Decatur Plastic Products Implements Robotics to Automate Two Flocking Lines in Its North Vernon Plant
Decatur Plastic Products
Case Study
Key Stats
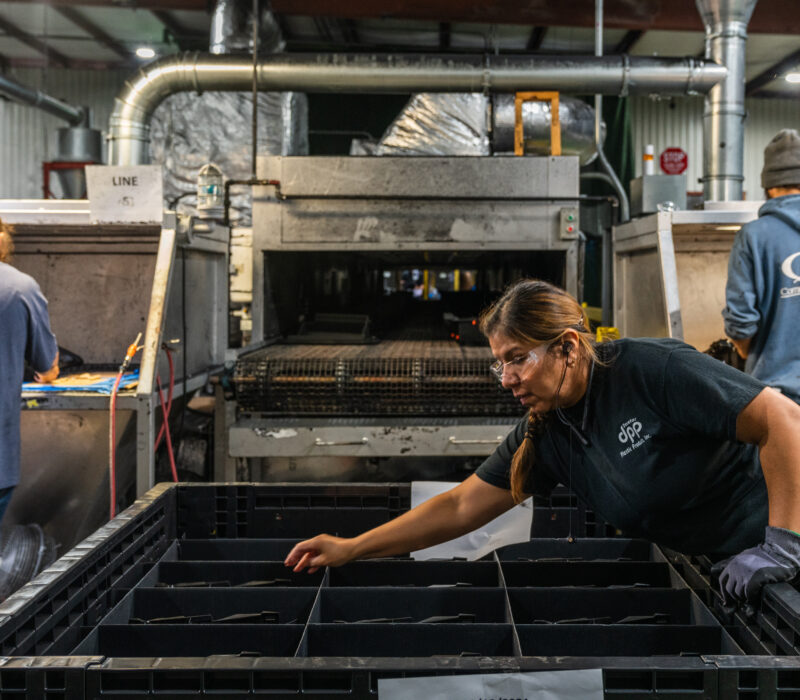
Company History
Owners bring family and community values to a North Vernon plant.
Decatur Plastic Products (Decatur) was established in 1983 as a sample shop for Decatur Mold Tooling & Engineering. In 2016, the business was acquired by the Riley family who remain actively involved in the operation of the business. Gary Riley Sr. serves as Chairman of the Board with President Robert Riley directing day-to-day operations and finance requirements for both Decatur and a sister company, Ningbo Global Sourcing, LLC, based in China. Other active leadership includes Gary Riley Jr, vice president of supply chain; Randy Richey, Indiana director of operations; Robert Shelton, corporate quality director; and Kent Stroud, corporate human resources manager.
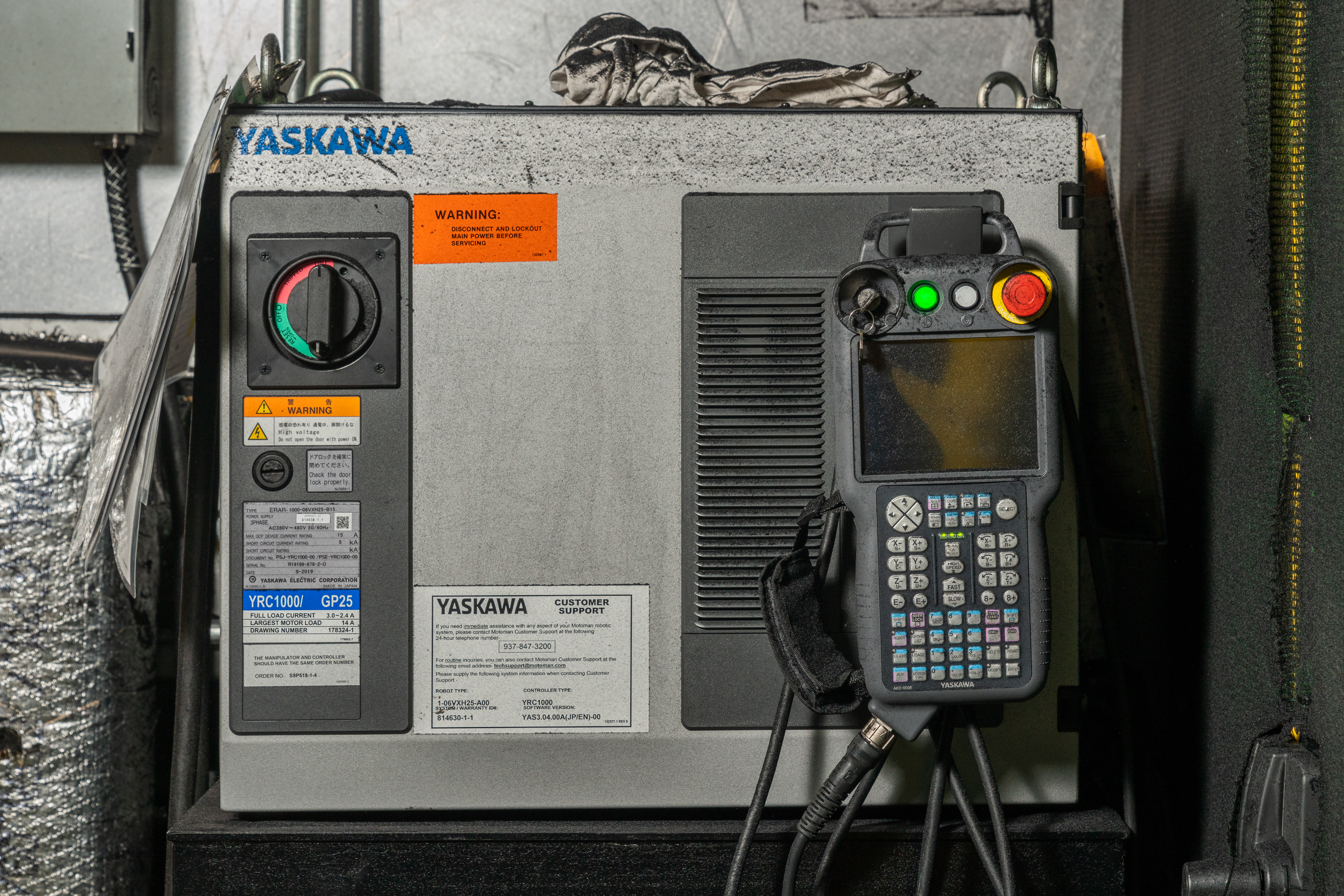
At 15,000 square feet, Decatur’s flocking footprint in North Vernon isn’t as large as some other companies in the area but the owners’ community engagement sets them apart, said Kent Stroud. “The way we work with our employees and the programs we have in place to skill people up is different from other employers around us. What separates us is our ability and willingness to look at a situation and work with the individuals involved,” he said.
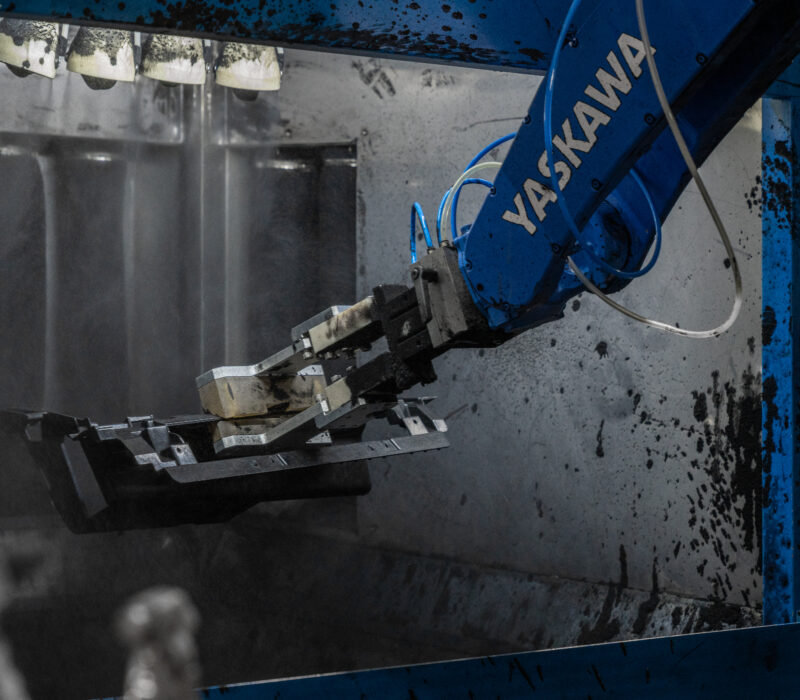
The Project
In the automotive industry—which includes many of Decatur’s customers—flocking is primarily decorative for motor vehicles.
The flocking process applies short fibers to a substrate coated with adhesive. Although the flock strand is very thin and usually just 0.25 to 5 mm, its application may make floor mats appear and function as if carpeted, or similarly impact the interior of glove boxes, drink holders, arm rests and similar parts that directly affect both the function and the aesthetics of the vehicle.
At Decatur, the process entails spraying the flock strands with an electric charge that helps them stand up. To make them even fluffier, the part is then placed in an oven at 150 to 180 degrees for 15 to 17 minutes. Finally, the part is inspected, any residue is blown off, and then it is packed for shipment.
To increase production efficiency, Decatur implements robotics to automate two flocking lines.
Plant Manager Kyle Grandin explained the efficiency aspect of the automated production line. “A robot is there 24 hours per day,” he said. “Of course, you have mechanical issues, but there’s a 100% guarantee the robot will execute its duties. It’s not that we’re trying to eliminate people; in fact, the robots provide labor continuity. The robots perform the tedious manual labor and free up human employees to do the human work. When you begin to become leaner and add automation, you’re able to upskill your workforce and provide a more competitive wage.”
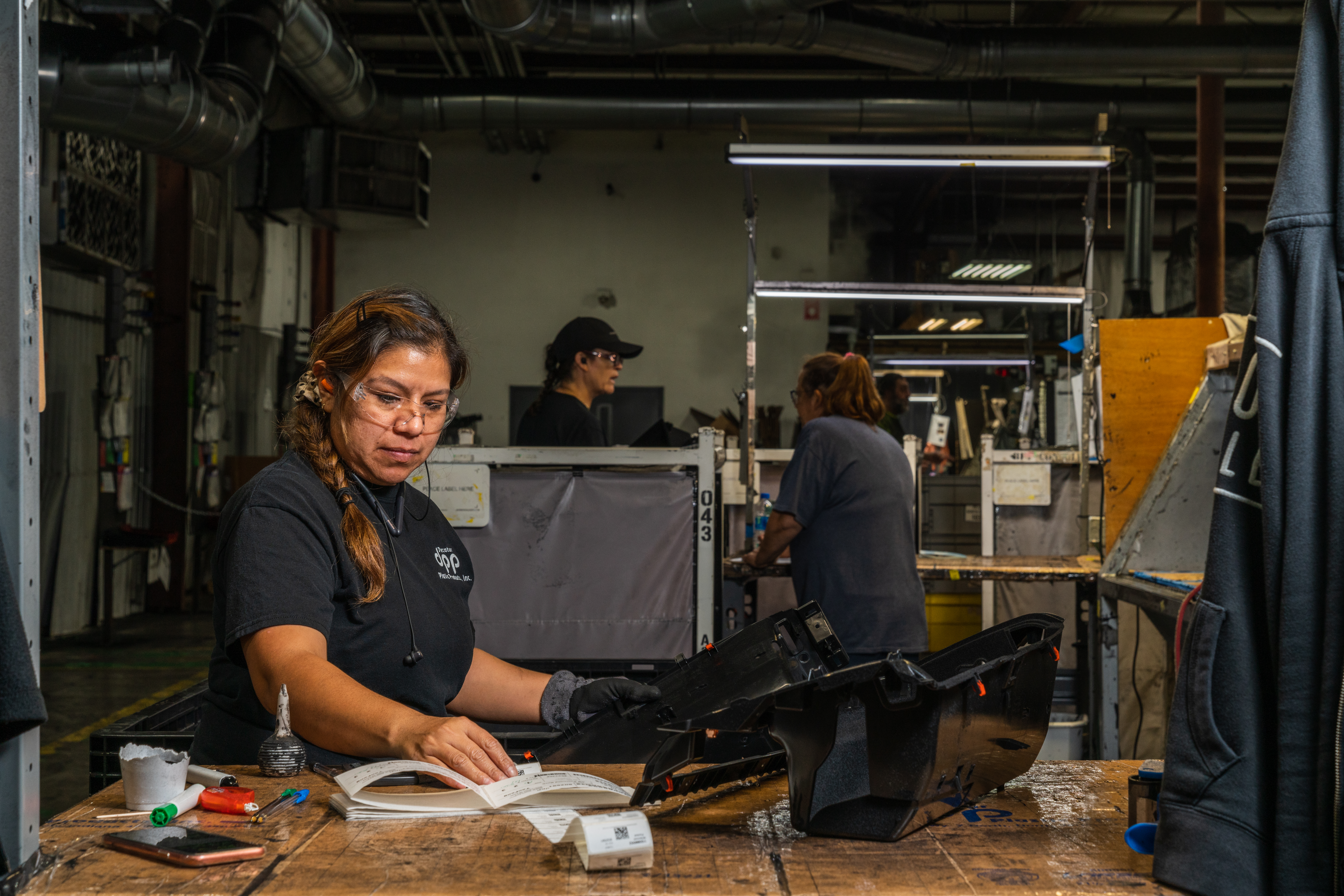
Automation also eliminates fatigue and repetitive motions for human employees. “Our operators can do more—spend more time inspecting, more time labeling things— customers are asking us to do. Our workforce can focus on the changing, evolving parts of the process, instead of the high volume, repetitive and monotonous work. Now we let the robots do those things,” Kyle said.
Manufacturing Readiness Grants (MRG) provided by the Indiana Economic Development Corporation and administered by Conexus Indiana are available to Indiana manufacturers willing to make capital investments to integrate smart technologies and processes that improve capacity. Decatur Plastic Products applied for and received funding to implement an automated flocking line, begin in-house manufacturing of essential parts and avoid lengthy lead times.
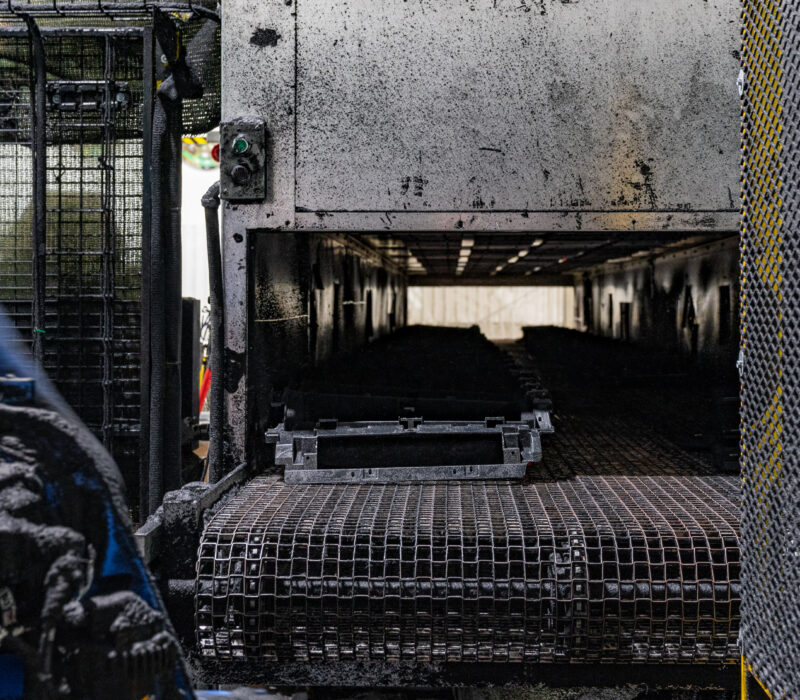
Key Learnings
Leveraging knowledge from an international sister company was an advantage in creating the concept and design for the automation project.
Turning to Decatur’s sister company in China, Ningbo Global Sourcing LLC, was an advantage. Ningbo also started with a manual flocking line process but built a new automated concept. The repetitive part of the job was assigned to a robot, with the worker doing more of the inspection work. “The Chinese team developed the ‘pots and pans’ for the automated process,” Kyle said, “and then we brought it over to Indiana and put it all together.”
Still, taking a turnkey solution from a sister company has its challenges from an implementation standpoint. Kent said, “Honestly when you’re starting out something from the ground up, you think you know what you want. But once you start implementing the solution, not everything works exactly as you thought you needed. Right now, we’re still sorting through and adapting the process.” But, he added, “From a planning perspective, there’s confidence in knowing what you’re going to produce and it gets you thinking about taking on some new orders because you just know you’ll he able to produce it on schedule. The output is more predictable.”
Providing Training Opportunities to Your Workforce Really Pays off for an Automation Project.
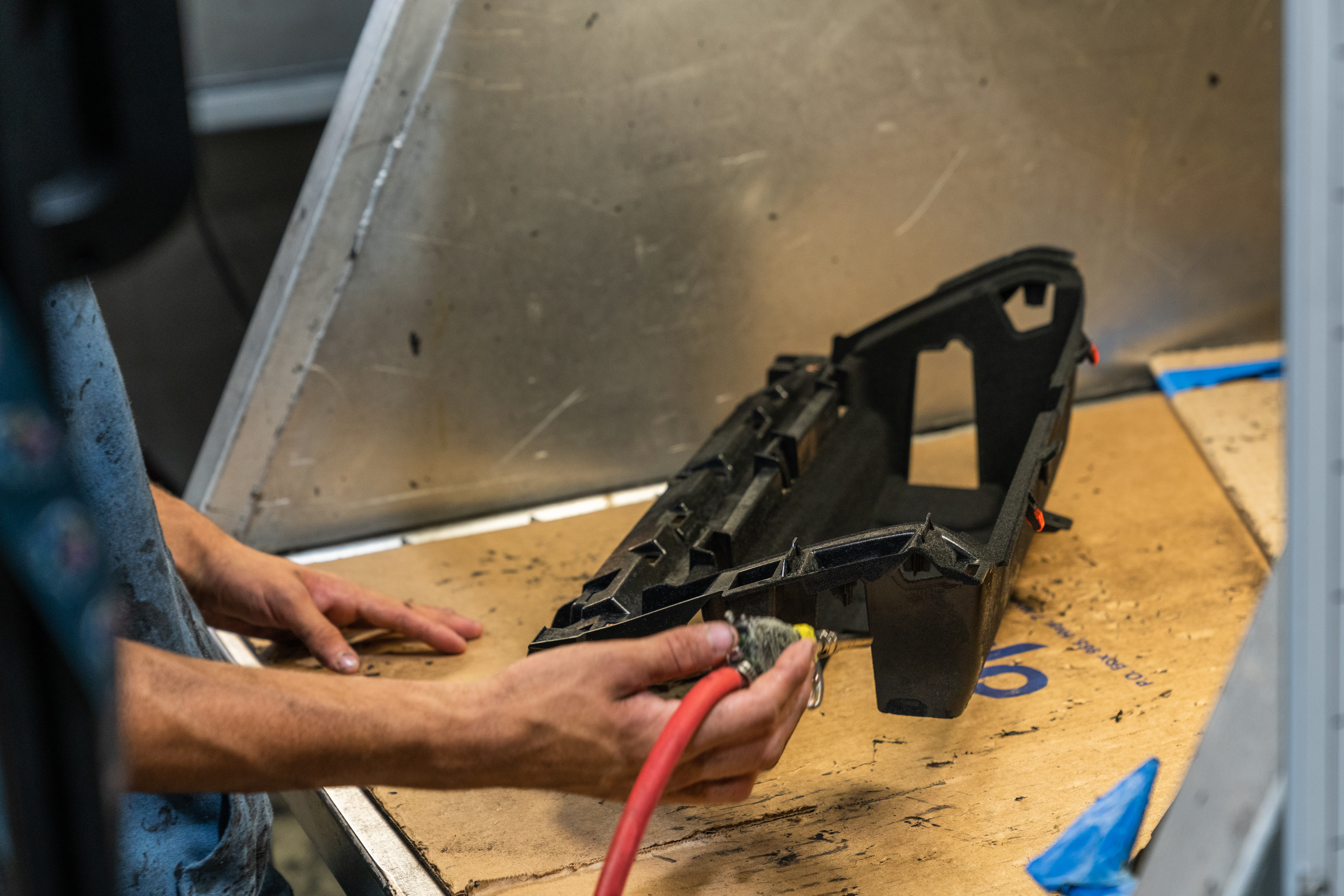
Some Decatur employees have received additional training, and that usually answers their concerns about how the automation works. “It’s a big learning curve,” Kyle said. “It’s scary at first. But our company and our workforce adapt quickly.” He would also advise other business leaders to research the project from all angles before jumping into new automation. “Look into what it actually takes as far as integrating and programming.” He added: “And make sure you do the training. It really pays off, and there’s never enough training.”
“I anticipate expansion over time, but there will always be challenges. Our customers are still struggling to get cars out, so we’re still faced with some of those big supply chain challenges. “Now that we have a couple of robots, we know that we’re going to add more automation, not less,” said Kent.
“Now that we have a couple of robots, we know that we’re going to add more automation, not less.”
Kent Stroud
Corporate Human Resources Director at Decatur Plastic Products
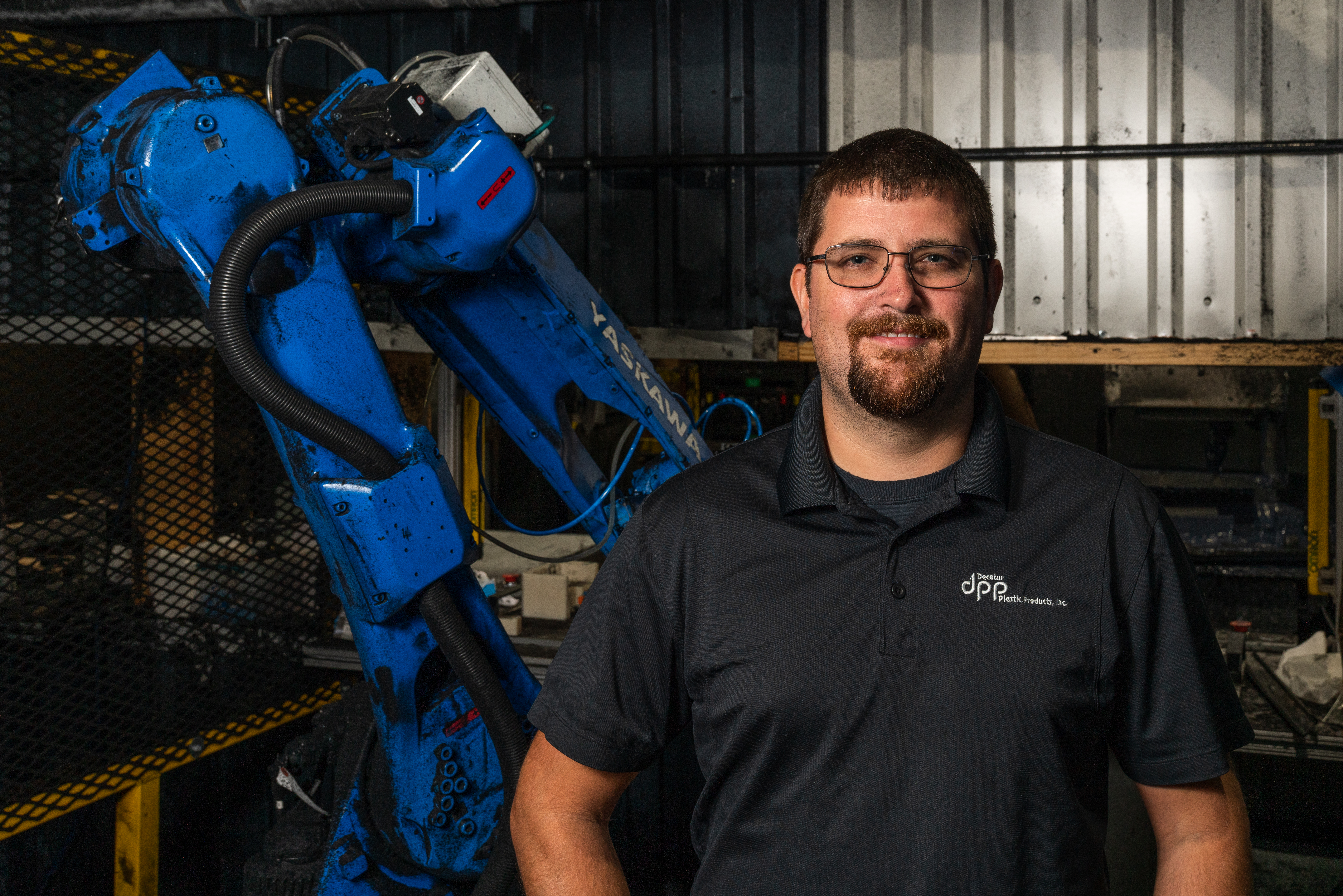