Liberty Trailers Invests in an Innovative Robotic Welding System for Automated Production of Multiple Trailer Models
Liberty Trailers
Case Study
Key Stats
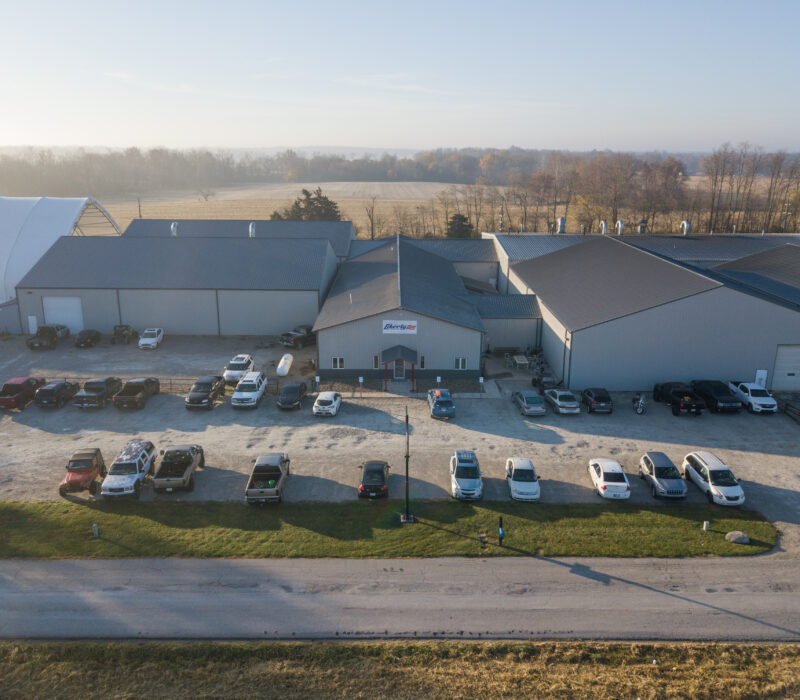
Company History
From founder Kurt Clearwaters to new owner, president and CEO Mike Teso, family-owned and operated Liberty Trailers has grown to become an internationally recognized name.
Fillmore, Indiana, is a small west-central Indiana town, north of U.S. 40 and I-70, just a few miles east of Greencastle. With fewer than 600 residents, the town is home to an international manufacturer of commercial-grade trailers with 80 dealers across the U.S. and Canada. Liberty Trailers was founded in 1998 by Kurt Clearwaters and remains privately-owned and operated today. The firm specializes in dump trailers, equipment haulers, car haulers, flatbed, tilt, pipe, and utility trailers, with its ongoing mission “to build commercial-grade trailers at competitive prices.”
Despite it being 23 years into its operations, Liberty Trailers is anything but old-fashioned. Well-known and respected by businesses and individuals for superior quality, customer service and value pricing, the company has enjoyed rapid expansion and growth to meet the increasing demand for trailers including dump trailers, equipment haulers, flatbeds and more. Its innovative attitude, including early adoption of industrial robotics, has supported an 8-fold production increase since 2020 when President and CEO Mike Teso purchased the company.
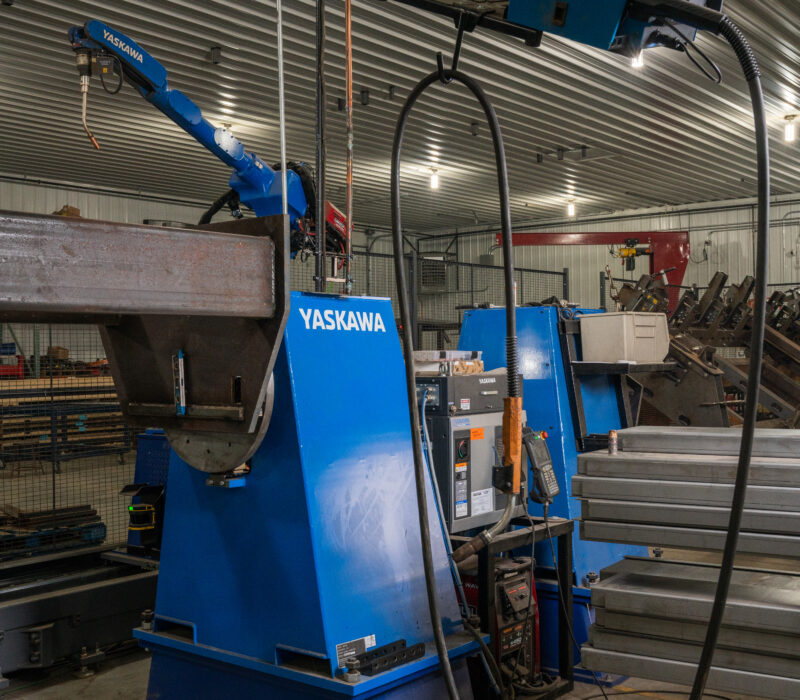
The Project
Liberty Trailers implements an innovative robotic welding system for automated production of its various trailer models.
While the technology adoption project wasn’t Liberty Trailers’ first investment in industrial robotics, it was a unique and innovative use of robotic welding for 20-25-foot-long trailers. Mike acknowledged that the project could have been a “very difficult space to venture into” had it not been for his belief in the team in place at Liberty and the technology integrator the company had partnered with previously (American Welding and Gas). “Let’s do something that’s never been done before in this industry,” Mike said. “Because our engineering team, our management team, the welding department and myself have been through robotics implementations before, I felt much more confident going down this path. In the end, the project was a no-brainer for us.”
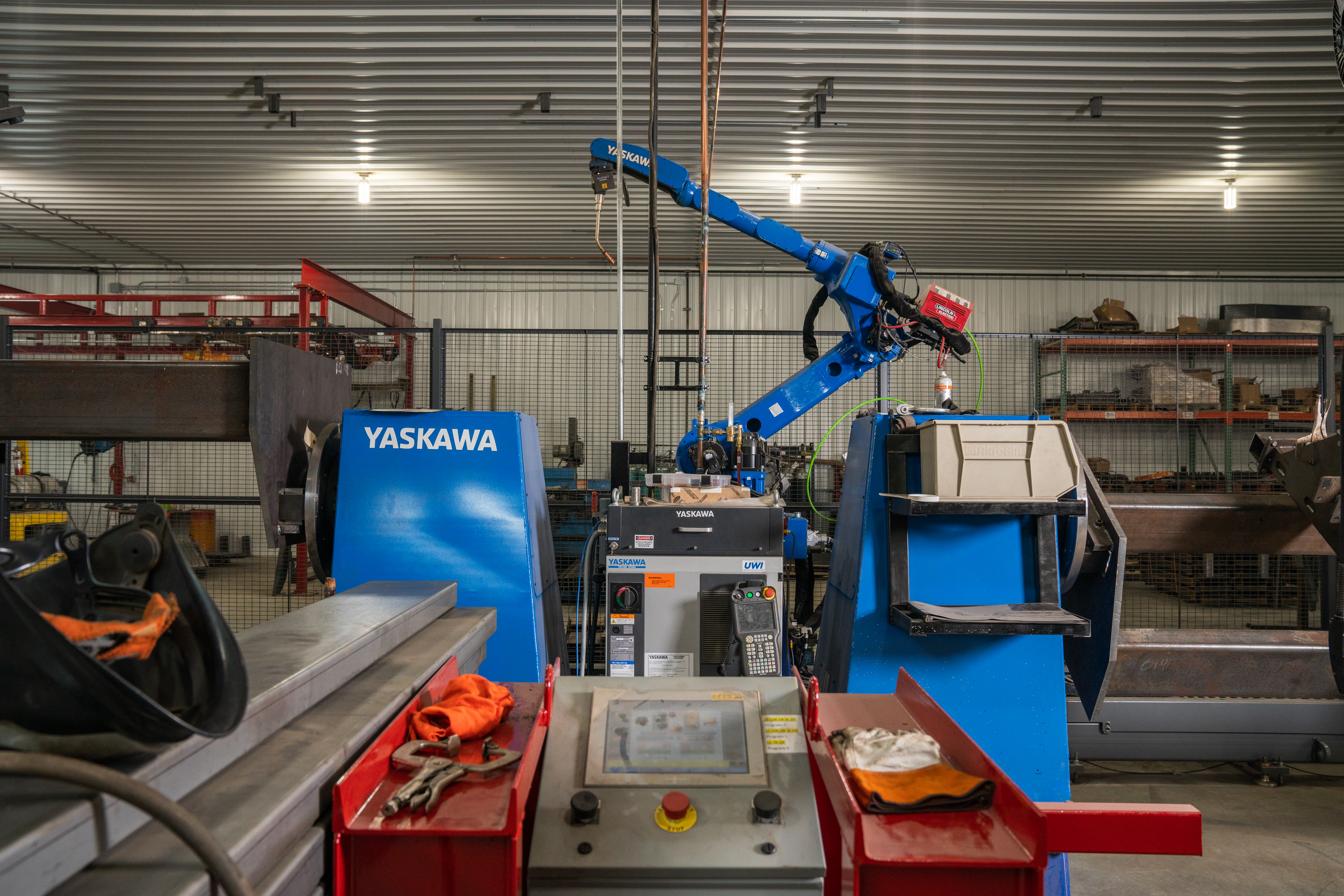
The purpose of the project was to increase efficiency and capacity in the production process of Liberty’s higher volume trailer models. The unique challenge was that the trailers are 20-25 feet long, and there were no off-the-shelf robotic welding systems that could access all the welding points autonomously. To further complicate the project, the welding system would need capabilities to maneuver the trailer and turn and twist it into the right position for the welding robot.
The project was designed to set industrial robotic welders on a movable track system that, much like an assembly line, would autonomously move the robotics up and down the trailer and into the right position. The solution was a 70-foot-long rail with one unit fixtured into place. Yet more impressive is that while the robot is welding one trailer product, another trailer (often a different model) is being automatically loaded into a secondary fixture. “The due diligence and pre-planning were the most important pieces of the technology adoption project,” Mike said. “If you try to take a shortcut in the planning process, it could seriously hinder project execution.”
The completed project resulted in a robotic welding system that can produce multiple Liberty Trailers models from start-to-finish. A video of the cell in operation can be viewed on the Liberty Trailers LinkedIn site here.
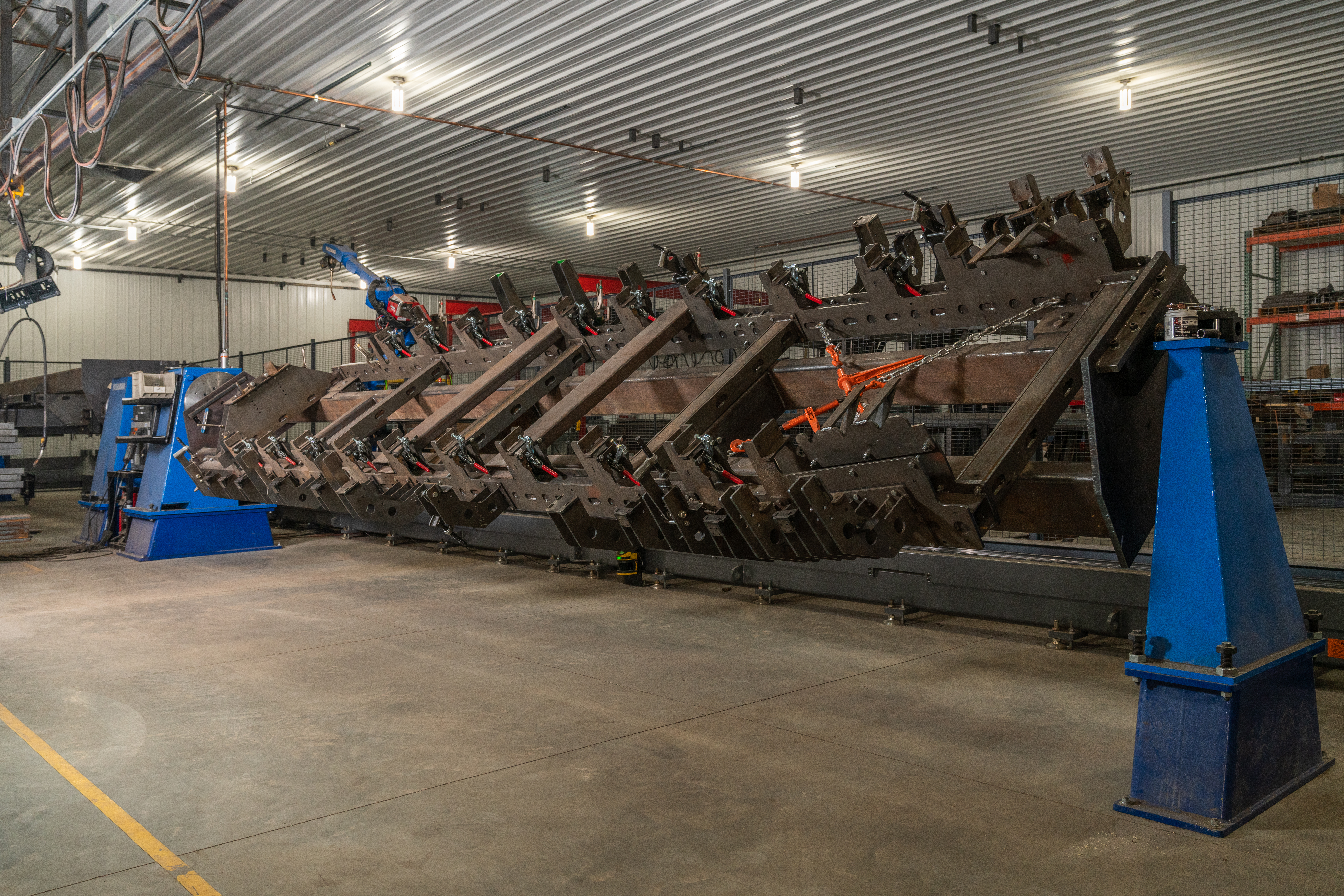
With the project fully integrated into Liberty Trailers’ manufacturing process, the company has increased production efficiency three-fold.
While production efficiency has increased significantly since adding the new robotic welding cell, efficiency has not been the only benefit of the investment. Quality has been similarly improved. In fact, the project has been so noteworthy that Mike said Liberty Trailers is considering adding more robotic welding on subassemblies as well. He credits the many programs available in Indiana to small- and medium-sized businesses. “Indiana does a really good job at supporting all enterprises–large and small,” he said. “We know we need to become more competitive because we’re operating at a global scale. The fact that Indiana supports these technology adoption efforts is very important.” As evidence of the project’s success, Mike pointed to the company’s extraordinary growth in the past two years. “Since undertaking this project and new upgrades made in 2020 and 2021, we now have 8 times more output in trailer production,” he said.
Manufacturing Readiness Grants provided by the Indiana Economic Development Corporation and administered by Conexus Indiana are available to Indiana manufacturers willing to make capital investments to integrate smart technologies and processes that improve capacity and productivity. Liberty Trailers earned a $100,000 Manufacturing Readiness Grants award to implement an innovative robotic welding system that significantly increased internal fabrication capacity and efficiency.
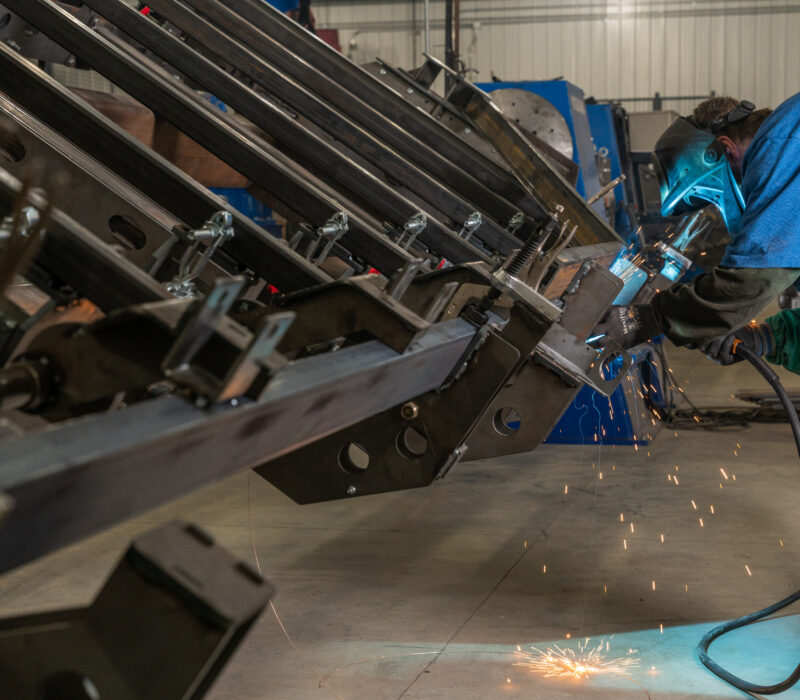
Key Learnings
The planning process is a crucial aspect of every Industry 4.0 project.
“By the time I sent the grant request for the Manufacturing Readiness Grants, we were already pretty far down the line in terms of project planning,” Mike said, emphasizing again the need not to go easy on the planning process for smart manufacturing improvements. As an example, he described the company’s experience with software integration for the robotic welding system. “We [Liberty Trailers] identified the welding points for the industrial robots, and our technology integrator inputs those into the software. But in the real world, there are material tolerances and other fabrication nuances that we had to learn about. If you think the process is going to be X amount of time for programming, budget for double.”
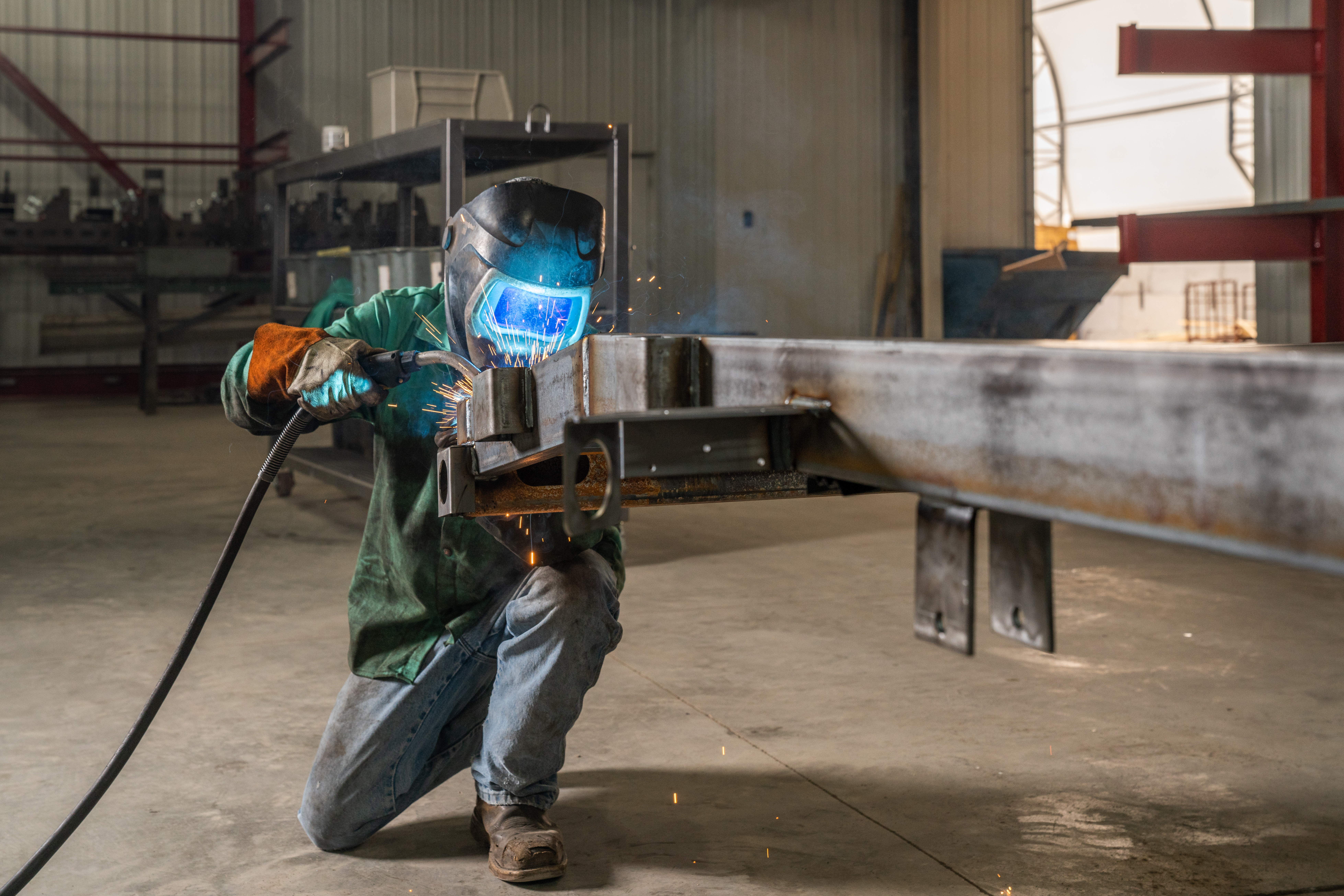
Mike also pointed out the impact of the Manufacturing Readiness Grants program on the company’s decision to move forward with the project. “It’s about more than just the money, it’s a good feeling for businesses to know that those resources are available to support them,” he said.
Rather than replacing its welders, Liberty Trailers upskilled its production staff to supervise and program the industrial robotics.
Employees who previously worked as welders at Liberty Trailers were provided training by the original equipment manufacturer (OEM) to learn how to maintain and program the robotic welding equipment. Yaskawa, the OEM, hosted manual welders at a 5-day training program at its U.S. headquarters. Mike stressed the importance of incorporating the existing workforce’s experience in welding principles into the programming, maintenance and quality monitoring of the robotic welding system. Mike said, “I encourage them to come back to Liberty Trailers after the training program and share that knowledge with their co-workers.” Similarly, the company’s engineers worked closely with American Welding and Gas during the software integration process.
“Indiana does a really good job at supporting all business–large and small. We [Liberty Trailers] know we need to become more competitive because we’re operating at a global scale. The fact that Indiana supports these technology adoption efforts is very important.”
Mike Teso
President at Liberty Trailers
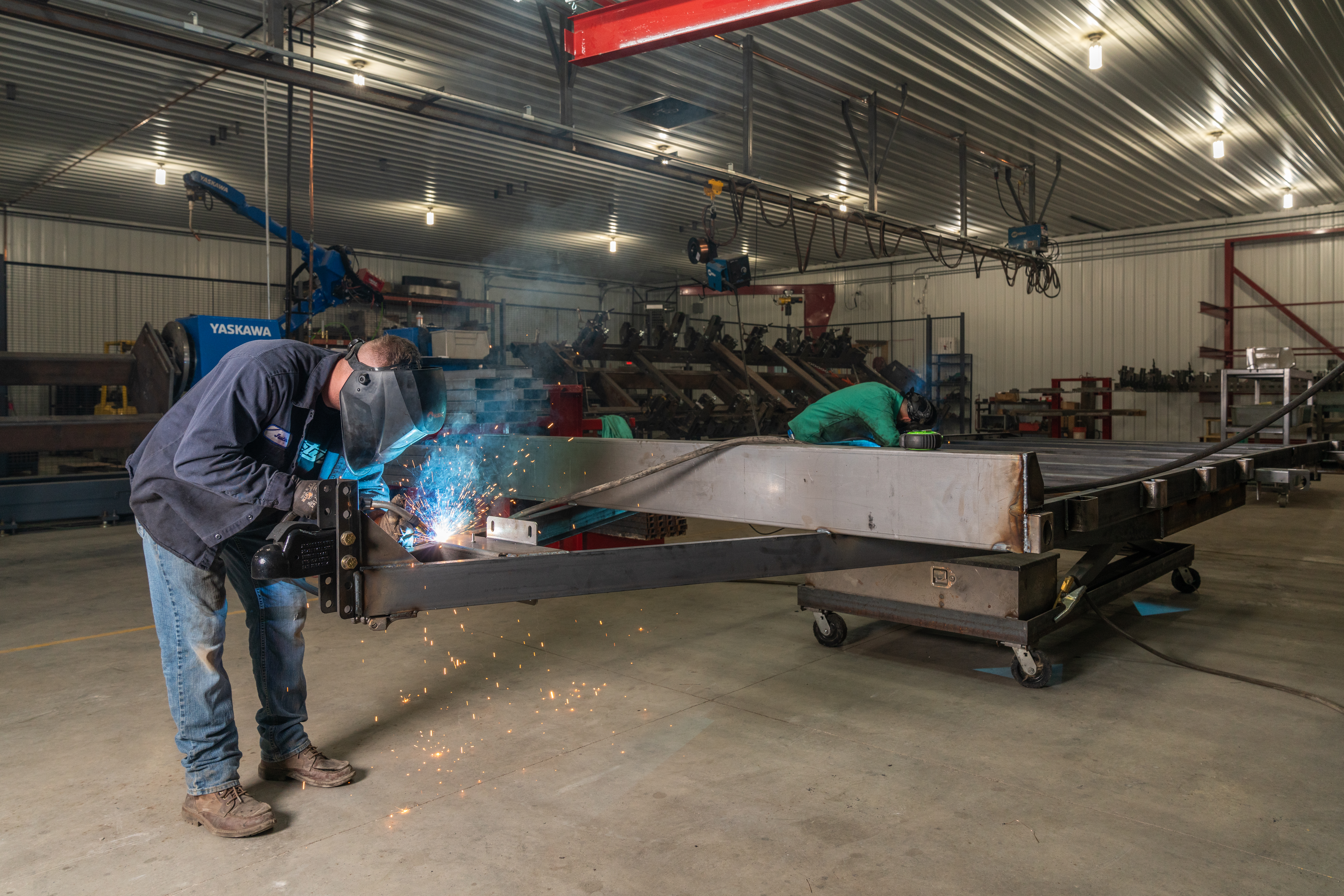