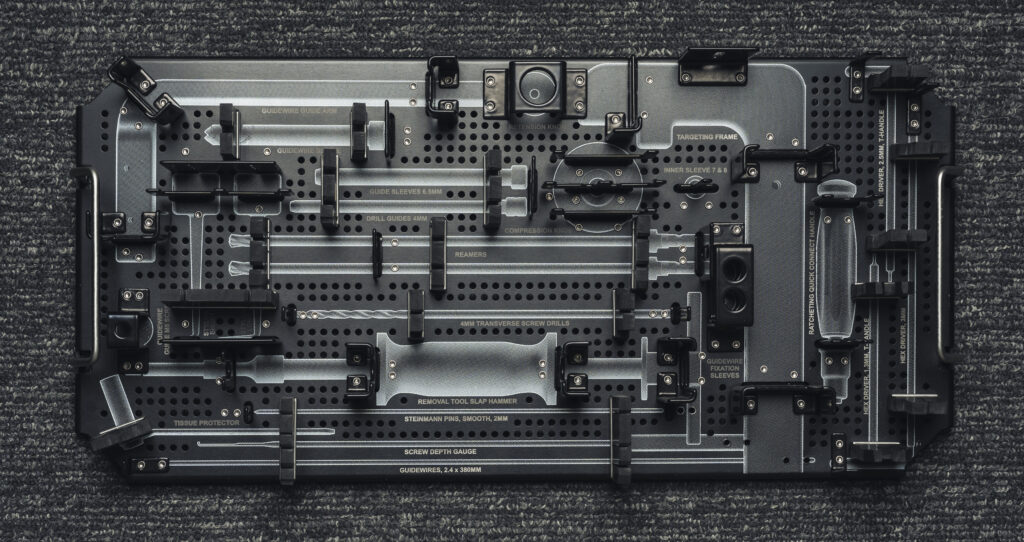
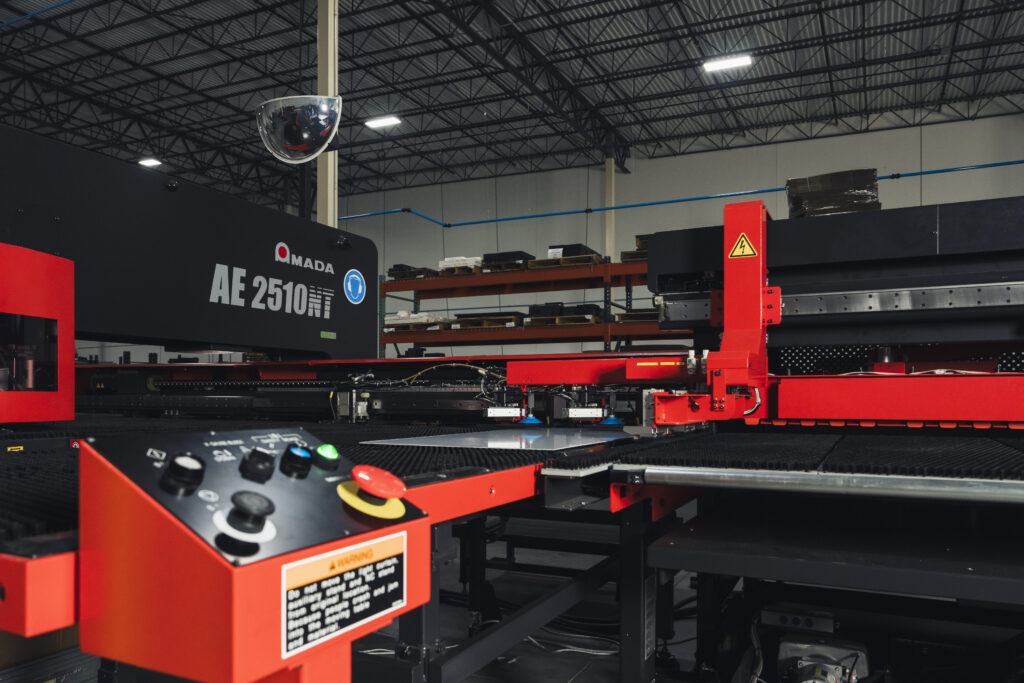
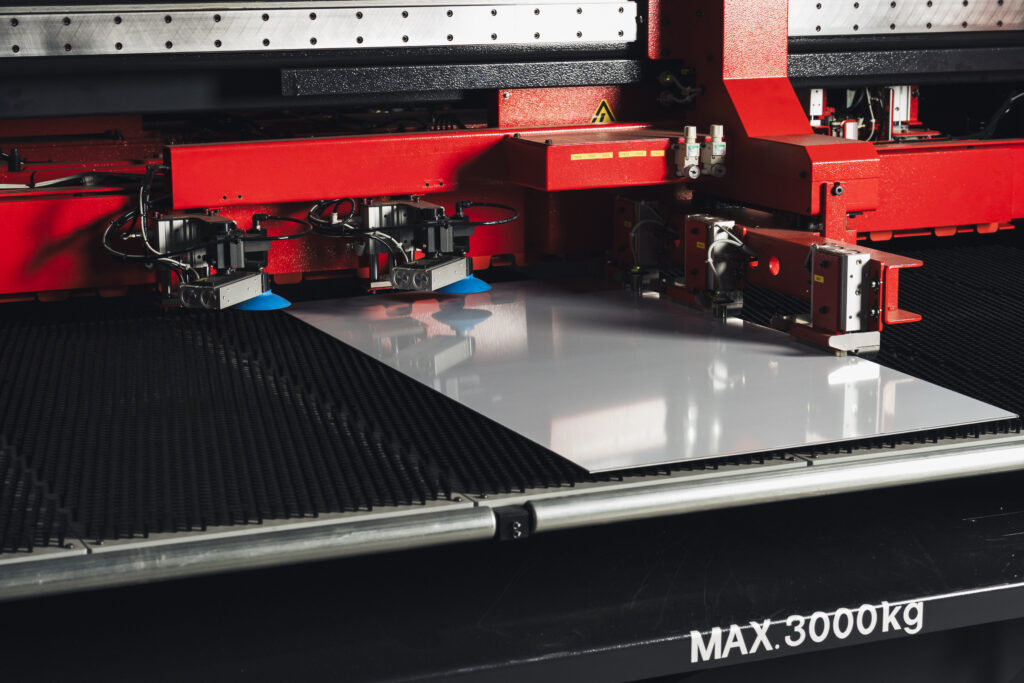
Another major advantage: Its automatic sheet loader reloads without an attending operator, giving Trifecta Medical “lights out manufacturing” capabilities. The plant can now program any number of parts to produce any volume of a customer’s project without a supervising operator. The technology adoption project has expected savings of over $300,000 annually — due to increases in manufacturing efficiency and capacity, as well as energy savings.
Manufacturing Readiness Grants (MRG) provided by the Indiana Economic Development Corporation and administered by Conexus Indiana are available to Indiana manufacturers willing to make capital investments to integrate smart technologies and processes that improve capacity and productivity. With a $150,000 MRG award, Trifecta Medical LLC purchased a punch press with an automatic loader, increasing its production capacity, while significantly decreasing production time of its medical cases and trays.
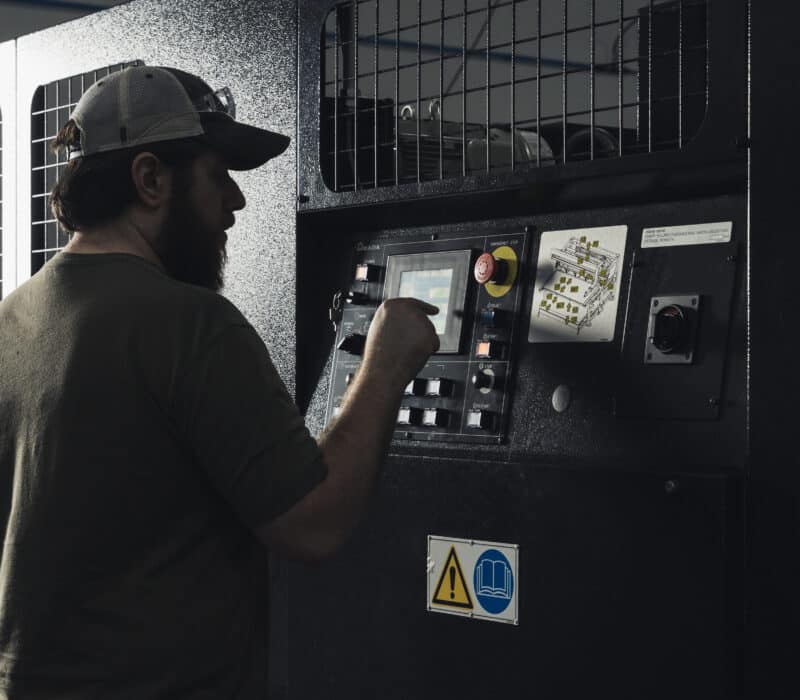
Key Learnings
Take advantage of grant opportunities to grow and expand your business.
“If you have confidence in your products and industry, take advantage of available opportunities and grants to expand your footprint in Indiana,” Steve advises. He acknowledged the potential challenges facing companies: Being the first user of an innovative technology, for instance, can be a gamble. “It is less of a gamble,” he said, “if your leadership is aligned and you do some due diligence.” In its case, Trifecta Medical leaned on personnel at Amada, manufacturer of the automated press equipment, as well as learned with industry colleagues. “Consulting with friends in the industry, I was able to hear about their experience with the new high-tech machine and its performance profile. It did inform our purchasing decision,” he said.
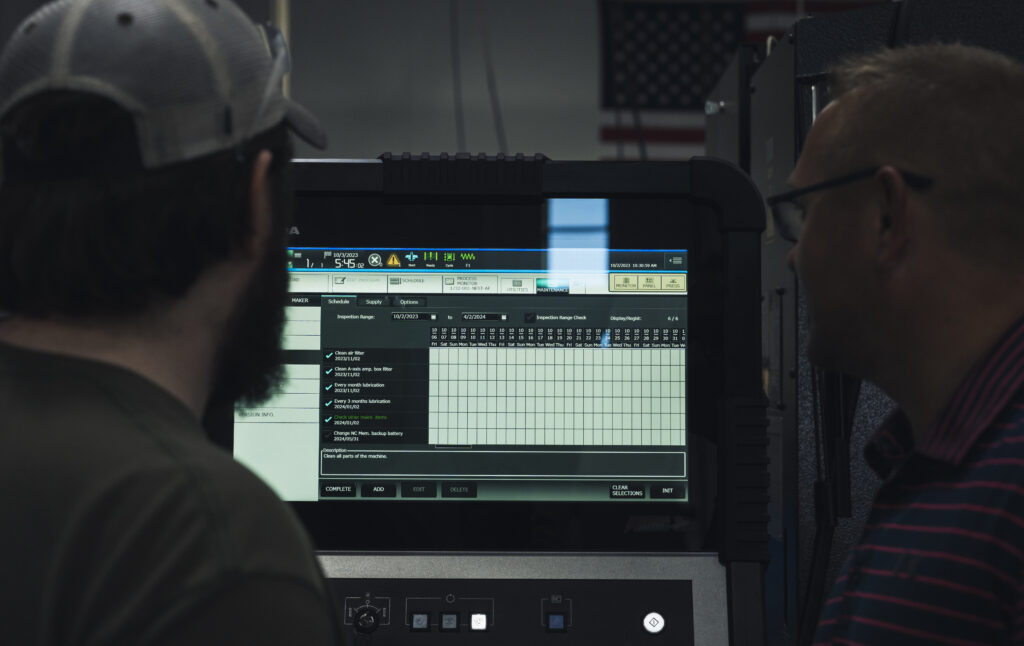
Trifecta Medical leadership was another strong factor in the decision. “The company is led by industry professionals with more than 100 years of combined experience in orthopedic cases and trays and we have an unwavering commitment to quality, responsiveness and reliability,” Steve said. “We knew we could continue to meet those values with technology adoption. In the final cost-benefit analysis, moving forward was the logical course.”
The availability of the Manufacturing Readiness Grants was the icing on the cake. “The grant process was very straightforward,” Steve said. “To make all the planned purchases, we needed some assistance along the way. Technology adoption can be expensive and time-consuming.”
Smart technology has allowed Trifecta Medical’s workforce to develop new skills and learn new processes.
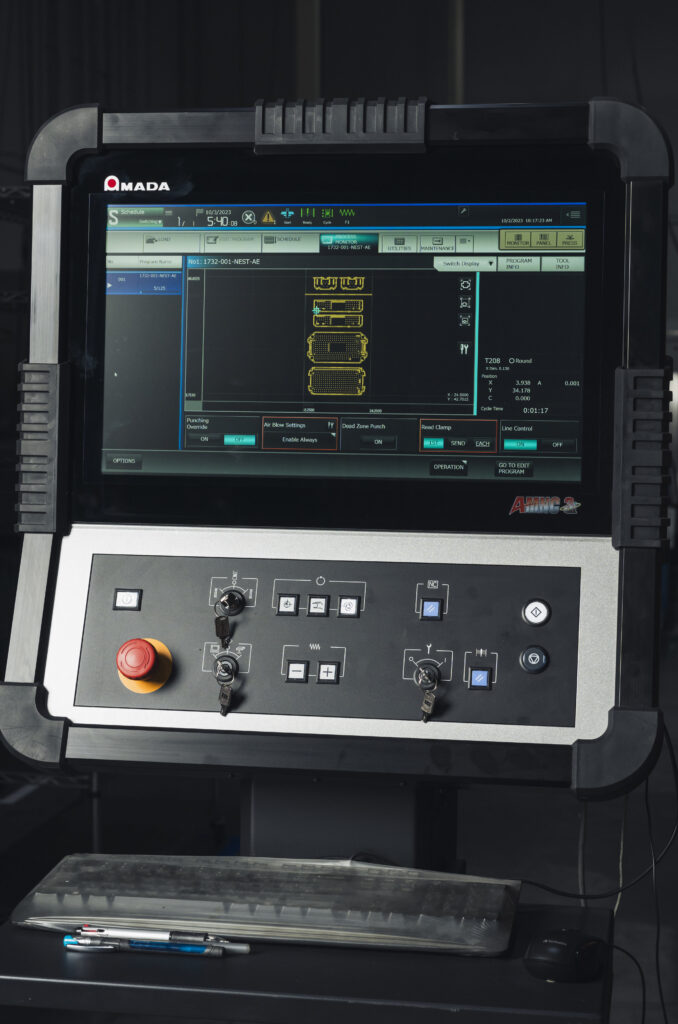
The Trifecta Medical plant has become a training ground for new and existing employees, providing the opportunity to learn and develop new skills used in the operation of the automated equipment that can be carried forward. “It validates our commitment to the continued growth of our workforce at the Plainfield facility,” Steve said. “There are new opportunities for cross-training, wage growth and job security for our employees and their families.”
The benefits are far-reaching. “We have already seen a positive impact on our culture as the new equipment performs exactly as we had hoped,” he said. “The added capacity is a benefit for our customers, and with recent sales, we anticipate continuing to add new upgrades, software and equipment for future production.”
“Indiana is one of the best places in the world to manufacture medical devices. There’s something about being a home-grown Hoosier that has an X-factor for medical device manufacturing.”
Steve Spencer
Vice President of Corporate Development at Trifecta Medical
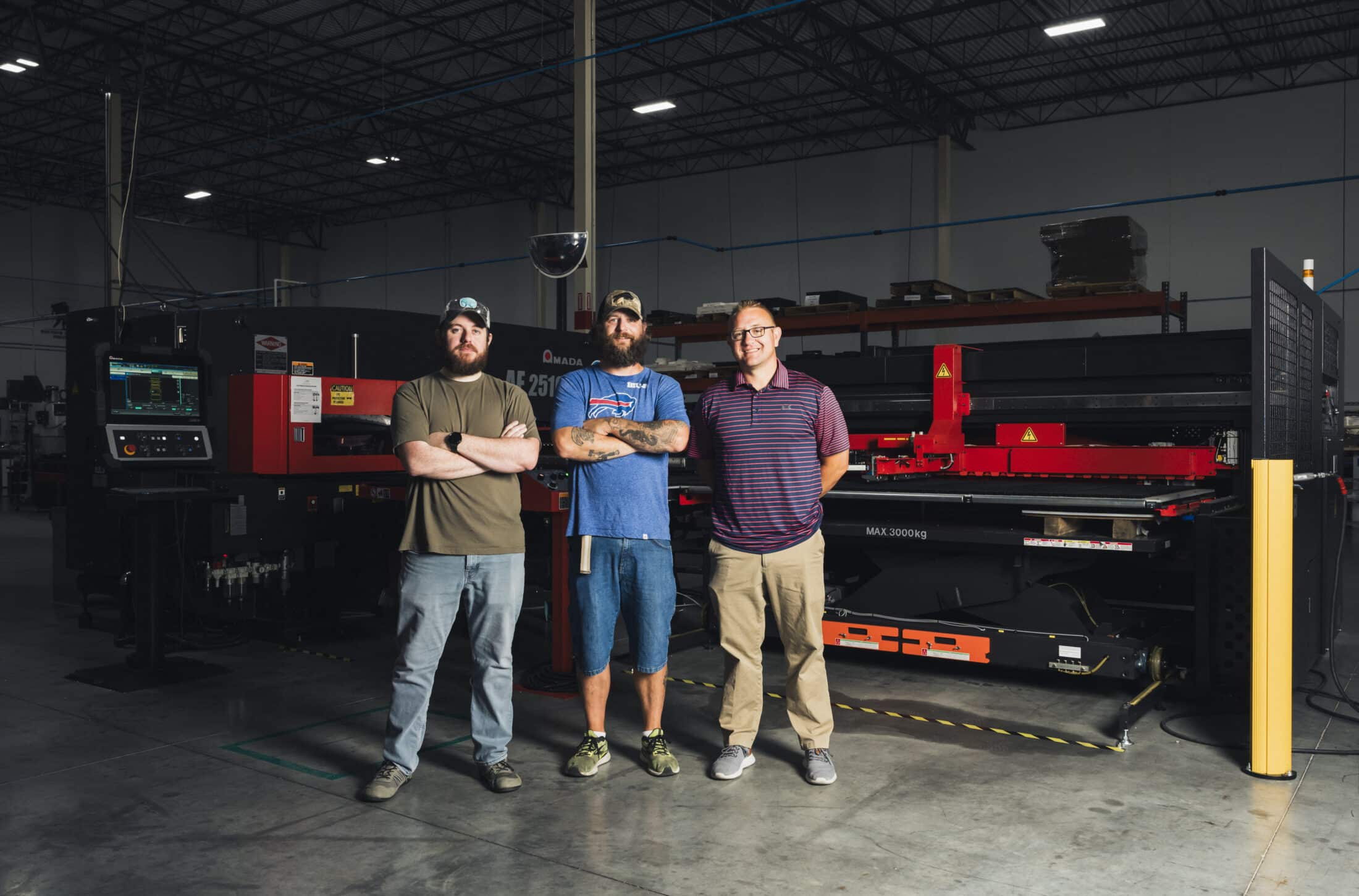